Werkstückbeispiele
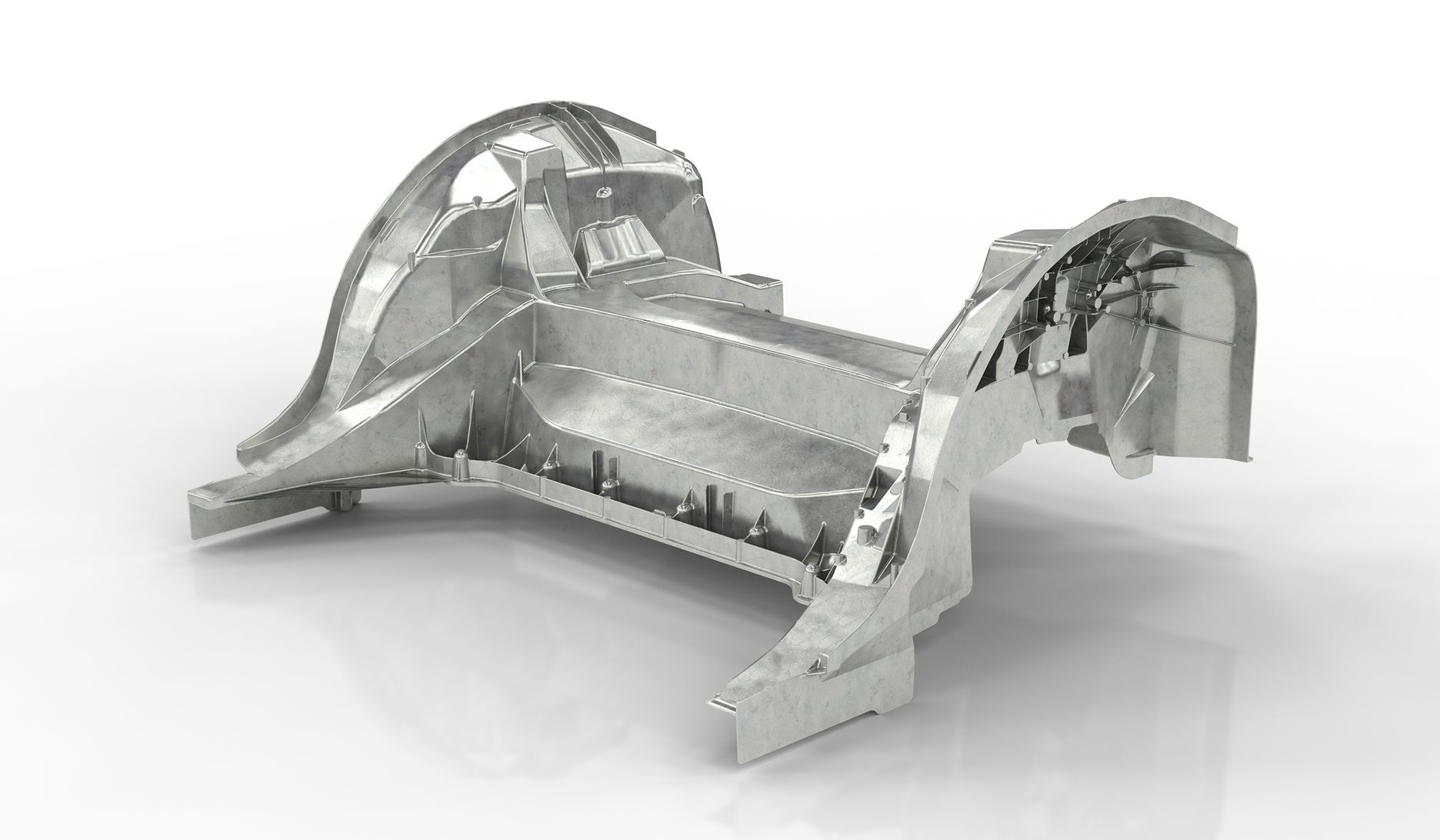
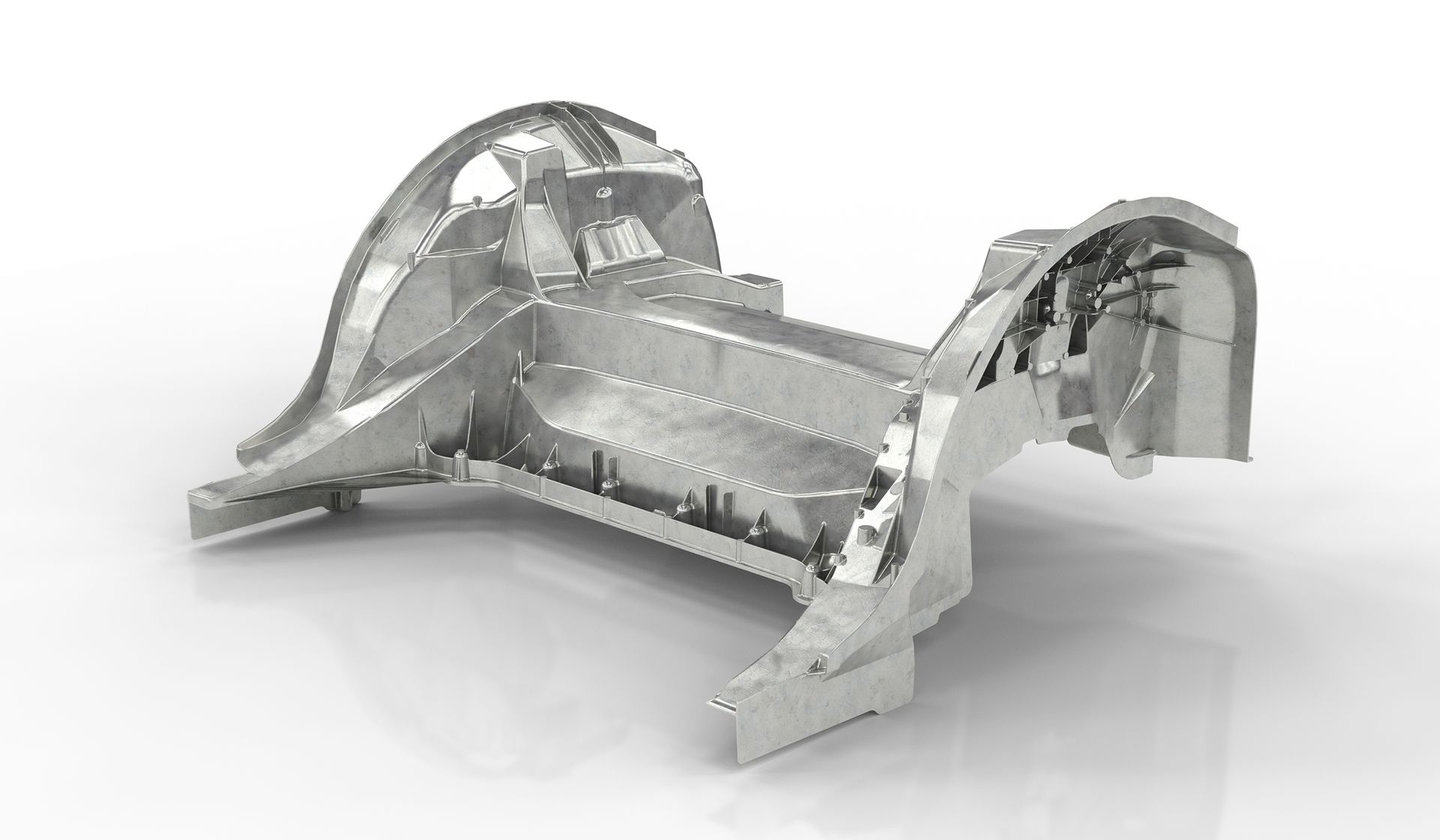
Machine concept
A solid welded machine bed forms the basis of the WH 10000. The two opposing machining units are mounted on the bed. Each machining unit (X, Y, Z) is equipped with a swivel head (B, C). The cradle bridge located in the centre serves as a workpiece carrier allowing the workpiece to be freely positioned in space. This enables machining from all sides in a single set-up. At the same time, it provides ample access for the operator and for loading and unloading. The position of the control cabinet can be freely selected according to the layout.
Optimal accessibility
- optimal view of the process through large safety windows
- one side of the machining centre can be used for automated loading: a large roller shutter opens the work area to the front and top for the use of robots and gantry systems
- maintenance area of the machine accessible through side doors
High frequency spindle with HSK-A 63 tool shank
- the WH 10000 combines two 5-axis machining units
- two spindles enable flexible machining from two sides
- the 4th and 5th axis are located in the tool, allowing various positions to be machined
An agile machining centre
- machine bed designed as a sturdy welded steel construction
- symmetrical design for thermal stability and optimum distribution of forces
- direct measuring systems in all axes
- use of a separate rotary axis for workpiece positioning enables machining in a single set-up
- ample access from two sides, separate for operator and automation
5-axis kinematics with horizontally arranged spindles
- machine bed supports the machining units as well as the NC cradle table
- machine unit moves in X-direction and supports the Y- and Z-axis
- compact swivel head with B- and C- axis guides the tool
- NC cradle table with counter bearing supports the workpiece and positions it in space
Roller-bearing linear guides and robust YRT bearing in the rotary axis
- linear axes with roller guides, driven by ground ball screws for high dynamics
- direct, absolute measuring systems for maximum precision and minimal positioning tolerances
- rotary axes A with large YRT bearing and automatic clamping for maximum stability and high tilting moment
Machining units
The swivel heads are rugged complete units from Benz. When machining structural components, the spindles must have a small interference contour while providing maximum rigidity, as long tools are often used for stepped machining and angular heads for hard-to-reach areas. All spindles are fully MQL compatible due to the special internal coolant supply.
Swivel head with HSK-A 63 tool shank
- maximum cutting performance due to compact overall design and robustly dimensioned spindle bearings
- permanent water cooling ensures thermal stability and precision
- rigid, ribbed guide carriage with high dynamic rigidity and damping
- small interference contour for perfect reach into the workpiece
- horizontal spindle for optimum chip fall
HELLER attachment head support (MSK)
- for the use of attachment heads, e.g. angular heads
- enlarged support basis with three-point rest
- integrated torque input and media transfer
Tool management
The machining of large structural components with complex shapes also requires very long tools. Therefore, the tool magazine can accommodate 51 tools with a maximum length of 450 mm. Tool change takes place directly during pick-up. Combined with high axis dynamics, this results in short chip-to-chip times.
Workpiece management
The machines from the WH 10000 series have been designed for table loading. The A-axis for workpiece positioning provides enough controlled lines for the use of automatic clamping fixtures and thus for fully automatic operation. Solutions for electronic signal transmission to the fixture are also available.
Easy automation and interlinking
- direct robot loading and unloading of the workpiece from the front
- direct top loading and unloading possible with gantry automation
- large roller shutter door provides ample access
- optimal integration into automation due to clear separation of loading side
Supply and disposal
Milling produces chips. And this is particularly true of the machining centres of the WH 10000 series: these extremely robust and reliable machining centres are made for production. To help you achieve consistent precision, we offer efficient evacuation solutions in all areas where chips are produced.
Media supply area on the sides of the machine
- easy maintenance with optimum accessibility
- all supply units visible a glance
- central oil-air lubrication for key components
- seal air and targeted blow-off of interfaces ensures long-term smooth machine operation
- media interface for hydraulic workpiece clamping
Effective tool cooling and work area extraction per spindle
- internal coolant supply (IKZ) through the tool and additional blow ring on the spindle
- proven Lubrix single-channel system incorporated as standard
- internal coolant supply (IKZ) with up to 3 pressure levels and variable lubricant content, freely programmable via NC program
Fast chip evacuation
- free chip fall below the spindle and quick evacuation from the work area
- central chip conveyor for quick disposal, optionally to the left or right
- scraper belt conveyor flanged directly to the machine bed to minimise space requirements
- inner work area panelling made of stainless steel for long term durability
Control technology
The WH 10000 is equipped with integrated absolute measuring systems in the NC axes. The state-of-the-art Siemens SINUMERIK ONE control ensures smooth operation and optimum operability of the machine. The machining centre uses digital drives and has a water-cooled control cabinet. For example, braking energy is fed back into the grid at a synchronised frequency to improve energy efficiency and performance.
Siemens SINUMERIK ONE
- main operating unit in ergonomic console-design
- optimally integrated and tailored to the requirements of HELLER machining centres
- digital drive technology and modern system architecture
- Profinet bus system for ultra-fast real-time communication
- IO-Link system for direct sensor diagnostics and parameterisation
- SINUMERIK Operate user interface for efficient machine operation
- HT 10 handheld operating unit
- console-style two-hand enable switch for easy start of e.g. clamping sequences from the loading side
Operation and maintenance
Every day you work with HELLER machines, you experience the depth of engineering experience built into these 5-axis machining centres. Key highlights of the WH 10000 include maximum user-friendliness during set-up and production, thanks to excellent visibility of the machining process, as well as easy access for maintenance.
Maximum ease of operation during set-up and production
- main operating unit in console-design for optimum ease of use
- excellent visibility into the work area thanks to large safety windows
- smooth-running work area door with linear guides for easy access to the work area
- LED lighting in the work area
- large multi-touch screen
- LED status lamp to indicate machining progress
Easy automation with robot and gantry
- wide, powered work area door designed as NC axis
Centralised media supply area at the side of the machine
- media supply and the process valves positioned on the side of the machine
- maintenance area located in the upper section of the machine, providing optimal access to the translational axes
Downloads
At a glance, our Download Centre offers an extensive range of information materials about our company, our products and services for you to download.
Contact
Contact
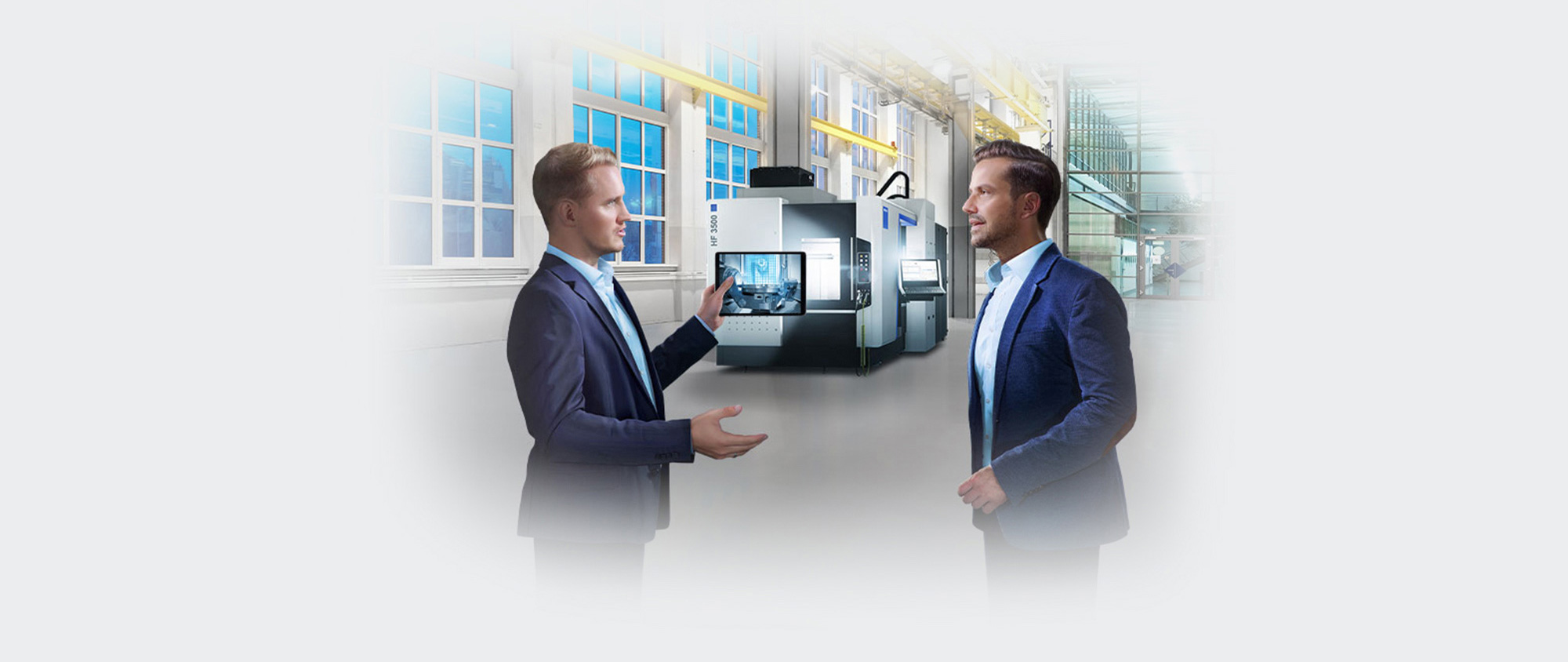
Sales & Services
Do you have questions about our products and services? Please get in touch with us, we are here for you! Benefit from our global HELLER network with knowledgeable sales and service contacts located in your region.
Find your nearest personal contact.
No results could be found.
You might also be interested in
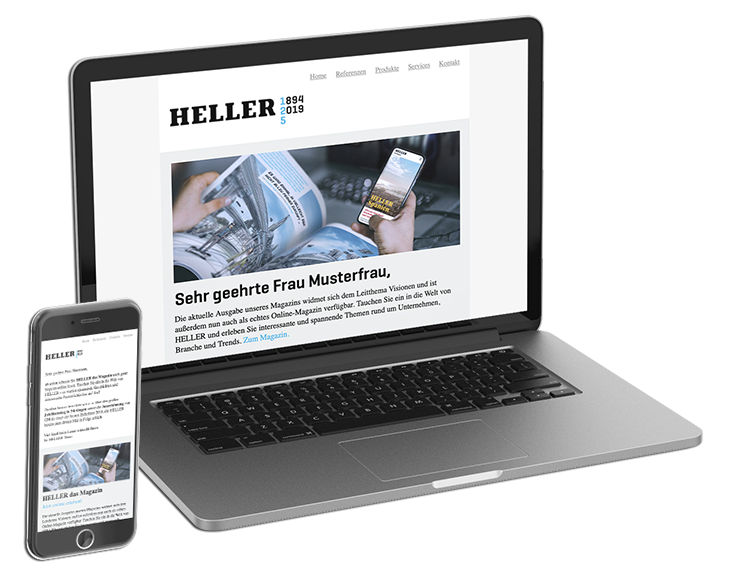
HELLER Newsletter
Register now!
The HELLER Newsletter provides you with information about all current topics concerning our company, our products and services as well as upcoming trade shows and events. Register now to make sure you never miss any news from the HELLER Group!