Crossbed and travelling column in gate design
- high stability and damping in the force flow through topology-optimised structural components in cast iron
- thermo-symmetrical design and optimised flow of forces
- a broad selection of robustly designed machining units
- a broad selection of tool magazine types: chain or rack
- tool changer with two NC axes for rapid, automatic tool change
4-axis kinematics with horizontally arranged spindle
- machine bed supports the X- and Z-axes in crossbed arrangement
- machine column moves in X direction and supports the machining unit
- machining unit moves in Y direction, compact and stably integrated in machine column
- rotary table moves in Z direction and performs feed motion
- NC rotary feed table (rotary axis B) turns the workpiece with continuous adjustment (360,000 x 0.001°)
Anti-friction linear guideways and stable YRT bearing in rotary table
- linear axes with roller guideways powered by ball screw drives for high feed forces
- direct absolute measuring systems (glass scales in linear axes) for maximum precision and low positioning tolerance
- equipment package SPEED available as an option for shortest idle times
- NC rotary feed table with large YRT bearing and automatic clamping for maximum stability and high tilting moments
- NC rotary feed table with gear unit for high circular milling torque and damping
- NC rotary feed table with direct drive for high dynamics and fast positioning (option for H 2000 and H 4000)
- good milling behaviour even in the upper stroke positions due to two ball screw drives in the Z-axis and optimum design of the drive train
Machining units
Spindles "made by HELLER" are among the highlights of our H-series 4-axis machining centres. Thanks to in-house production expertise, they guarantee you the highest possible machining quality and, above all, process stability and optimised performance in operation. A special benefit: The HELLER zero-spindle system. If the worst comes to the worst, the machining spindle can be replaced quickly and simply.
Robust machining units "made by HELLER"
- H 2000 – H 4000: 3 machining units with HSK-A 63 tool shank
- H 5000 – H 8000: 3 machining units with INLINE spindles and HSK-A 100 tool shank, 3 machining units with gearbox and HSK-A 100 tool shank
- H 10000 – H 16000: 5 machining units with HSK-A 100 tool shank
- compact overall design and robustly dimensioned spindle bearings for maximum cutting performance
- thermal stability and precision thanks to permanent cooling: precision cooling unit and thermal growth compensation of the spindle
- sturdy cast iron guide slide with high dynamic rigidity and damping
- slim spindle neck for perfect reach into the workpiece
- horizontal spindle for optimum chip fall
Quick and easy spindle exchange with cost advantages
- easy replacement without time-consuming tuning work due to spindle tuned to zero dimension
- maximum machine availability due to short repair times
- cost-effective solution for low TCO (Total Cost of Ownership)
- reduced spare parts costs due to the integrated zero spindle technology
HELLER attachment head support (MSK)
- for the use of attachment heads, e.g. angular heads
- enlarged support basis with three-point rest
- integrated torque input and media transfer
HELLER attachment head additional clamping*
- for additional clamping of attachment heads on the attachment head support
- optimum stability when using attachment heads and under high process forces
HELLER facing slide system
- for automatic adjustment of actuating tools
- actuation with a full-fledged NC axis (U) integrated in the machine control
- ideal for boring contours or facing work
- available for machining units with HSK tool shank
* not available for all machining units
Tool management
Short tooling times and short idle times – what you can rightly expect from our H-series 4-axis machining centres. The tool changer with two NC-axes achieves maximum precision and optimum movement sequence for short tool change times. The result, in combination with a high axis dynamic, is short chip-to-chip times.
Rapid tool provisioning
- 4 chain-type magazines with up to 240 positions for machines with HSK-A 63 (SK/BT)
- 3 chain-type magazines with up to 150 positions for machines with HSK-A 100 (SK/BT)
- rigid tool holder mounted on both sides of a double chain for optimised traversing dynamics
- tool provisioning during machining for short tool-to-tool times
- rapid tool change for short chip-to-chip times
- two NC axes with lifting/swivelling principle for high dynamics and constant precision
- stable double gripper for a secure hold with high tool weights and moments of weight
- tool shank in enclosed holders: protection against clogging and ideal holding during positioning
- workpiece loading station with optimum accessibility for ergonomic and rapid loading of tools
- integrated tool provisioning place for provision of next tool during machining and short tool-to-tool times
High storage capacity
- 1 rack-type magazine with 489 positions for machines with HSK-A 63
- 4 rack-type magazines with up to 425 positions for machines with HSK-A 100 (SK/BT)
- small footprint due to space-saving positioning of the magazine alongside the machine (H 2000 – H 8000)
- tool handling with highly dynamic loader for rapid tool provisioning
- rapid tool change for short chip-to-chip times
- two NC axes with lifting/swivelling principle for high dynamics and constant precision
- stable double gripper for a secure hold with high tool weights and moments of weight
- convenient operating panel at workpiece loading station
- workpiece loading station with integrated rotary station with several positions for tool loading during machining
Fast tool change for short chip-to-chip times
- two NC axes with lifting/swivelling principle for high dynamic and constant precision
- rigid double gripper for a secure hold with high weights and moments of weights
- tool shank in enclosed holders: protection against clogging and ideal holding during positioning
- tool setting station with optimum accessibility for ergonomic and fast tool setting
- integrated tool provisioning place for provision of next tool during machining and short tool-to-tool times
Ideal solution for the series production
- automatic pallet changer with lifting/swivelling principle
- high maximum load with robust, hydraulic drive
- optimised power grip at machine pallets due to fork shape of the lifting/swivelling traverse
- consistently high tool change accuracy with robust alignment elements and full blowing-off of functional surfaces
- machine pallets with DIN hole pattern and standardised alignment elements for rapid mounting of clamping fixtures
- hydraulic pallet clamping for a secure hold, even under high process forces
Pallet automation
- storage of machine pallets and automated loading of one or multiple machines
- standardised linear storage systems with up to 15 storage places depending on the type and size (option)
- everything from a single source: complete solutions for short installation time and commissioning
- specific advantages for production tasks with a large part mix and series production with small batch sizes
- optimal capacity utilisation with continuous pallet feed to one or multiple machines
- increased cost efficiency of the systems and more flexibility in production
Options
- standardised machine interface available for numerous machine sizes
- standardised host computer interface for optimal connection to the host computer
- high number of functions and options for automated production control
- media interface for hydraulic workpiece clamping
Workpiece automation
- automatic loading and unloading of workpieces in series production
- workpiece handling by robot relieves the operator
- automatic loading of pallets and fixtures as customer-specific solutions
- a perfect choice for series production with large batch sizes
- optimum capacity utilisation thanks to continuous stock feed
Options
- standardised machine interface for robot loading onto the setting station
- media interface for hydraulic workpiece clamping
- location check and unclamping check adjustable at main operating unit (IO link)
Supply and disposal
Any machine that mills will cause chip fall. And this is particularly the case with H-series 4-axis machining centres: Extremely resilient and reliable machining centres, these machines are made for production. To keep your results precise at all times, we have an efficient solution for disposal wherever chips accumulate.
Central media supply area on the rear of the machine
- easy maintenance with optimum accessibility, all supply units at a glance
- central oil-air lubrication for key components
- seal air and selective blow-off of interfaces for consistently smooth machine operation
- media interface for hydraulic workpiece clamping with up to 200 bar (option)
- compressed air and water gun integrated in the machine housing at workpiece loading station
Effective cooling lubricant supply and filtration
- coolant units: paper band filter or reversible flow filter with high tank volumes optionally available
- internal coolant supply (IKZ) through the tool with high-pressure 50 bar (option: 70 bar with frequency converter (FU))
- internal coolant supply with up to 7 pressure steps freely programmable via NC program
- external tool cooling with integrated spindle rinsing nozzles
- integrated work area shower with adjustable nozzles for optimum flushing of work area and cooling of workpiece
Options
- coolant cooler for high thermal stability and precision
- coolant tempering unit /on request
- automatic filling of the coolant unit
- oil skimmer for removing foreign oil from the cooling lubricant tank
- IKZ 70 bar with frequency converter (FU)
Rapid chip disposal
- H 2000 – H 6000: free chip fall below the spindle and fast disposal from the work area with central chip conveyor
- H 8000 – H 16000: chip disposal using spiral conveyors
- model: scraper or hinged belt conveyor (option), selectable depending on application
- work area flushing and shower support rapid chip removal in machines with coolant units
- extraction unit (option), supports rapid chip removal in machines with coolant units
- steep side panels and concertina covers with self-cleaning effect prevent chip deposits
Siemens SINUMERIK ONE
- H 2000 – H 8000: Siemens SINUMERIK ONE
- H 10000 – H 16000: Siemens SINUMERIK 840D sl
- main operating unit in console design, as standard on machine models H 2000 – H 8000*
- high-performance control for machining centres, meeting the highest standards of performance and machining precision
- optimally integrated and tailored to the requirements of HELLER machining centres
- digital drive technology and modern system architecture
- SINUMERIK Operate user interface for efficient machine operation
- HELLER Operation Interface for even greater ease of operation, as standard on machine models H 2000 – H 8000*
Fanuc 31i-B
- high-performance control for machining centres, meeting the highest standards of performance and machining precision
- operating elements optimally integrated into the machine’s main operating unit
- digital drive controller and modern system architecture
- iHMI operating software for machine models H 2000 – H 8000
- Screen Display Function operating software for machine models H 10000 – H 16000
- highest standards of precision and reliability
HELLER user interface with extended range of functions
- 4 functional areas for more information at a glance
- main operating unit in console design for optimum ease of operation on machines with Siemens control systems
- 24” screen and multi-touch function, ideal for displaying documents and drawings
- practice-oriented Xtends: HELLER extensions with additional functions
- machine control panel with pushbuttons and 3 overrides for optimum control in all operating situations
- third override reduces the rapid traverse speed, helping to eliminate the risk of a collision during manual operation
- H 10000 – H 16000: main operating unit in console design with 24” screen, multi-touch function and HELLER Operation Interface
- main operating unit in panel design (ITC 2400)
- convenient operating panel at the tool loading station
- HT 2 or HT 10 handheld operating unit
- additional keyboard
- work area camera
- in-process tool monitoring (IPM)
- damage reduction
- tool requirements planning
- automatic loading/unloading sequence
- maintenance manager
- job management
- interpolation turning (IPT)
- PRODUCTION-Assist
- HELLER Services Interface (HSI) and other HELLER4Industry products
* As standard for the machine models H 2000 – H 8000. For H 10000 – H 16000 optionally available.
Operation and maintenance
When you work with HELLER H-series machines, just how much machine construction has gone into these 4-axis machining centres will be tangible. No matter whether on the workpiece setting station, during tool loading, programming or maintenance – your comfort and safety and, above all, the productivity of your manufacturing facility is paramount at all times.
Maximum operating comfort during setting and production
- ergonomically arranged operating elements and control screens
- good view into the work area thanks to large safety screen
- smooth-running work area door with linear guide opens the work area roof in the operating area
- operating modes 2 and 3 included in standard scope of supply
Options
- handheld operating unit
- screen blow-off device for a clear view when machining with cutting fluid
Setting and loading during machining thanks to the pallet changer
- large smooth-running door to optimise access for loading and setting by crane or handling systems
- workpiece setting station, lockable at 90° indexing with foot unlocking mechanism, unrestricted manual rotation
- operating elements, as well as media guns within reach, integrated into the machine enclosure
Options
- automatically actuated setting station door
- automatically rotating NC setting station
- software options: automatic setting and de-setting sequence
Optimal accessibility for fast tool setting
- ergonomically arranged operating elements
- insertion location at optimum height and with integrated unclamping function for simple handling
- tool setting at the magazine when spindle is running
Options
- convenient operating panel at workpiece loading station
- setting during machining
- tool coding with RFID chip
- HELLER TRP (Tool Requirement Planning) for automatic creation of loading and unloading lists
Central supply area at the rear of the machine
- all supply units at a glance with good accessibility
- smooth-running doors and easily removal metal enclosure elements
- simple and direct access to the control cabinet
- quick-response HELLER spare part service
Options
- maintenance manager for maintenance planning and operator support on the machine itself
- HELLER TPS (Total Productive Services): Service Agreements for inspection, service and maintenance measures
Technical data
Product selection | H 2000 | H 4000 | H 5000 | H 6000 | H 8000 | H 10000 | H 14000 | H 16000 | ||
Positioning range
X/Y/Z | mm | 630/630/630 | 800/800/800 | 800/800/800 | 1,000/1,000/1,000 | 1,400/1,200/1,400 | 1,600/1,400/1,300 | 2,400/1,600/1,600 | 2,400/1,600/1,600 | |
Rapid traverse speed
X/Y/Z | POWER (SPEED) | m/min | 65 (80/80/90) | 65 (80/80/90) | 50 (65/65/72) | 50 (65/65/72) | 50 (60) | 45 | 41/45/45 | 41/45/45 | |
Acceleration
X/Y/Z | POWER (SPEED) | m/s² | 8 (10/10/12) | 8 (8/8/12) | 5 (7/7/10) | 5 (7/7/10) | 4 (5.5/6/6) | 4 | 3 | 3/3/2 | |
Positioning tolerance Tp / At1) X/Y/Z | VDI/DGQ 3441 / ISO 230 | POWER (SPEED) | mm | 0.005 | 0.005 | 0.005 | 0.008 | 0.008 (0.006) | 0.008 | 0.008 | 0.008 | |
Tool shank
SK/BT for selected units available as alternative | Size | HSK-A 63 | HSK-A 63 | HSK-A 100 | HSK-A 100 | HSK-A 100 | HSK-A 100 | HSK-A 100 | HSK-A 100 | |
Chip-to-chip time2) t₂,₃ | VDI 2852 | POWER (SPEED) | s | 2.5 (2.2) | 2.8 (2.3) | 3.4 (3.0) | 3.6 (3.2) | 4.6 (4.4) | 5.5 | 6.7 | 6.7 | |
Clamping surface
Nominal size | mm | 400 x 500 | 500 x 630 | 630 x 630 | 630 x 630 | 800 x 800 (1,000 x 1,000) | 1,000 x 1,000 | 1,000 x 1,000 | 1,250 x 1,600 | |
Workpiece dimension
Diameter x height | mm | Ø 720 x 850 | Ø 900 x 1,000 | Ø 900 x 1,000 | Ø 1,000 x 1,200 | Ø 1,400 x 1,500 | Ø 1,400 x 1,600 | Ø 1,400 x 1,800 | Ø 2,000 x 1,725 | |
Clamping load | kg | 800 | 1,400 | 1,400 | 1,400 | 2,000 | 4,000 | 4,000 | 8,000 | |
Machine control
Siemens SINUMERIK ONE / Siemens SINUMERIK 840D sl / Fanuc 31 i-B | ✓ / - / ✓ | ✓ / - / ✓ | ✓ / - / ✓ | ✓ / - / ✓ | ✓ / - / ✓ | - / ✓ / ✓ | - / ✓ / ✓ | - / ✓ / - |
( ) = optional values
- = not available
1) position uncertainty
2) applies to Siemens SINUMERIK
Downloads
At a glance, our Download Centre offers an extensive range of information materials about our company, our products and services for you to download.
Ready4productivity
Stock machines at a special price
Are you looking for a machining centre, but have no time to put up with long delivery times? Then we have the perfect solution for you: discover the 4-axis and 5-axis machining centres from our H and HF series available at short notice. Pre-configured and available in various specifications – for maximum efficiency and diverse production requirements.
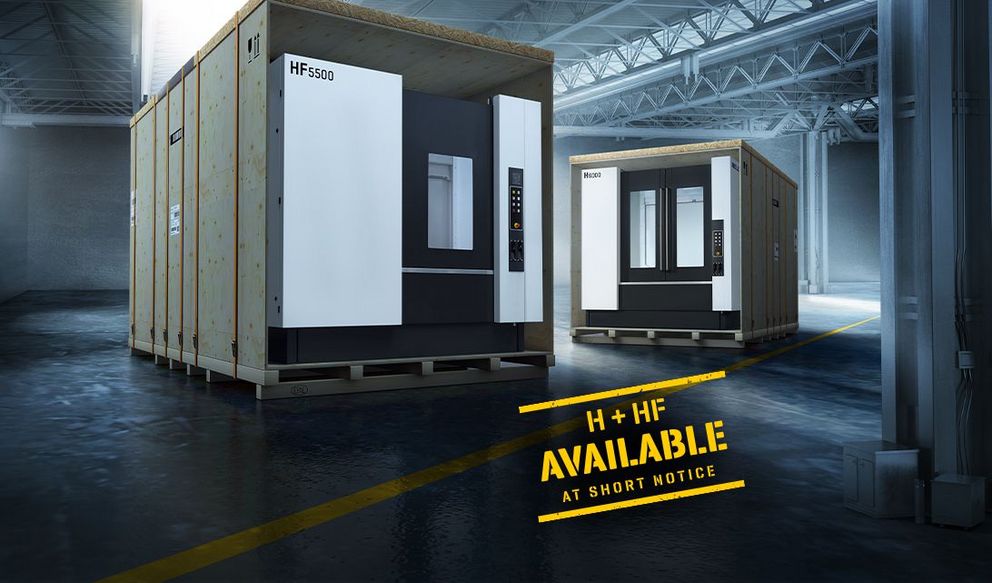
Ready4productivity
Stock machines at a special price
Are you looking for a machining centre, but have no time to put up with long delivery times? Then we have the perfect solution for you: discover the 4-axis and 5-axis machining centres from our H and HF series available at short notice. Pre-configured and available in various specifications – for maximum efficiency and diverse production requirements.
Contact
Contact
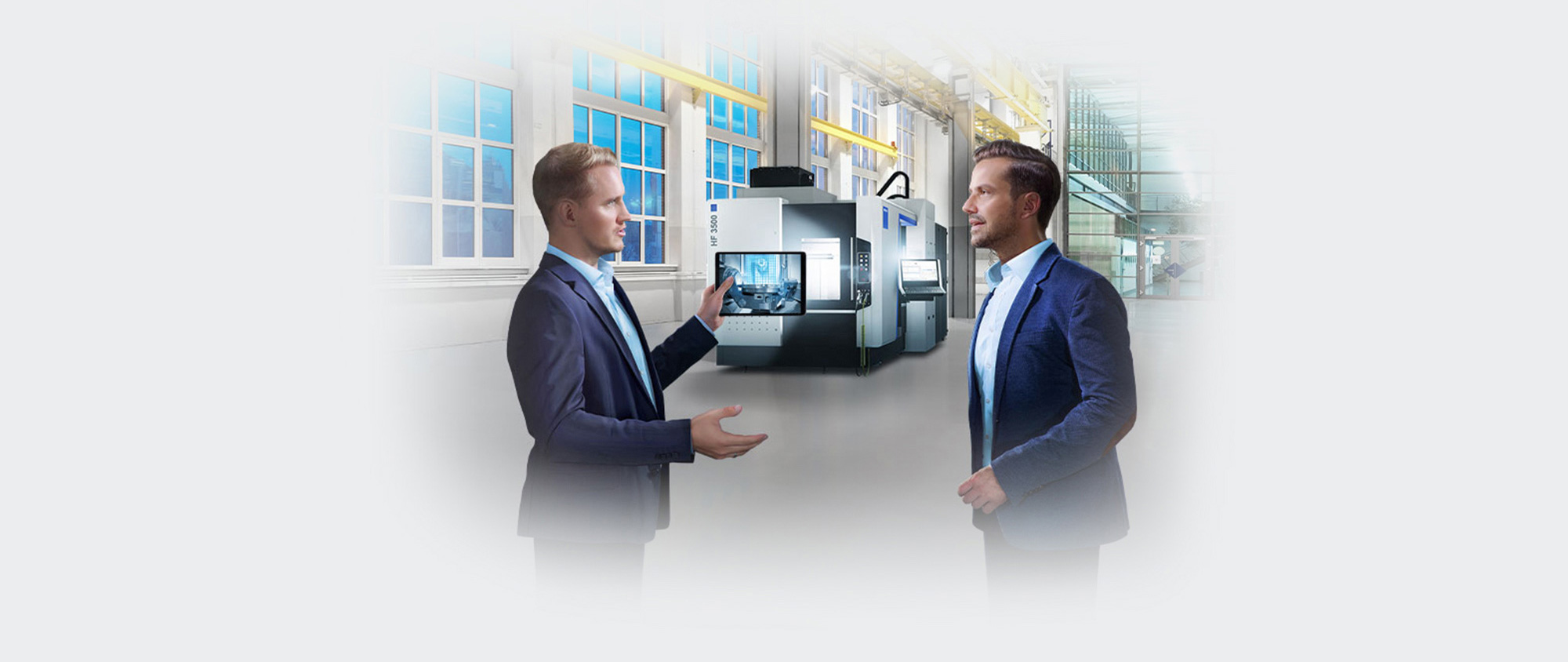
Sales & Services
Do you have questions about our products and services? Please get in touch with us, we are here for you! Benefit from our global HELLER network with knowledgeable sales and service contacts located in your region.
Find your nearest personal contact.
No results could be found.
You might also be interested in
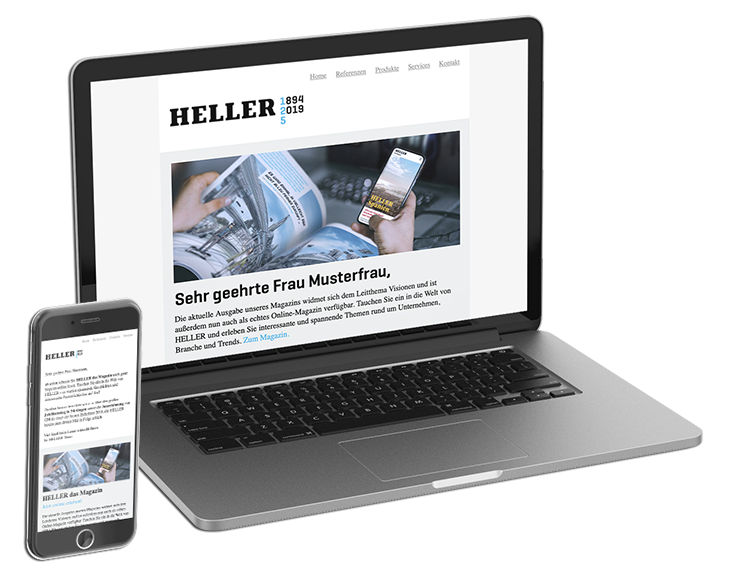
HELLER Newsletter
Register now!
The HELLER Newsletter provides you with information about all current topics concerning our company, our products and services as well as upcoming trade shows and events. Register now to make sure you never miss any news from the HELLER Group!