Machine concept
The HF-series 5-axis machining centres are the perfect combination of apparent contrasts - stiffness and dynamics. The basis is the rigid machine bed. Highly precise and fast machining cycles guarantee the unique machine structure of the HF: the fifth axis is located inside the workpiece, the directly-driven A/B-axis is supported by a counter-bearing.
Crossbed and travelling column in gate design
- rigid cast iron machine bed in combination with weight-optimised machine columns from steel
- horizontal spindle with lean spindle neck for perfect reach into the workpiece
- NC-rotary swivel table with counter bearing for optimum force flow and compact design
- gantry drive in Z axis (option) with two ball screw drives and two direct measuring systems
- chain-type or rack-type tool magazine for fast tool provisioning and high storage capacity
- tool changer with two NC axes for fast automatic tool change
- pallet changer with lifting/swivelling principle and robust HF pallet interface
- machine variant with table loading available as an alternative
5-axis kinematics with horizontal spindle and 5th axis in the workpiece
- machine bed carries the X- and the Z-axis in a cross bed arrangement
- the machine column traverses in the X-direction and carries the spindle unit
- machining unit moves in Y direction compact and stably integrated in machine column
- NC-rotary swivel table with counter bearing traverses in Z-direction and executes the feed movement
- NC rotary indexing table (B rotary axis) turns the workpiece continuously (360,000 x 0.001°)
- swivel table (A rotary axis) swivels the rotary table continuously (225,000 x 0.001°)
Anti-friction linear guideways and stable YRT bearings in the rotary axes
- linear axes with roller guides, driven by ball screws for a high dynamic
- direct, absolute measuring systems for optimised precision and low position tolerance
- highest dynamics of linear axis with the equipment package PRO (option)
- A and B rotary axes with large YRT bearings and automatic clamping for maximum stability and high tilting moments
- direct drives in both rotary axes for high dynamic
- swivelling NC rotary table with counter bearing and lowest moments of inertia for fast positioning
- gantry drive in Z axis (option)
Complete machining on a single machine
- NC rotary table version DDT (Direct Drive Turning), version DDTe (Direct Drive Turning enforced) optional for HF 5500
- tool shank HSK-T for optimum accuracy of turning operation
- spindle lock to ensure stable hold of the turning tools
- balancing technology cycle for balancing the workpieces and fixture in the machine
- Siemens NC turning cycles for simple programming of turning operations
Preconditions
- Enforced Drive in Z (option for POWER, included in PRO)
- Enforced Drive in A (option for POWER, included in PRO)
- installation with anchoring for optimum turning results
- Mill-Turn machine pallets with counter weight and swivel clamping system
- media interface with multi-line clamping technology for mill-turn operations at 80 bar
- tool measurement with high precision laser and probe for turning tools
- oscillating speed: technology cycle to eliminate vibration in critical processes
- ChipBreak: technology cycle to prevent long chips and thread chips
Machining units
5-axis machining requires all components of a machining centre to deliver a top performance. The spindle must be particularly efficient: highly flexible, with torque characteristic curve adapted for the task in hand and suitable for a range of materials. The HF-series 5-axis machining centres offer seven robust and powerful versions, so you work with a spindle that best suits your requirements.
Robust machining units "made by HELLER"
- 7 spindles to choose from, with the new dynamic cutting spindles (DC 63 i and DC 100 i ) perfect for universal use
- tool shank HSK-A 63 or HSK-A 100 optionally available for both machine sizes
- maximum performance in operation with compact overall dimensions and robustly dimensioned spindle bearing
- thermal stability and precision thanks to continuous cooling: precision cooling unit and spindle thermal growth compensation
- rigid cast iron guide slide with high dynamic rigidity and damping
- slim spindle neck for perfect reach into the workpiece
- horizontal spindle for optimum chip fall
Quick and easy spindle exchange with cost advantages
- easy replacement without time-consuming tuning work due to spindle tuned to zero dimension
- maximum machine availability through short repair times
- cost-effective service solution for low TCO (Total Cost of Ownership)
HELLER torque support
- absorbs the torque generated on the tool
HELLER attachment head support (MSK)
- for the use of attachment heads, e.g. angular heads
- enlarged support basis with three-point rest
- integrated torque input and media transfer
HELLER facing slide system
- for automatic adjustment of actuating tools
- actuation with a full-fledged NC axis (U) integrated in the machine controller
- ideal for boring contours or facing work
Tool management
If you have to work with a broad range of tools and respond flexibly to new production requirements, our HF-series 5-axis machining centres are the ideal solution for you. Powerful tool magazines and a precise high-speed tool changer for optimum chip-to-chip times guarantee you constantly short non-productive times.
Rapid tool provisioning
- 4 chain-type magazines with up to 240 positions for machines with HSK-A 63
- 3 chain-type magazines with up to 150 positions for machines with HSK-A 100
- double chain with high traversing dynamic and rigid tool holders mounted on both sides
- short tool-to-tool times achieved through tool provisioning during machining
- convenient operating panel at the tool loading station (option)
- tool loading station with optimum ergonomic design
High storage capacity
- 3 rack-type magazines with up to 340 positions for machines with HSK-A 100
- 2 rack-type magazines with up to 489 positions for machines with HSK-A 63
- small footprint due to space-saving positioning of the magazine alongside the machine
- fast tool handling with highly dynamic NC loader
- tool provisioning place for an optimised tool change process
- convenient operating panel at the tool setting station
- tool setting station with integrated rotary station with multiple locations for setting during machining
Fast tool change for short chip-to-chip times
- two NC axes with lifting/swivelling principle for high dynamic and constant precision
- rigid double gripper for a secure hold with high weights and moments of weights
- tool shank in enclosed holders protects against contamination and optimum hold during positioning
- tool setting station with optimum accessibility for ergonomic and fast tool setting
- integrated tool provisioning place for provision of next tool during machining and short tool-to-tool times
Workpiece management
No matter whether with pallet changer or as table loading – HF-series 5-axis machining centres are best prepared for both feeding concepts. Various table sizes or pallet dimensions and numerous options to suit different sizes. So you can configure the machine to suit your specific requirements.
Optimal for series production
- automatic pallet changer with lifting/swivelling principle
- high maximum payload with robust, hydraulic drive
- secure force application on machine pallets via HF interface with integrated pallet pick-up check
- continuously high changeover accuracy through integrated zero point pallet clamping system
- high process reliability thanks to integrated pallet location check (option)
- machine pallets with DIN hole pattern and standardised aligning elements for fast mounting of clamping fixtures
Optimal for workshop use
- workpieces loaded onto the machine table in the work area itself
- wide, smooth-running work area door opens the work area roof for crane loading
- short distance to the workpiece thanks to inclined protective enclosure
- additional loading stroke for the table in in the Z-axis
- easy to automate with interchangeable pallet (option)
- round machine table with large clamping surface and DIN hole pattern
- optimum accessibility to the workpiece thanks to low "loading edge"
NC swivelling rotary table with counter bearing as standard
- directly driven rotary axes A and B with high dynamics
- large YRT bearings for maximum stability and high tilting moments
- integrated automatic fail-safe clamping for high tangential moments in high performance machining
- fast positioning due to minimal moment of inertia
Options
- integrated media interface for hydraulic workpiece clamping with 80 or 200 bar pressure and multi-line clamping technology
- additional pneumatic functions: support control and release control via media interface
- automatic door at setup station
- DIN T-slot design
Pallet automation
- storage of machine pallets and automated loading of one or multiple machines
- standardised linear storage systems with up to 15 storage places depending on the type and size (option)
- everything from a single source: complete solutions for short installation time and commissioning
- specific advantages for production tasks with a large part mix and series production with small batch sizes
- optimal capacity utilisation with continuous pallet feed to one or multiple machines
- increased cost efficiency of the systems and more flexibility in production
Options
- standardised machine interface available for numerous machine sizes
- standardised host computer interface for optimal connection to the host computer
- high number of functions and options for automated production control
- media interface for hydraulic workpiece clamping
Workpiece automation
- automatic loading and unloading of workpieces in series production
- workpiece handling by robot relieves the operator
- automatic loading of pallets and fixtures as customer-specific solutions
- a perfect choice for series production with large batch sizes
- optimum capacity utilisation thanks to continuous stock feed
Options
- standardised machine interface for robot loading onto the setting station
- media interface for hydraulic workpiece clamping
- location check and unclamping check adjustable at main operating unit (IO link)
Supply and disposal
Thermal stability is one of the decisive factors for reliable and highly-precise machining processes. The heat input into the machine structure and workpiece as a result of hot chips can impair accuracy. Our aim is therefore: fastest-possible chip disposal and coolant supply directly through the spindle.
Central media supply area on the rear of the machine
- easy maintenance with optimum accessibility, all supply units at a glance
- central oil-air lubrication for the key components
- seal air and selective blow-out of interfaces for permanently smooth machine operation
- media interface for hydraulic workpiece clamping with up to 200 bar (option)
- compressed air and flushing gun at the workpiece setting station integrated into the machine enclosure
Efficient cooling lubricant supply and filtration
- coolant units: Paper band filter or reversible flow filter with high tank volumes optionally available
- internal coolant supply through the tool with high-pressure 50 bar (optional: 70 bar)
- internal coolant supply with up to 7 pressure stages freely programmable via the NC program
- external tool cooling with multiple integrated spindle flushing nozzles
- integrated work area shower with adjustable nozzles for optimum flushing of work area and cooling of workpiece
Options
- coolant cooler
- coolant temperature control for high thermal stability and precision
- automatic filling of the coolant unit
- oil skimmer for removing foreign oil from the cooling lubricant tank by oil separation
Rapid chip disposal
- free chip fall below the spindle and rapid removal from work area
- central chip conveyor for rapid disposal to the rear
- model: scraper or hinged belt conveyor (option), selectable depending on application
- work area flushing and work area shower support fast chip disposal for machines with coolant units
- extraction unit (option) for extraction of cooling lubricant from the work area
- steep side walls and stainless steel lamella covers with self-cleaning effect prevent chip deposits
- interior work area enclosure made from electrolytically galvanized sheets provides long-term resistance against dirt and coolant
Control technology
Speed is always of the essence during the daily working routine. The Siemens SINUMERIK ONE, a state-of-the-art high-performance controller with HELLER Operation Interface, makes your work easy through efficient support: with intuitive operation, simple programming, cycle support and all important information at a glance.
Siemens SINUMERIK ONE
- high-performance control Siemens SINUMERIK ONE to meet the highest standards of performance and machining precision
- main operating unit in console-design and ergonomic control panels around the machine
- optimally integrated and selectively matched to the requirements of HELLER machining centres
- digital drive technology and modern system architecture
- Profinet bus system for fastest possible real-time communication
- IO-Link for direct diagnostics and parametrisation of sensors
- SINUMERIK Operate user interface for efficient machine operation
HELLER user interface with extended range of functions
- 4 functional areas for more information at a glance
- 24“ screen and multi-touch function, ideal for displaying documents and drawings
- practical Xtends: HELLER extensions with additional functions
- machine control panel with pushbuttons and 3 overrides for optimum control in all operating situations
- third override reduces rapid traverse speed, helping to eliminate the risk of a collision during manual operation
- convenient operating panel at the tool loading station
- HT 2 or HT 10 handheld operating unit
- additional keyboard
- work area camera
- in-process tool monitoring (IPM)
- damage reduction
- tool requirements planning
- automatic loading/unloading sequence
- maintenance manager
- job management
- interpolation turning (IPT)
- PRODUCTION-Assist
- HELLER Services Interface (HSI) and other HELLER4Industry products
Operation and maintenance
When you work with HELLER HF-series machines, just how much machine construction has gone into these 5-axis machining centres will be tangible. No matter whether on the workpiece setting station, during tool loading, programming or maintenance – your comfort and safety and, above all, the productivity of your manufacturing facility is paramount at all times.
Maximum operating comfort during setting and production
- main operating unit designed as a console for optimum operating comfort
- good view into the work area thanks to large safety glass
- smooth-running work area door with linear guide opens the work area roof in the operating area
- operating modes 2 and 3 included in standard scope of supply
- LED work area lighting (blue/white, adjustable)
- 24“ screen with multi-touch function and HELLER Operation Interface
- double rotatable main operating unit designed as console
- additional holder for flushing gun within reach, integrated into the machine enclosure
- work-cam: work area camera to display on the main operating unit
Options
- hand-held operating unit HT 2 or HT 10
- screen blow-off device for a clear view when machining with cutting fluid
- LED status lamp with machining progress display
Setting and loading during machining thanks to the pallet changer
- large, smooth-running setting station door with large viewing panel
- optimum accessibility for loading and setting work with crane or handling systems
- workpiece setting station lockable with 90° increments, with foot unlocking mechanism
- operating elements as well as media guns within reach, integrated into the machine enclosure
- low "loading edge" and short distance to the pallet
Options
- automatically actuated setting station door
- automatically rotatable NC setting station
- automatic flushing workpiece setting station
- automatic loading sequence
- automatic desetting sequence
Optimal accessibility for fast tool setting
- tool setting during spindle operation for more flexibility
- ergonomically arranged operating elements and operating unit with touch function
- insertion location at optimum height and with integrated unclamping function for simple handling
- LED lighting at the tool setting station (blue/white, adjustable)
Options
- convenient operating panel at tool loading station
- loading during machining (HZPR)
- tool coding with RFID chip
- tool requirement planning (TRP) for automatic creation of loading and unloading lists
Central supply area at the rear of the machine
- all supply units at a glance with good accessibility
- easily removal metal enclosure elements for fast access to the maintenance points
- control cabinet with smooth running, lockable doors
- quick-response HELLER spare part service for optimum supply of genuine spare parts
Options
- maintenance manager for maintenance planning and operator support on the machine itself
- HELLER TPS (Total Productive Services): service contracts for inspection, service and maintenance measures
Technical data
Product selection | HF 3500 | HF 5500 | |||||
Positioning range
X/Y/Z | mm | 710/750/710 | 900/950/930 | ||||
Rapid traverse speed
X/Y/Z | POWER (SPEED) (PRO) | m/min | 65 (90/90/80) (90/90/80) | 65 (90/90/80) (90/90/80) | ||||
Acceleration
X/Y/Z | POWER (SPEED) (PRO) | m/s² | 8 (10/10/8) (10/10/10) | 8 (10/10/8) (10/10/10) | ||||
Positioning tolerance Tp / At1) X/Y/Z | VDI/DGQ 3441 / ISO 230 | POWER (SPEED) (PRO) | mm | 0.005 (0.005) (0.004) | 0.005 (0.005) (0.004) | ||||
Tool shank | Size | HSK-A 63 | (HSK-A 100) | HSK-A 63 | (HSK-A 100) | ||
Chip-to-chip time
t₂,₃ | VDI 2852 | POWER (SPEED) (PRO) | s | 2.6 (2.4) (2.4) | (3.2 (3.0) (3.0)) | 2.7 (2.5) (2.5) | (3.3 (3.1) (3.1)) | ||
Type | Pallet changer | Table loading | Pallet changer | Table loading | |||
Clamping surface
Nominal size | mm | 400 x 500 | Ø 630 (Ø 710)2) | 500 x 630 | Ø 810 (Ø 880)2) | ||
Workpiece dimension
Diameter x height | mm | Ø 7103) x 630 | Ø 710 x 690 | Ø 9003) x 800 | Ø 900 x 870 | ||
Clamping load
POWER (SPEED) (PRO) | kg | 550 (550) (650) | 550 (550) (650) | 750 | 750 | ||
Machine control | Siemens SINUMERIK ONE | Siemens SINUMERIK ONE |
( ) = optional values
- = not available
1) position uncertainty
2) clamping plate
3) consider limitations
Downloads
At a glance, our Download Centre offers an extensive range of information materials about our company, our products and services for you to download.
Ready4productivity
Stock machines at a special price
Are you looking for a machining centre, but have no time to put up with long delivery times? Then we have the perfect solution for you: discover the 4-axis and 5-axis machining centres from our H and HF series available at short notice. Pre-configured and available in various specifications – for maximum efficiency and diverse production requirements.
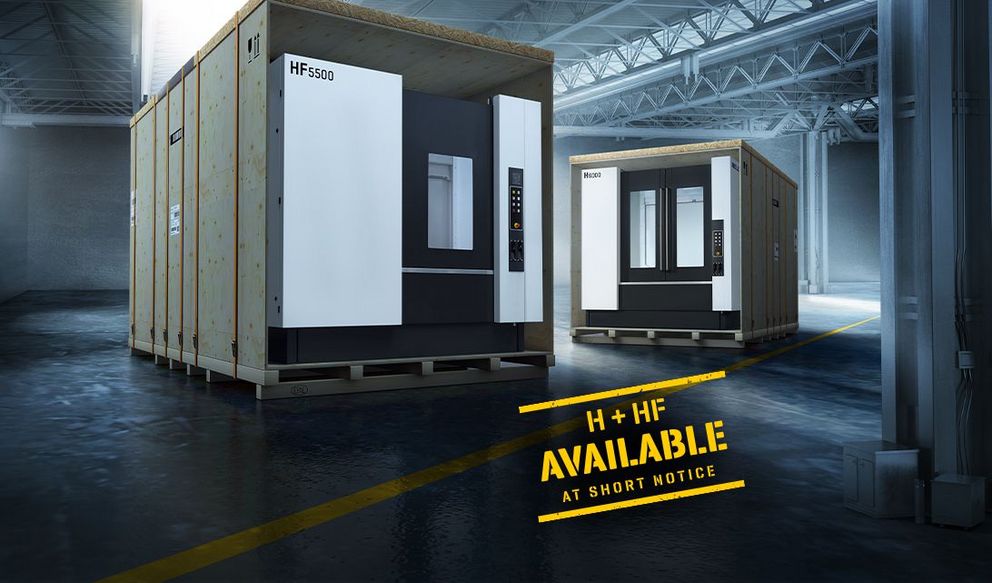
Ready4productivity
Stock machines at a special price
Are you looking for a machining centre, but have no time to put up with long delivery times? Then we have the perfect solution for you: discover the 4-axis and 5-axis machining centres from our H and HF series available at short notice. Pre-configured and available in various specifications – for maximum efficiency and diverse production requirements.
Contact
Contact
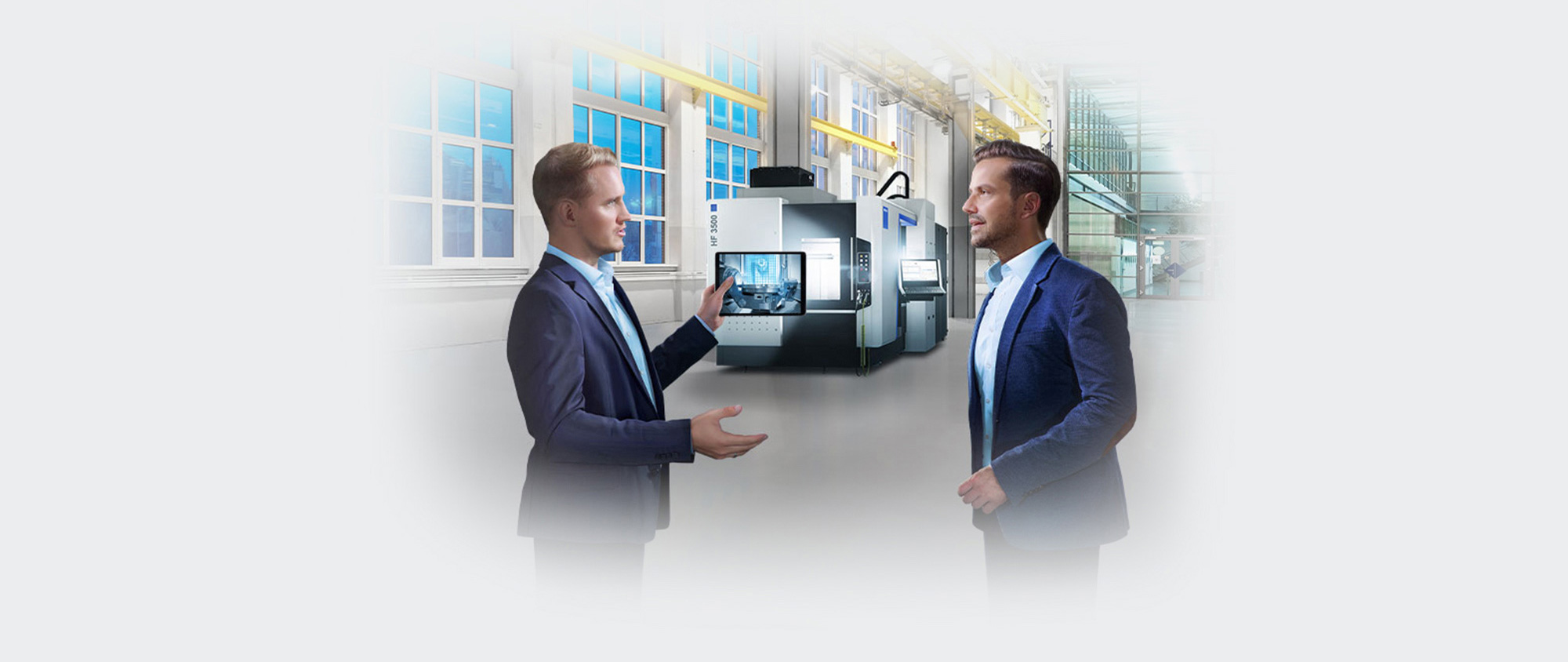
Sales & Services
Do you have questions about our products and services? Please get in touch with us, we are here for you! Benefit from our global HELLER network with knowledgeable sales and service contacts located in your region.
Find your nearest personal contact.
No results could be found.
You might also be interested in
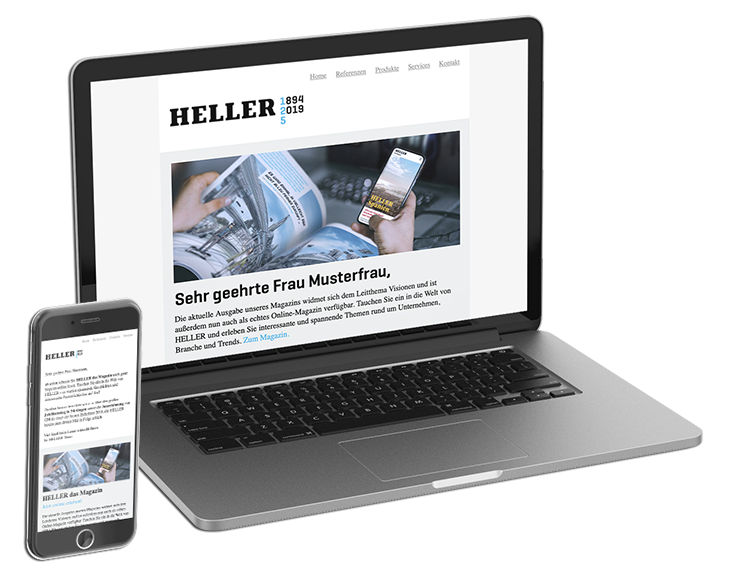
HELLER Newsletter
Register now!
The HELLER Newsletter provides you with information about all current topics concerning our company, our products and services as well as upcoming trade shows and events. Register now to make sure you never miss any news from the HELLER Group!