A shared philosophy
for the perfect picture
TEXT Lukas Schult
Every photographer and camera enthusiast should know the small town of Feltre in Northern Italy in the province of Belluno. Not only because the historic upper part of the town is picturesquely nestled into a hillside and located in a gorgeous, lush valley on the foothills of the Dolomites. It is also home to one of the world’s most renowned manufacturers of camera accessories. For 45 years, the company Manfrotto, now Vitec Imaging Solutions, has been synonymous with highest quality in the production of camera tripods and other accessories for photo and video production. For ten years now, Andrea De Danieli has been the Head of Industrial Engineering and Facilities in Feltre, employing approx. 400 staff producing all key components of tripods in a wide range of different sizes. However, this supposedly simple product does not only comprise countless individual parts, but also requires extensive know-how, innovative spirit and a charismatic tinkerer, who is responsible for a total of seven production workshops covering 40,000sqm floorspace, to which a HELLER HF 3500 was added last year.
The Pioneering Lab as a factory into the factory
At the beginning of 2018, the people at Vitec Imaging Solutions decided to set up a Pioneering Lab, a dedicated area for manufacturing the latest developments for testing at the customers. “It took us four months to clear, refurbish and set up the hall,” explains Andrea De Danieli, who was the originator of the project. “In here, we produce new products and developments in small volumes which we will then test in the market. We see the lab as a mixture of prototype construction and series production. It practically is a factory within the factory that operates independently of the rest of the production,” De Danieli continues. The graduate electronic engineer will eagerly and enthusiastically show people visiting the facilities around his department and they will realise immediately that the company develops and produces high-tech equipment at the factory. The innovative spirit can be felt throughout the hall. High, light-coloured walls, shiny white floors, ample space to experiment and in the centre of it, the HELLER 5-axis machining centre model HF 3500. These are the ingredients for the tripod pioneers at Vitec Imaging Solutions. “Everything was new to us. This area was supposed to be completely different from the others, the strategy was new to us and so was 5-axis machining. However, it all fell into place perfectly,” says De Danieli.
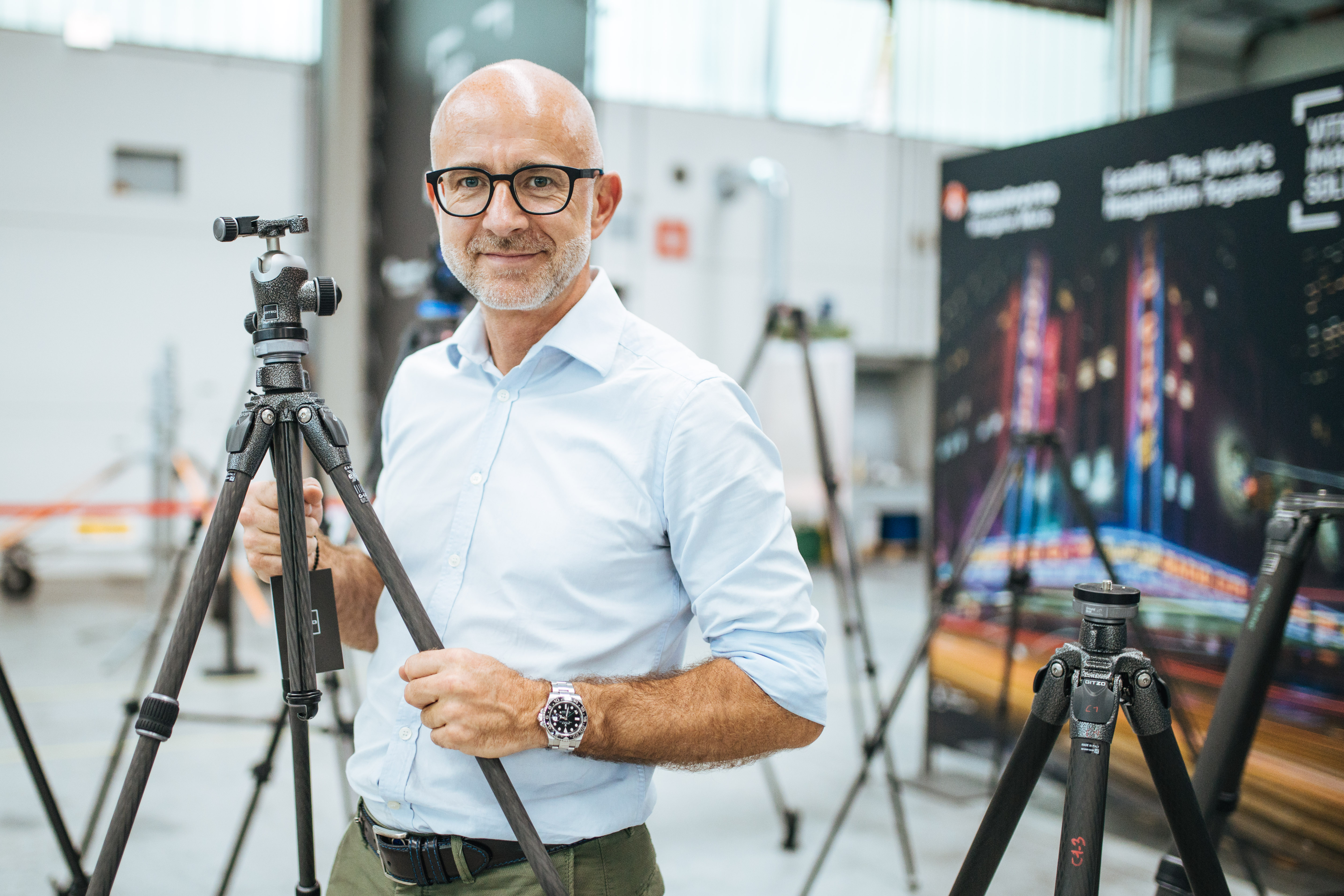
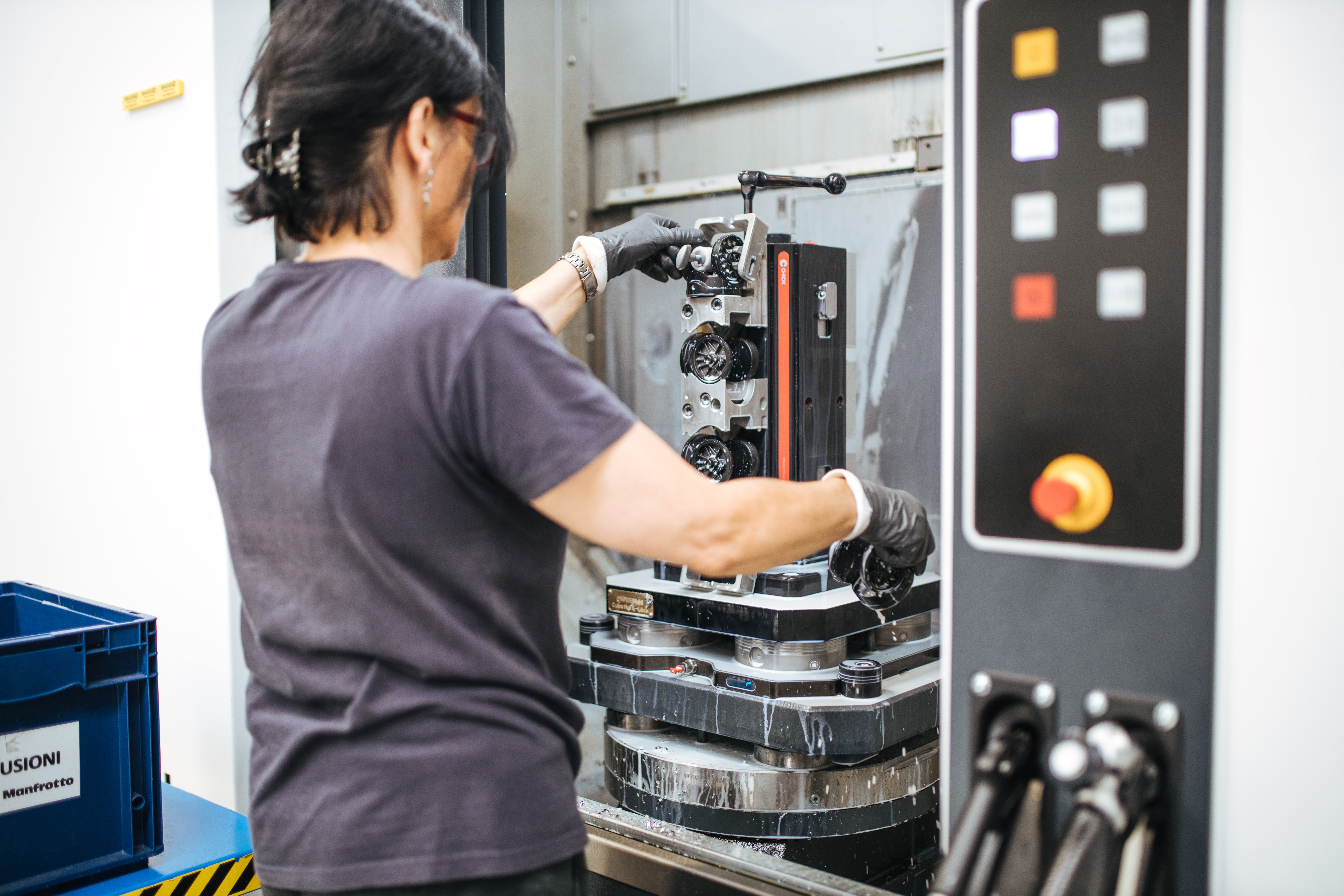
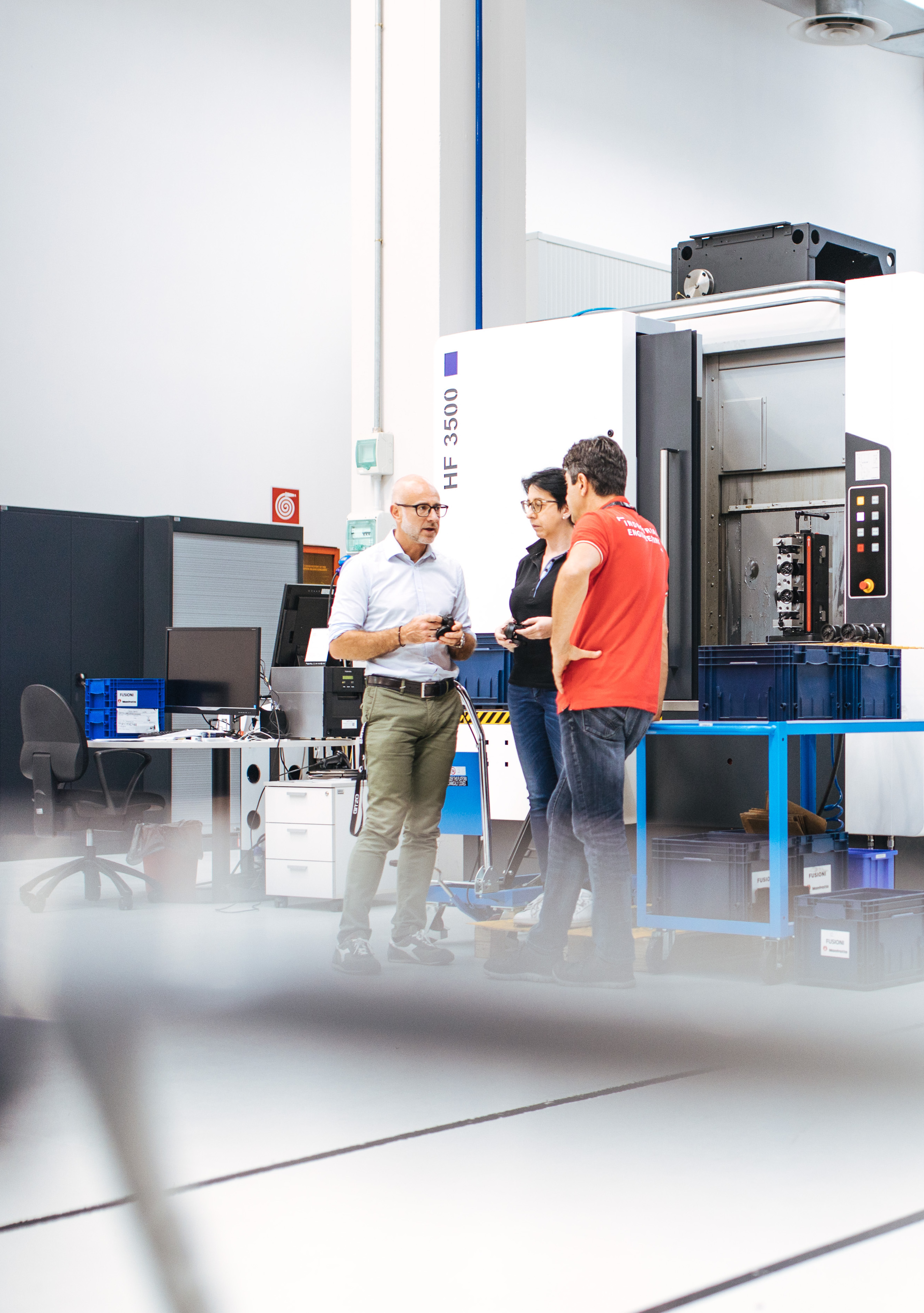
The HF 3500 provides a highly productive overall package
The HF on site is used for the production of the first two different products that subsequently have to undergo market testing. In the first six months, for instance, the company machined an innovative camera head at the facility in a volume of 3000 pieces. The machine in Feltre is equipped with a pallet changer and a rotary load/unload station with CAD/CAM technology and a Balluff sensor system for automatic tool recognition. The motor spindle with HSK-A63 spindle taper provides 47kW drive power, 100Nm of drive torque and generates a speed of 18,000rpm. Moreover, the torque drives in the A axis and C axis equipped with counter bearings ensure the machine’s high level of productivity. The tool magazine of the HF 3500 at Manfrotto has 80 storage places.
What convinced De Danieli was not the feedback from other Italian users, but a visit to HELLER in Nürtingen, Germany. “What sparked my enthusiasm was the ‘HELLER made by HELLER’ concept that matches our philosophy.” Anyone who talks to Vitec Imaging Solutions’ ‘Gyro Gearloose’ will know immediately why the concepts are such a good match. The Engineering Manager is an inventor and developer of complex production machines himself. His machines are used in the cutting of the tripod legs and the painting of the finish-machined parts. “We plan, design and manufacture our own machines for production. That is a major competitive advantage of ours and I am convinced that it is extremely important for our status as a leading innovator,” he explains. Therefore, the engineer is very discerning when it comes to buying new machines. “The HELLER machine is a highly precise machine, guaranteeing the highest quality, also for our customers.” And if ever service support is needed, the HELLER RDS remote diagnostics included in the package ensures quick troubleshooting and fault rectification.
De Danieli is what would these days be called an innovator. He travels widely throughout the world, always looking for new trends and technological developments. Although he is not a member of the R&D team, his opinion is heard and greatly valued. “I am always involved in the brainstorming sessions of our R&D department,” says the tinkerer who – what is hardly surprising – is a major photo enthusiast himself. At the beginning of his 20s, he started photography as a hobby. Only ten years ago, when he came to Manfrotto, he became involved in photography on a professional level. “My job has given me the opportunity to meet the most important and best-known photographers in the world and to go on a photo tour with them. That has been a really unique experience.” As a result, the feedback received from customers can be directly incorporated into production. After all, there are high requirements on tripods. They have to ensure high stability and low vibration in order to guarantee perfect picture quality. This absolute requirement on highest quality fits in perfectly with HELLER’s goal to always offer customers the best and highest-quality solution for their individual manufacturing tasks. Translating this into steel, iron or carbon is more than just work to Andrea De Danieli: to him, it is sheer passion. “I don’t like my job, I love it.”