for machining centres
TEXT Peter Klingauf
PHOTOS Jens Gelowicz, Jürgen Altmann
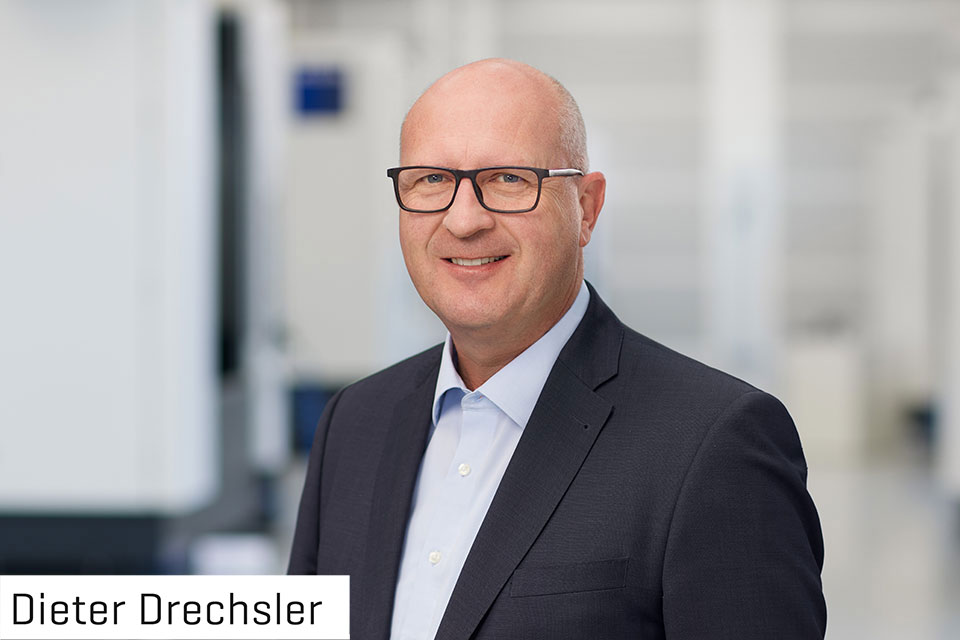
How can we make our machining centres even more efficient? – a question that is constantly on the minds of the HELLER product managers. One key to higher productivity is complete machining on a single machine. “This is exactly what we are working on,” says HELLER Managing Director Dieter Drechsler: “We keep our ears close to our customers and know how important it is to finish-machine components in one setup.” Therefore, the HELLER engineers are in the process of integrating various technologies into the current line of machining centres. In addition to turning operations and methods for gear cutting, the portfolio has now been expanded by friction stir welding. HELLER also develops complementary processes beyond the machining centre: a coating module for cylinder surfaces of smaller powertrains is about to be launched on the market.
How can we make our machining centres even more efficient? – a question that is constantly on the minds of the HELLER product managers. One key to higher productivity is complete machining on a single machine. “This is exactly what we are working on,” says HELLER Managing Director Dieter Drechsler: “We keep our ears close to our customers and know how important it is to finish-machine components in one setup.” Therefore, the HELLER engineers are in the process of integrating various technologies into the current line of machining centres. In addition to turning operations and methods for gear cutting, the portfolio has now been expanded by friction stir welding. HELLER also develops complementary processes beyond the machining centre: a coating module for cylinder surfaces of smaller powertrains is about to be launched on the market.
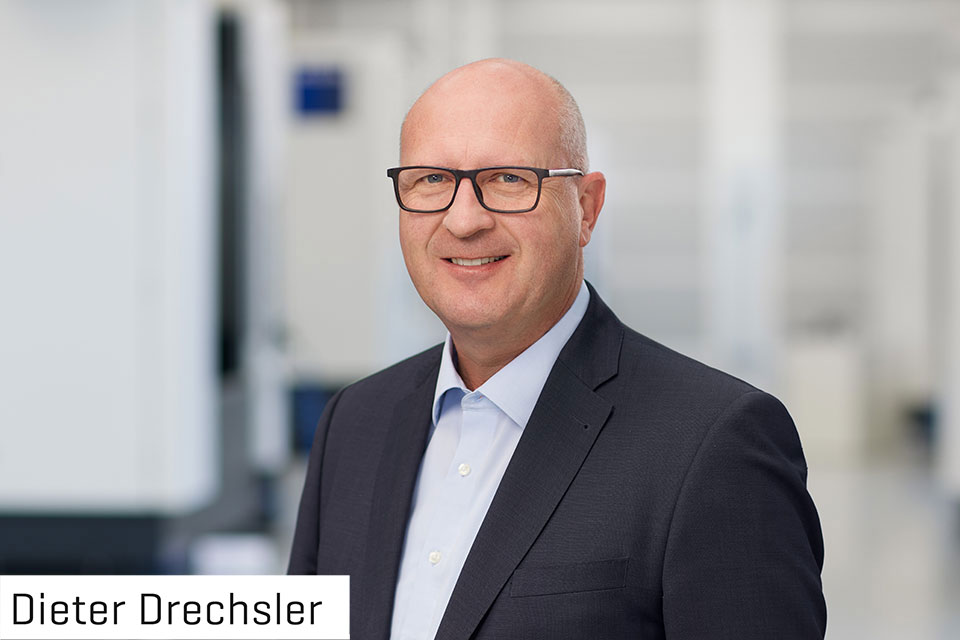
Turning technology: from maximum productivity to full flexibility
For many years, HELLER machining centres have enabled complete machining by milling and turning on a single machine. With the Mill-Turn functionality, the additional turning operation is carried out using a rapidly rotating rotary table. The HELLER out-facing head is an NC drive integrated into the spindle unit for the use of motion tools.
In addition to that, the Nürtingen-based machine tool manufacturer offers another alternative turning option – interpolation turning. What is new about it is the application of a Siemens-developed software feature, for which HELLER provided exclusive support during the development phase.
Although interpolation turning is significantly slower than the methods mentioned previously, it offers a range of advantages: it requires no special hardware, causes only minimal software costs and can be retrofitted at any time in the modern Siemens Sinumerik controls (from software version 4.95). This makes it an interesting alternative for all users who only rarely require a turning function on the machining centre and who in particular value higher flexibility.
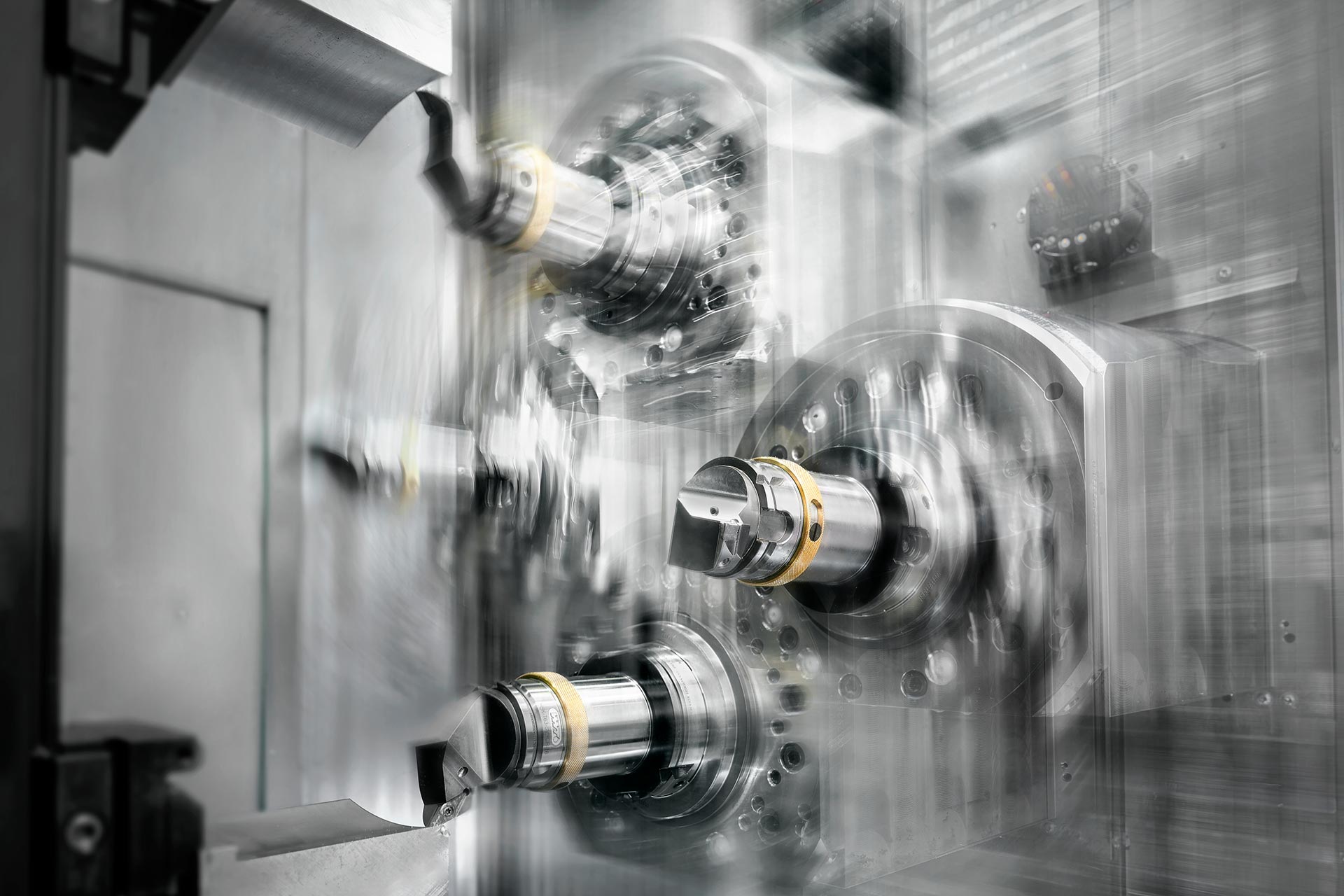
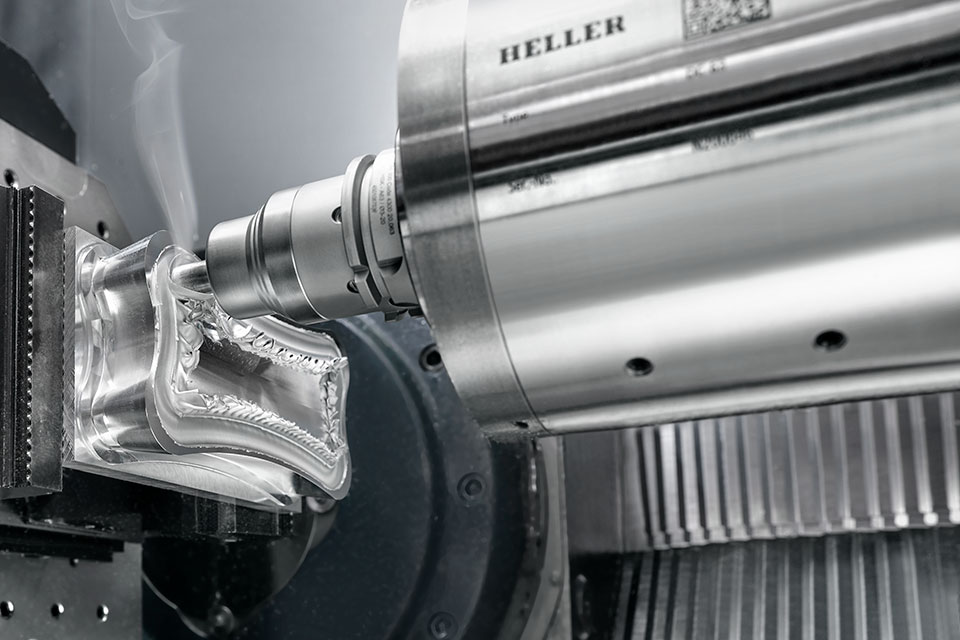
Flexible joining process for machining centres: friction stir welding
An integrated joining technology enables complete machining in a completely different way: at the 2022 in-house exhibition, HELLER presented friction stir welding integrated into four- and five-axis machining centres to the general public for the first time. This was preceded by an extensive test phase with several pilot customers.
Basically, the friction stir welding technology has been around for a very long time. The process-controlled implementation via the Siemens CNC Sinumerik 840D sl control of the HELLER machines is totally new – without using so-called load cells. The retrofittable software feature enables reliable cavity-free welding of aluminium housings, as used, for example, in the food industry. Managing Director Dieter Drechsler sees e-mobility as another target industry: “The welding of battery boxes with lids will be increasingly in demand in the future. We enable complete machining and subsequent welding in one setup. In terms of productivity and precision, this offers clear advantages for the user.”
Gear cutting made easy: gear hobbing and power skiving
In addition, two brand new methods for producing gearings on various HELLER 5-axis machining centres are now available: gear hobbing and power skiving. “Both processes can be retrofitted via software and are particularly suited for the machining of complex products in a single setup such as planetary carriers,” Dieter Drechsler explains. Pure gear production using this method is usually only viable for small to medium series. A major advantage of the process is easy programming via an HMI-supported user interface.
Which of the two methods is best suited depends on the type of gearing, but also on the type of machine used. Power skiving, for example, can be used to produce not only straight and helical external gears but also internal gears of all kinds. Precondition: the machining centres must be equipped with the relevant turning functionality. For gear hobbing this is not necessary. However, this method is only suitable for external gears – whether straight or helical is irrelevant (read more).
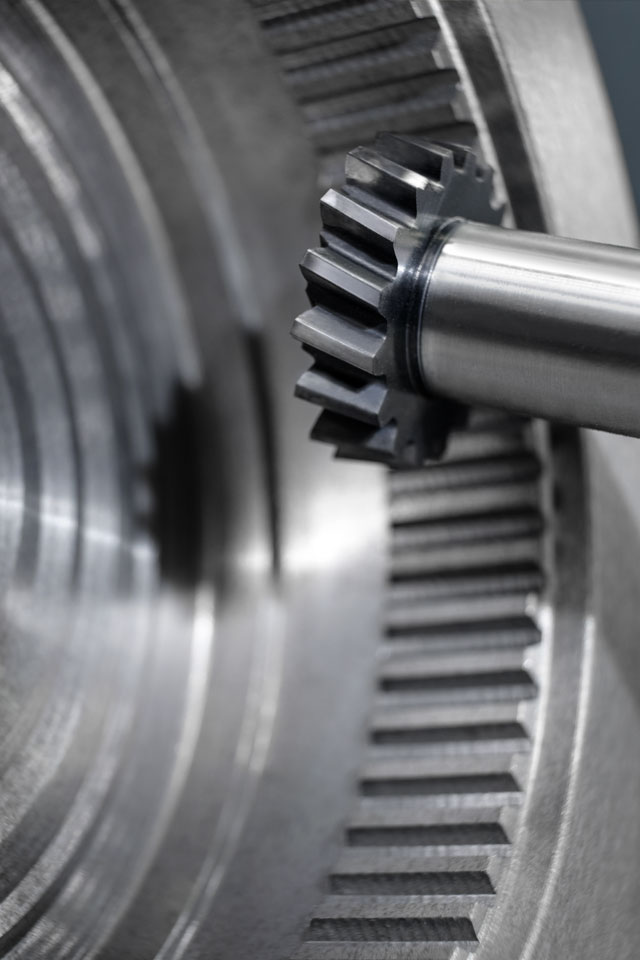
Gear cutting made easy: gear hobbing and power skiving
In addition, two brand new methods for producing gearings on various HELLER 5-axis machining centres are now available: gear hobbing and power skiving. “Both processes can be retrofitted via software and are particularly suited for the machining of complex products in a single setup such as planetary carriers,” Dieter Drechsler explains. Pure gear production using this method is usually only viable for small to medium series. A major advantage of the process is easy programming via an HMI-supported user interface.
Which of the two methods is best suited depends on the type of gearing, but also on the type of machine used. Power skiving, for example, can be used to produce not only straight and helical external gears but also internal gears of all kinds. Precondition: the machining centres must be equipped with the relevant turning functionality. For gear hobbing this is not necessary. However, this method is only suitable for external gears – whether straight or helical is irrelevant (read more).
CBC 10: coating of the inner surfaces of small cylinders
Last but not least, HELLER is launching a new system for the coating of cylinder surfaces using wire arc spraying: CBC 10. It is the smaller sibling to the CBC 200 coating system based on twin-wire technology, which has been established for more than ten years now. This autumn, HELLER will be presenting the CBC 10 equipped with the new single-wire technology. The aim of this development is to make the coating process used for larger engines with an average displacement of two to three litres available for the production of small engines with up to 125cc. Ultimately, engines manufactured with this technology are much more environmentally friendly – thanks to the HELLER technology which reduces friction and wear, and thus fuel consumption and emissions.