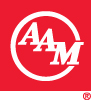
As a leading global tier 1 automotive supplier, American Axle & Manufacturing, Inc. (AAM) designs, engineers and manufactures systems and technologies making the next generation of vehicles smarter, lighter, safer and more efficient.
Headquartered in Detroit, AAM has over 21,000 associates operating at nearly 80 facilities in 17 countries to support their customers on global and regional platforms with a focus on quality, operational excellence and technology leadership.
Collaboration with HELLER
Over 20 years ago, HELLER reached out to the AAM CEO at the time and started the relationship which really took off when AAM opened their Mexico office: HELLER was the exclusive choice for all prismatic cast iron machining that AAM was launching to the major OEM auto manufacturer GM. The “add-on” was when AAM won the FCA business for their heavy duty trucks.
According to Tom Szymanski, Vice President of Global Manufacturing Services, American Axle & Manufacturing, Inc. has the full gamut of HELLER equipment, H 4000s, H 4500s, H 5000s, and is still running some 20-year-old MCP’s “that are still running really well and making good parts”.
“We have always had good service support from HELLER, anywhere on the globe.”
“When we upgraded to the HELLER equipment and technology, we saw a dramatic improvement in the quality of our carriers for front and rear axles which was our bread and butter business at that time, and along with this improvement came a big improvement on Ring and pinion replacement warranty for the OEMs.”
“When you are hogging off and cutting big cast iron carriers day in and day out, 24 hours a day for 6+ days a week and the machines hold up for 15 plus years, I think that speaks for itself.”
“The other machines’ controls became obsolete in terms of electronics and capabilities as new technologies were deployed. So, the reliability of the HELLER equipment was a definite strength over other suppliers.”
“HELLER has always built high-quality machines and mechanically the HELLER machines from our experience have outperformed the rest of the (other branded) machines.”
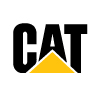
Since 1925, Caterpillar Inc. has been helping their customers build a better world – making sustainable progress possible and driving positive change on every continent.
With 2019 sales and revenues of $53.8 billion, Caterpillar is the world’s leading manufacturer of construction and mining equipment, diesel and natural gas engines, industrial gas turbines and diesel-electric locomotives. Services offered throughout the product life cycle, cutting-edge technology and decades of product expertise set Caterpillar apart, providing exceptional value to help their customers succeed. The company principally operates through three primary segments – Construction Industries, Resource Industries and Energy & Transportation – and provides financing and related services through its Financial Products segment.
Collaboration with HELLER
Caterpillar’s sister machining facility in San Antonio, Texas that also machines heads and blocks has been utilizing HELLER machines since they opened in 2003. The team located in Schertz, Texas has also been producing parts on HELLER machines since they opened the facility in 2011.
“HELLER has always been very flexible when working with CAT. HELLER takes the time to develop the processes with our engineering teams to make sure the processes are seamless. This is unlike the other machine tool OEMs that have told CAT, ‘this is the process you are going to use’, which has not worked out in the past.”
“HELLER knows the diesel industry very well which allows HELLER to bring processing strength to the table. The trust in expertise is a big factor in the partnership.”
“HELLER machines are more heavy duty than competitors’ machines. The flexibility of being able to use the machines as stand-alone, gantry loaded, robot loaded etc. is a good advantage.”
“The partnership with the process design is a big advantage – this is a lot better than when the machine builder just hands you a machine and says, ‘have at it’.”
“Before introducing HELLER, the machines were manually loaded commodity machines and specially designed transfer lines. The key benefit of the HELLERs was still the gantry loaded automated processes, but with the flexibility of having machining centers mixed with specialized machines to keep throughput high and have the ability to adapt the equipment to new or different processes. There was not the flexibility we have now since bringing HELLER machine solutions into the plants.”