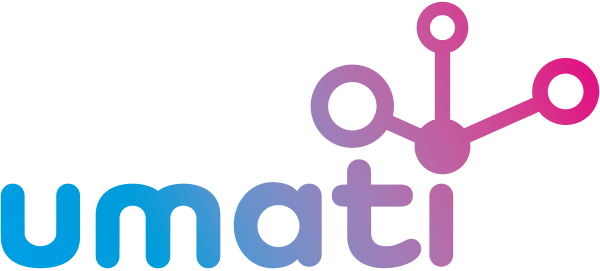
Digitisation of production is more and more becoming a reality. To date, proprietary systems complicate linkage to subordinate and superordinate control levels. An initiative started by the German Machine Tool Builders Association VDW has succeeded in developing an internationally accepted standard for a data exchange interface called umati.
TEXT Martin Ricchiuti IMAGES VDW, Ansgar Pudenz
Anyone engaged in the linkage of industrial systems – be it vertical integration with superordinate systems or horizontal integration of equivalent units – has to consider the compatibility of the various controls and interfaces. Over decades, various manufacturers and providers have pursued their own proprietary approaches which they deemed appropriate for the application at hand. This resulted in heterogeneously controlled and linked machinery, performing as intended following installation, but requiring a substantial integration effort with every modification made to the original configuration.
Many entrepreneurs are feeling the enormous impact of this almost Babylonian confusion, particularly regarding the numerous ongoing digitisation initiatives. To extract data from your systems, you first have to merge and standardise data. Otherwise it will not be possible to perform any analyses beyond the systems’ boundaries. According to Bernd Zapf, Head of Development New Business & Technology at Gebr. Heller Maschinenfabrik GmbH (image p. 51), these kinds of problems already emerge when linking a machine to MES software: “What we have is a standardised and extensively documented interface. In practice, we then have to see whether we have to adapt our interface to the conditions at customer site or vice versa. The first scenario always incurs additional costs, ties up capacities and complicates a seamless integration. This is something we are faced with almost every time we sell a machine. In the second scenario, the automation or software partner is required to make the adaptation.” This example gives us an idea of the kind of complexity the machine tool manufacturer is confronted with during the integration and what kind of know-how he has acquired over the past years.
Uniform machine interface paves the way for data exchange
Zapf expressly welcomes the VDW’s initiative to develop a uniform machine interface in close cooperation with machine tool manufacturers: “We prefer to adopt an active role in the design to promote our idea of universal compatibility of different machines, units and software. As a so-called ‘core partner’, HELLER became involved at an early stage, playing a key role in the engineering of the umati interface.
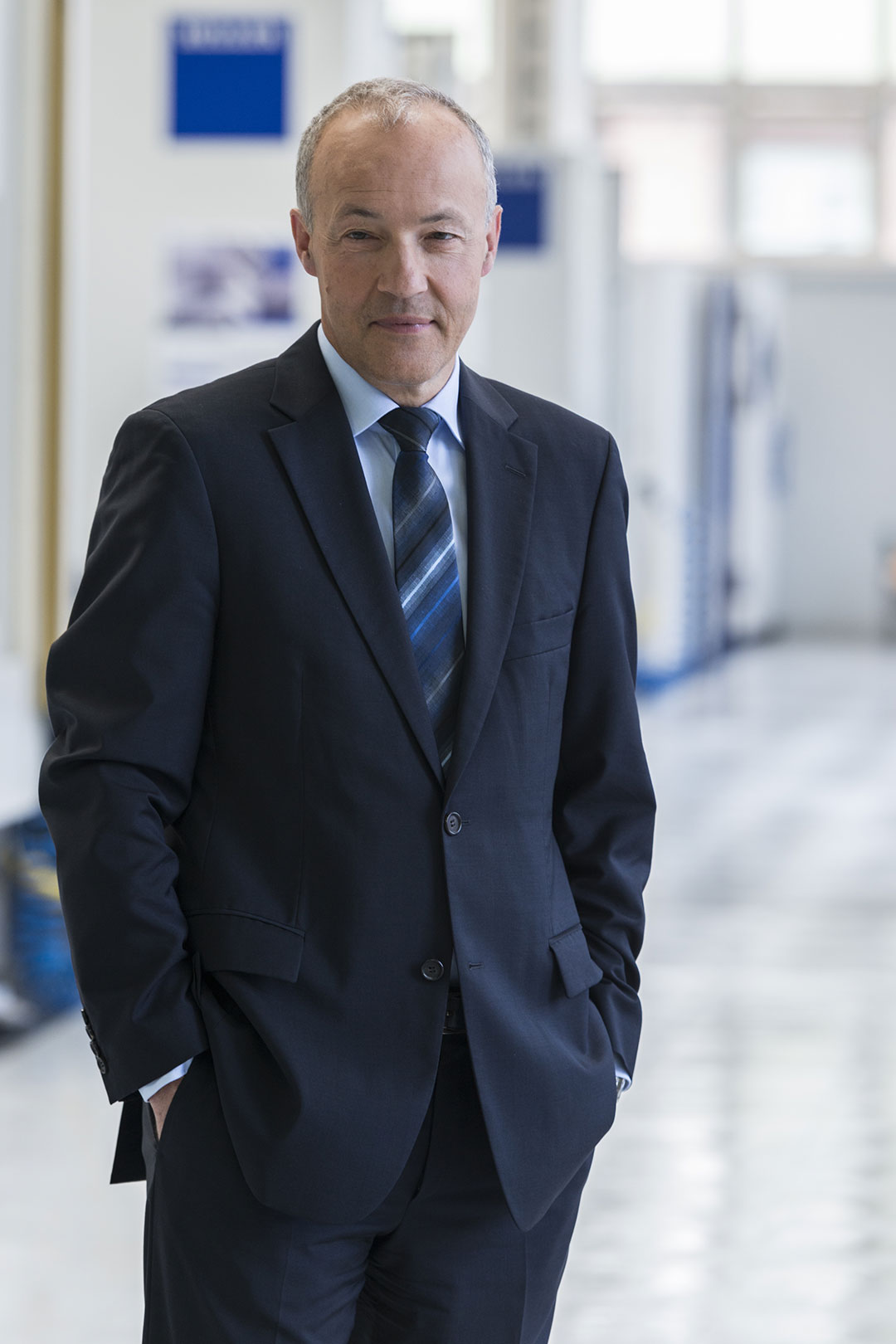
The OPC-UA server developed by VDW in 2006 provides the foundation for the umati standard. The OPC-UA server acts as a ‘translator’, transforming the various data formats provided by the CNC control, the HMI or other data sources into clear-text encoded signals. It significantly facilitates communication on a purely formal level.” Zapf gives an example to illustrate this: “To perform a machine status enquiry, all you have to do is ask the question: what is the machine status? Since the answer to this question is provided in clear text, it is just as easy to understand. Before we had umati, the question would be just as cryptic as the response. This does not only increase ease of operation, but also provides higher user acceptance.”
“Another crucial advantage of the umati project is its transparency,” Zapf explains. “Unlike previous standardisation efforts, all parties involved in the joint working group pull together. However, this requires a certain willingness to compromise to ensure a viable consensus is reached and the project is making progress. The involvement of control manufacturers from Japan and the North American MQTT initiative underscores the outreach and significance of the umati standardisation efforts.”
In a way, umati can be compared to road traffic regulations – provided all parties involved observe the rules, smooth and secure data exchange is guaranteed. At the same time, the VDW-managed project is open to many different machine manufacturers. It includes companies from different industries whose requirements in terms of data signals are uncommon in metal-cutting machining, for example. As a result, the exchange with these industries brings fresh impetus to machine tool manufacturing. In the future, umati will cover these various data requirements. The advantage for HELLER is that for data provision, the OPC-UA server only has to be configured for umati communication. No programming is needed. Zapf stresses: “We as Heller have decided to realise the entire transformation outside of the control in order to leave the machine control untouched. For this we use edge computing in the form of Sinumerik-Edge: the OPC-UA server is installed in the small grey box. If this is already sufficient for the signal scope at hand, no further installation is needed. If the required signal scope goes beyond that provided by the control, we additionally install the transformation engine to comply with the umati standard.”
This configuration can easily be retrofitted to existing HELLER machines using the edge computer. In the future, customers operating older machine models will be able to upgrade their machines with the additional edge computer to be on the safe side.
Standardisation where necessary, flexibility where possible
Bernd Zapf is convinced that the wide acceptance of standardisation based on umati is due to the approach utilising functions known from social communities: “The more companies participate, the broader the acceptance. Genuine willingness to compromise ensures the agreement of all. By now, China, Japan and the US have expressed their interest in this standard – a dream that seemed inconceivable only a short while ago.”
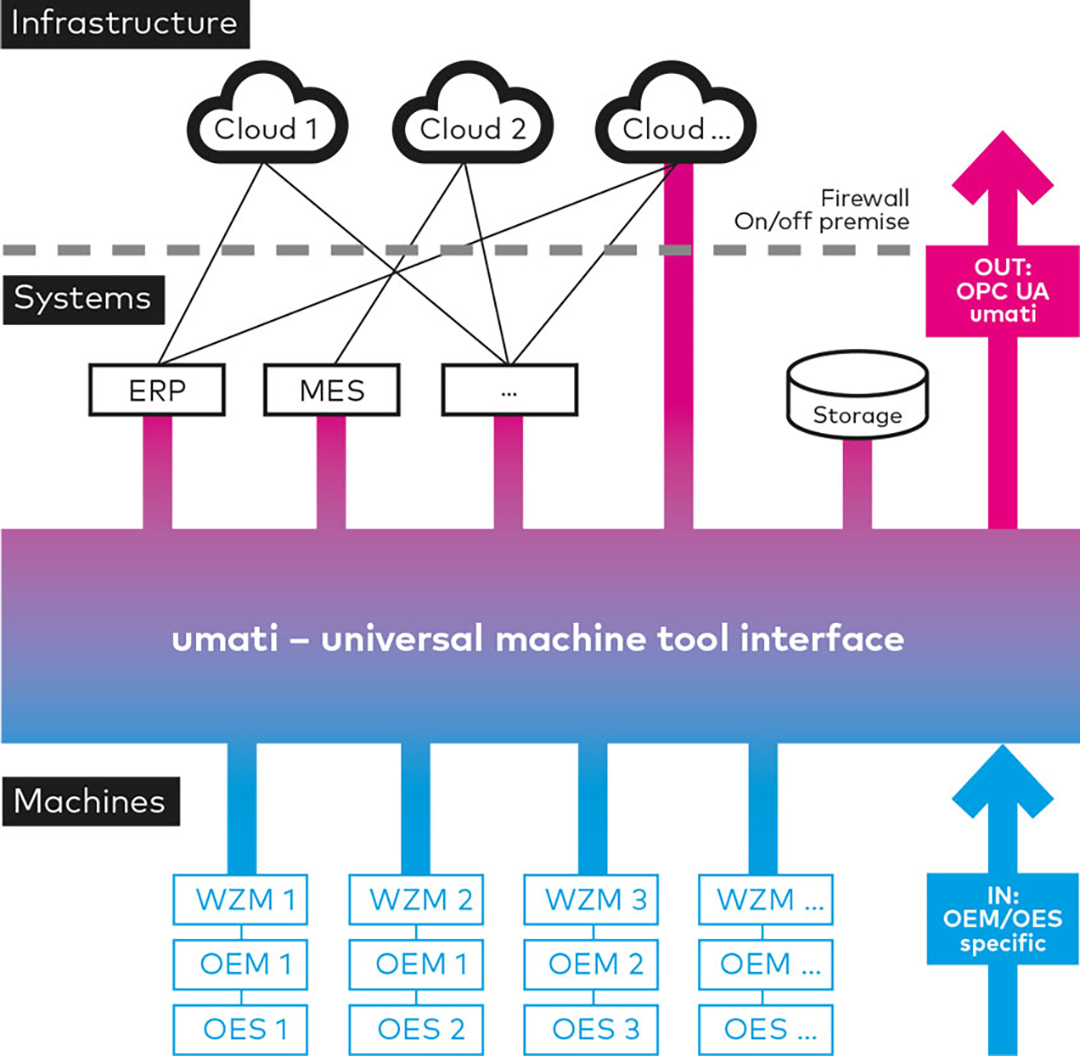
What are the benefits to the user?
The user has the advantage that he can link different systems with minimal effort. This applies to various machine types, from tool presetters or measuring machines, deburring cells and part cleaning through to machine tools and peripheral equipment.
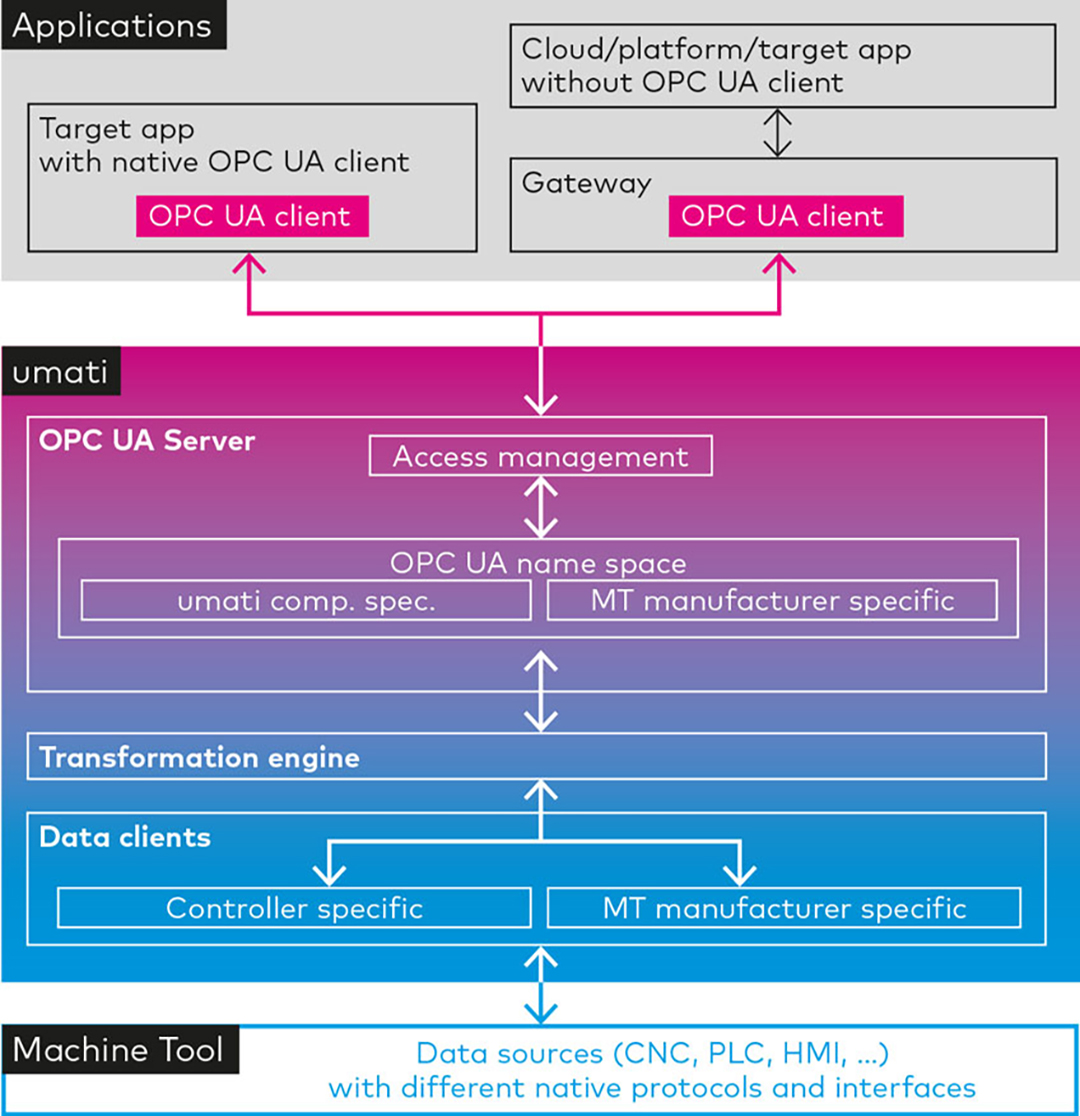
To illustrate the functional principle of umati, HELLER will present various use cases at EMO: at the trade show, the Nürtingen-based machine tool manufacturer will showcase a total of four data suppliers with the EMO-umati data model: a 5-axis machine at the HELLER stand, two training machines, one of them at the VDW stand, and another 5-axis machine located at the production workshop in Nürtingen from where it sends data.
Another example from tool management illustrates the compatibility of the umati interface: when requesting data about all the tools required for a machining operation using umati, the ‘replies’ from various types of machines or machines from different manufacturers can be transmitted to the superordinate control system. Since only a part of the requirements regarding the new interface have been implemented so far, the current focus is on application examples from machine data acquisition. For this purpose, HELLER will integrate its previous MDA/PDA interface into the umati data model, making it possible to link the previous interface to MES systems without any problem using umati.
With umati and its wide market acceptance based on the involvement of many different stakeholders such as control manufacturers, machine builders and software suppliers, the goal of plug-and-produce solutions has come within reach. In terms of Industry 4.0 and digitisation of production, this means an enormous step forward has been taken.