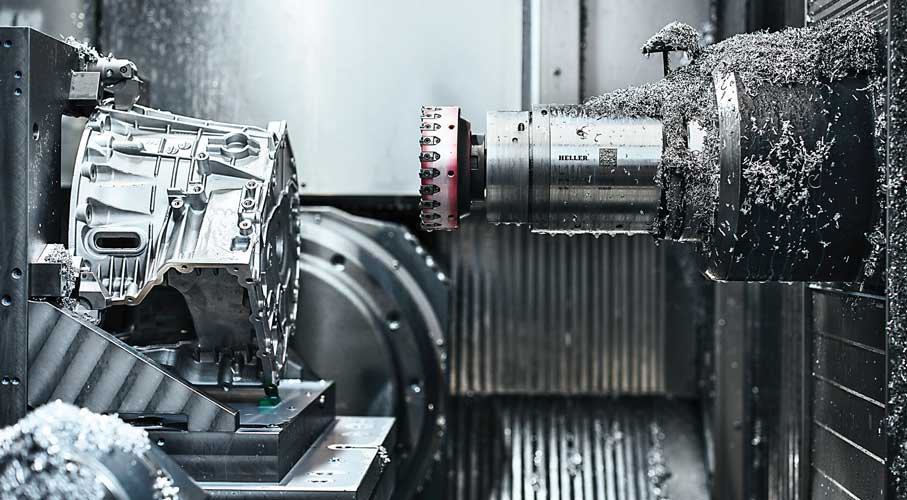
TEXT Manfred Lerch PHOTOS Sebastian Grenzing
HELLER envisioned the application of the first 5-axis machining centres from the HF series, with the 5th axis provided by the workpiece, mainly for medium-sized batches in series production. With the development of the second generation, the range of application has now expanded significantly. The company Stöferle manufactures up to 350,000 components per year on two HF 5500 machines integrated into a production line. In three shifts, the automotive supplier is constantly pushing the limits of the machining centres and convinced that they were an investment in the future. In addition, Stöferle has meanwhile invested in what is now the fourth generation of the 4-axis machining centres from the H series.
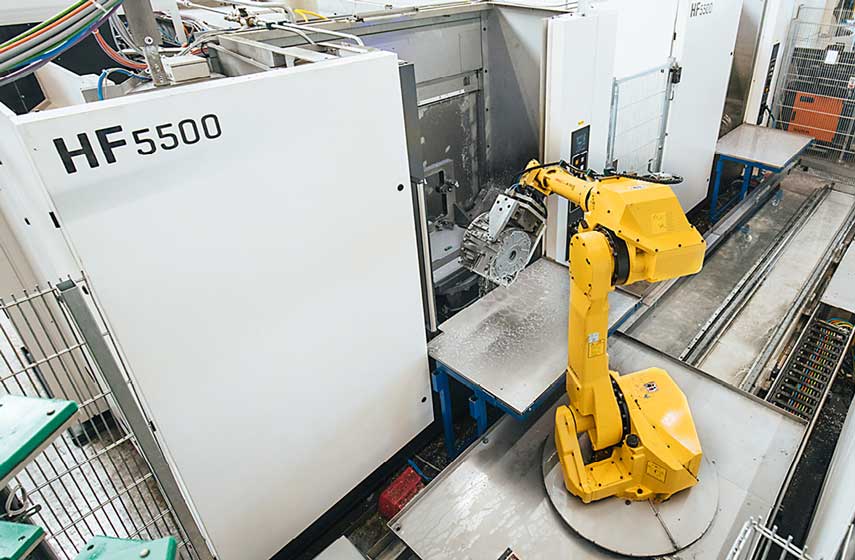
The company Stöferle based in Laupheim has been confronted with the development of alternative, CO2-free drive systems in the automotive industry for years. With the introduction of electromobility and hybrid technology, components are becoming more and more complex. Moreover, the requirements in terms of precise and increasingly inclined surfaces as well as high-quality surfaces are increasing. In 2019, the company therefore started looking for suitable machining centres for the machining of large components for use in mild hybrid car models with fits between H6 and H7 and diameters ranging from 240 to 320 mm. It invested in two HELLER 5-axis machining centres model HF 5500 of the second generation.
Now, however, Stöferle is in a special situation. On the one hand, the company develops special-purpose machines itself. On the other hand, as a partner of HELLER, they are testing machining centres in medium and large volume production, running three shifts, seven days a week. For Managing Director Erich Stöferle, these are real endurance tests: “We are always operating the machines at the maximum limits, including the HF series, going up to ten percent below the performance limits specified by HELLER. If the maximum weight of a milling cutter is specified as 16 kg, we go up to 15.5 kg. We have been doing this for years. For example, we are operating a Ø 160 mm cutter at 15,000 rpm. That may not be a problem in single-part manufacturing, but we produce in three shifts. Another aspect is that the two HF 5500 are part of a manufacturing line comprising five to six machines and that batch sizes have initially been set at 350,000 pieces/year. Therefore, highest levels of reliability and availability are a basic requirement for us.” This shows that the HELLER DNA of productivity, precision and reliability has been implemented in a practice-oriented manner in the new generation.
The people in Laupheim believe that the new HSU inline spindles, which are absolutely made by HELLER, provide clear advantages over the first generation. In terms of vibration behaviour, these spindles are much more rigid, allowing a quick and cost-effective replacement for service purposes. Regarding spindle units, Stöferle opted for Speed Cutting (SC) spindles with speeds of 18,000 rpm and 103 Nm of torque. Moreover, the machining centres also provide impressive precision. In terms of parallelism, the large components are within 2/100 mm and regarding surface finish and flatness the valley depth lies at 6. Accordingly, these tolerances can be achieved. What is more, in contrast to the first generation, the new spindles allow to achieve significantly higher quality surfaces. Another and very important change for Erich Stöferle was the shortening of the distance from the spindle front edge to the rotary centre of the B-axis, because until now the people in Laupheim often required an extension for the tools.
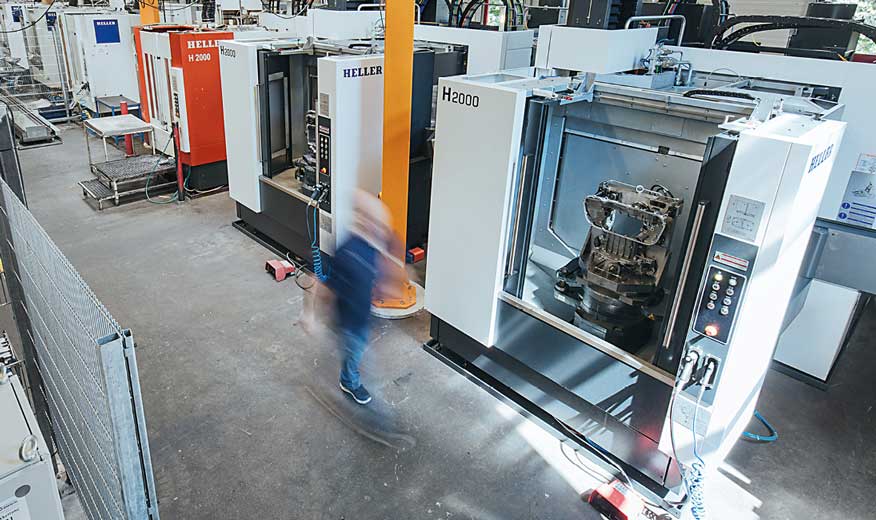
With the fourth generation of the H series, HELLER has significantly increased the dynamics. Chip-to-chip times have been measurably reduced on specific components. That is why the company invested in two H 2000 machines of the new generation.
4th generation provides significantly reduced chip-to-chip times
Stöferle is also carrying out field tests on what is now the fourth generation of the 4-axis machining centres from the H series. Since February 2020, these machines have been used to the maximum in large-volume production. For Managing Director Katja Stöferle, this is a logical consequence of the experience gained so far: “We have more than 20 machines from this series and have reliably manufactured over a million components on quite a few of them without major repairs. For example, we had an H 2000 that ran for 15 years with the same ball screw drive. For transmission components with batch sizes of 250,000 pieces/year, the stability, the drives and the chip disposal simply have to be right. To put it briefly, these are our best machines. Regardless of this, electromobility not only increases the requirements in terms of the components, but also the batch sizes. That is why we are continuously looking for ways to reduce cycle times. Not much can be said about the reliability of the new generation of the H series, but HELLER has significantly increased the dynamics of this generation, allowing us to measurably reduce the chip-to-chip times for specific components. This is one of the reasons why we have invested in another three H 2000 models.” According to René Greising of the regional representative Hans P. Greising GmbH, it is the heart of the machine, i.e., the spindle, which is primarily responsible for this reduction in machining times. “For this generation, HELLER offers three variants: Power Cutting (PC), Speed Cutting (SC) and now Dynamic Cutting (DC). The DC units in particular perfectly combine high torques with high speeds.”
Overall, both new generations from HELLER have already been put through their paces in practice and have been available in the market as well-engineered machines since the beginning of 2021.
The H 2000 is and has always been an excellent machine.
The proportions are just right. It is low, has little movement in the bed, wide guideways, a good spindle and runs absolutely reliably for years in three-shift operation.
Erich Stöferle
“
The two machining centres were purchased for the machining of large components for use in mild hybrid car models with fits between H6 and H7 and diameters ranging from 240 to 320 mm.
“With batch sizes between 200,000 and 300,000 parts, we have to be highly productive and flexible. The components are constantly changing, requiring inclined bores, new angles to be approached, etc. Of course we have to be able to respond quickly to these requirements.”
Erich und Katja Stöferle
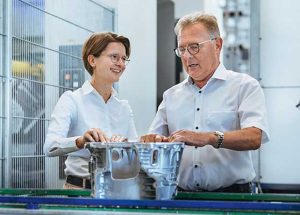
Stöferle GmbH founded in 1992 employs 200 people and focuses on tailor-made, individual solutions for the economic and quick production of medium and large volumes in light-metal processing. This also includes the development of special-purpose machines. Stöferle is a partner and supplier to the automotive industry. In order to make better use of technology transfer and synergies, the company was expanded by Stöferle Automotive GmbH. In this area, Stöferle acts as a system supplier. In addition, Stöferle manufactures parts washing systems, systems for leak testing and assembly as well as additional components such as clamping fixtures, handling systems and production-related measuring and testing equipment. www.stoeferle-gmbh.com
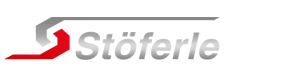