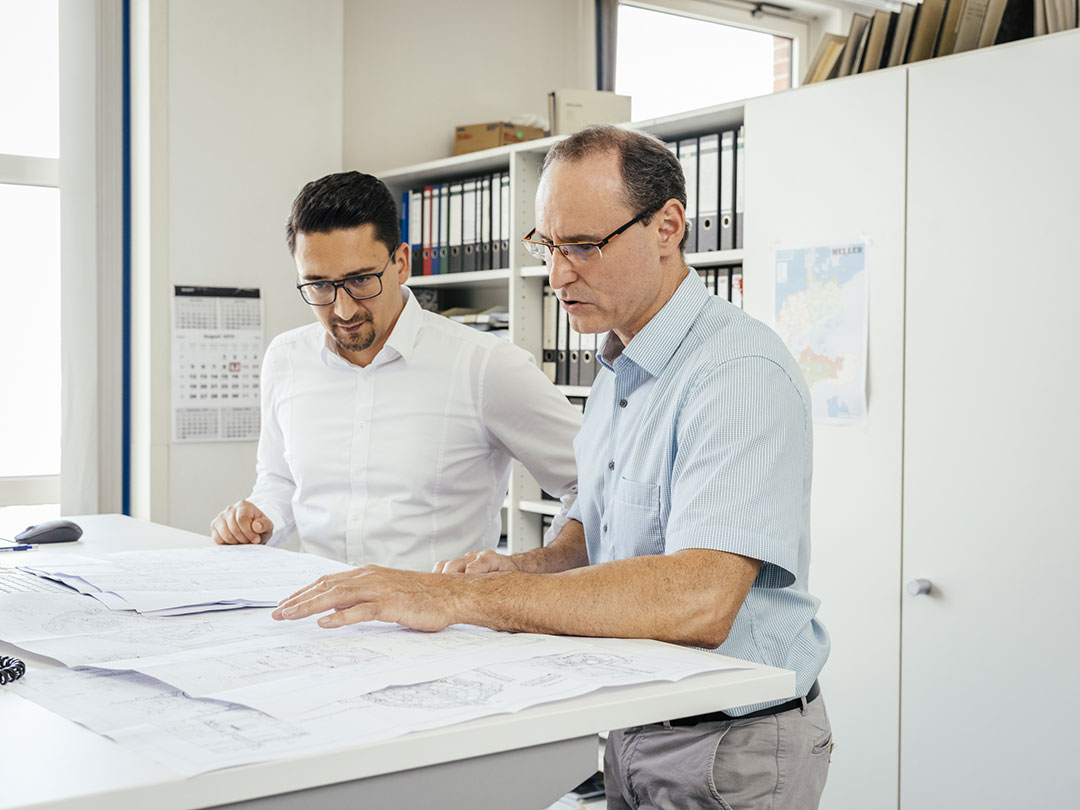
At the end of 2018, HELLER established the SNSE department as a support and engineering team. The new team’s goal is to minimise the response times from the first enquiry to the elaboration of a specific quotation, especially for enquiries received from the European market. The department’s responsibilities cover three subject areas: determination of the machine type and definition of the required machine options, elaboration of the machining processes and the appropriate machining strategy and visualization, and, as a third step, the preparation of cycle time calculations.
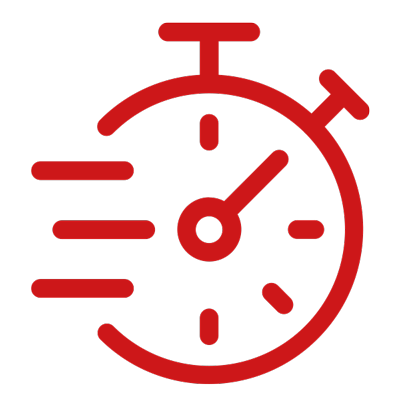
TEXT Manfred Lerch IMAGES Tina Trumpp
Ninety percent of the components machined by the customer are made of aluminium. Therefore, he intended to invest in a machine equipped with an SC63 spindle unit with 16,000 rpm. However, in addition to the aluminium components, he also machines steel components. The result of the spindle power investigation performed by SNSE based on tooling and cutting data provided by the customer from their current manufacturing process showed that the planned machining operation would go to the limits of spindle performance. Therefore, the team recommended a different machining strategy for the steel components. This meant that the tool number had to be increased from three to four, but resulted in significant time savings and a reduced spindle load.
The SNSE department often faces a situation where a customer wants a specific machine model. The example in which the customer initially considered a 5-axis mill/turning centre illustrates the benefits and economic advantages of the analyses and assessments made by the department. In this specific case, the investigation showed that the use of the HELLER out-facing head solution on a 4-axis machining centre was the more cost-effective solution for the machining of the workpieces in question.
At HELLER, engineering starts with the quotation phase. After all, the design of the machining processes, clamping fixtures and tooling, and the determination of machine models and cycle time calculation often provide the basis for a ready-to-order quotation. So far, HELLER provides four teams for these tasks, working on projects from all over the world and specialising in crankshafts, prismatic engine components, transmission and axle components and components from hydraulics, mechanical engineering, agriculture and construction machinery, etc. In mid-2018, HELLER came up with the idea to install an application department for the European market under the direction of the Sales and Services Europe business unit. Today, the department established at the end of 2018 comprises four staff, partly contributing more than 25 years of experience at HELLER. The department’s main goal is to reduce response times by providing preliminary studies. Determining the appropriate machine types is the initial goal when receiving an enquiry. This means that the customer provides SNSE with information and data about the workpiece to be machined and a request for an appropriate machine. Head of SNSE Atilla Yurtseven and his team investigate the swing diameters and, depending on the workpiece dimensions and machining requirements, recommend a suitable machine for 4-axis or 5-axis machining. The result and the evaluation are forwarded to Sales including recommended options, e.g. the appropriate spindle type or software options.
Analyses and recommendations regarding machining strategies
In the second stage of the process, the results are visualised. This includes a 3D analysis of the work area with consideration of the workpiece, the complete clamping fixtures and, if requested, first machining strategies. Recently, the demand for these has increased, as customers often have not yet machined the components and therefore ask for suggestions regarding the number of setups or possible sequential processes. The workpiece dimensions and the predefined tolerances provide the basis for these investigations in order to visualise a reasonable and efficient process. One customer, for example, wanted to use several redundant machining centres for complete machining in a single setup in order to reduce setup times and to achieve shorter cycle times. SNSE’s analysis and calculation showed that the machining of the workpiece would require approx. 50 tools. However, further investigations also showed that machining of the high numbers required using a single setup was not feasible without compromises due to possible collision paths of the fixtures and the resulting use of relatively long tools. Therefore, the SNSE team recommended a sequential process to optimise accessibility on the workpiece (tool lengths), the machining process and, as a result, machining time.
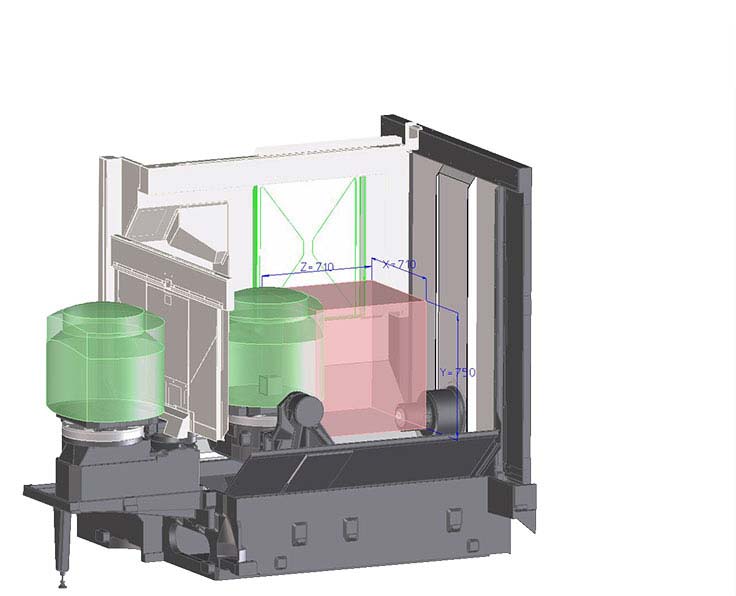
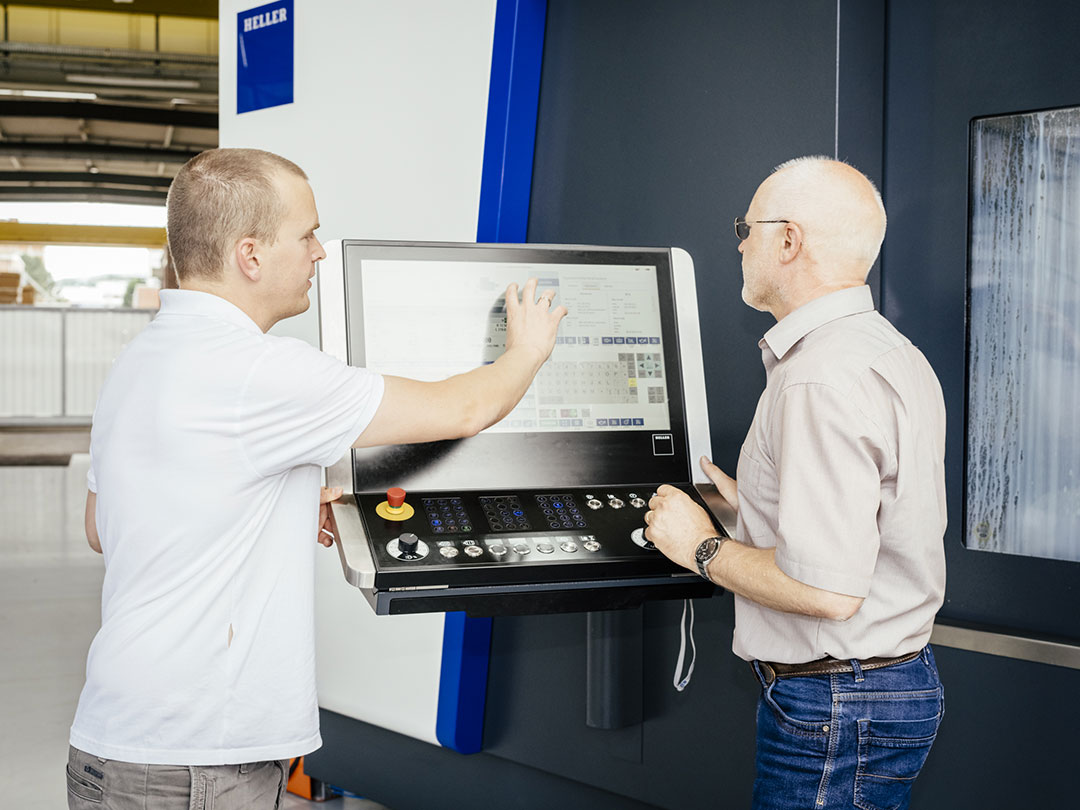
This approach also allowed to achieve a significant reduction in the overall investment costs for tooling as the required tools do not have to be provided in all machining centres.
In the third stage, SNSE prepares the cycle time calculation. For this purpose, the department can simulate the machining process in the CAD/CAM system, even for complex components from mold and die manufacturing or aerospace. In this specific case, the workpiece was a complex die plate machined from solid material. For this process, the tool technology and the cutting data as well as the programming strategy played a major role. The component was simulated in the CAD/CAM system. To verify the process data, trial machining was performed in cooperation with tooling partners at HELLER’s own TechnologyCenter.
Product and process knowledge for optimal process design
The department handles a wide range of different tasks. Depending on customer requirements, the projects range from ‘naked’ machines through to complete turnkey solutions for which, depending on complexity, the team receive support from the central application department. A different approach is also required when the customer intends to machine new components. In this case, the SNSE department also gets involved at an early stage. In many other cases, customers ask for a neutral assessment of an existing machining process. With the customer contributing his experience, the SNSE team starts from scratch. The goal is to identify the best possible synthesis at the end. In most cases, these constellations lead to very positive results. Whilst the customer contributes his experience with the workpiece, the SNSE team provides the current process know-how.
In summary, the SNSE department is a support and engineering team verifying the proposal made by Sales regarding which machine fits which workpiece or customer by investigating the feasibility and economic efficiency. Additionally, the team develops machining strategies and clamping concepts and performs tolerance analyses and cycle time calculations. For these use cases, HELLER customers expect high-quality metal-cutting machines and efficient production processes. And they expect product and process knowledge to be provided and incorporated during the preparation of the quotation, enabling them to manufacture the required output in the required quality.