The main purpose of automated manufacturing and production centres is to achieve a reduction in idle times, thus optimising system availability. However, the requirements of the individual industries vary greatly, resulting in a wide range of different solutions available in the market. HELLER is completely open as far as the three main groups of automation solutions are concerned when it comes to enhancing productivity, availability and economic efficiency.
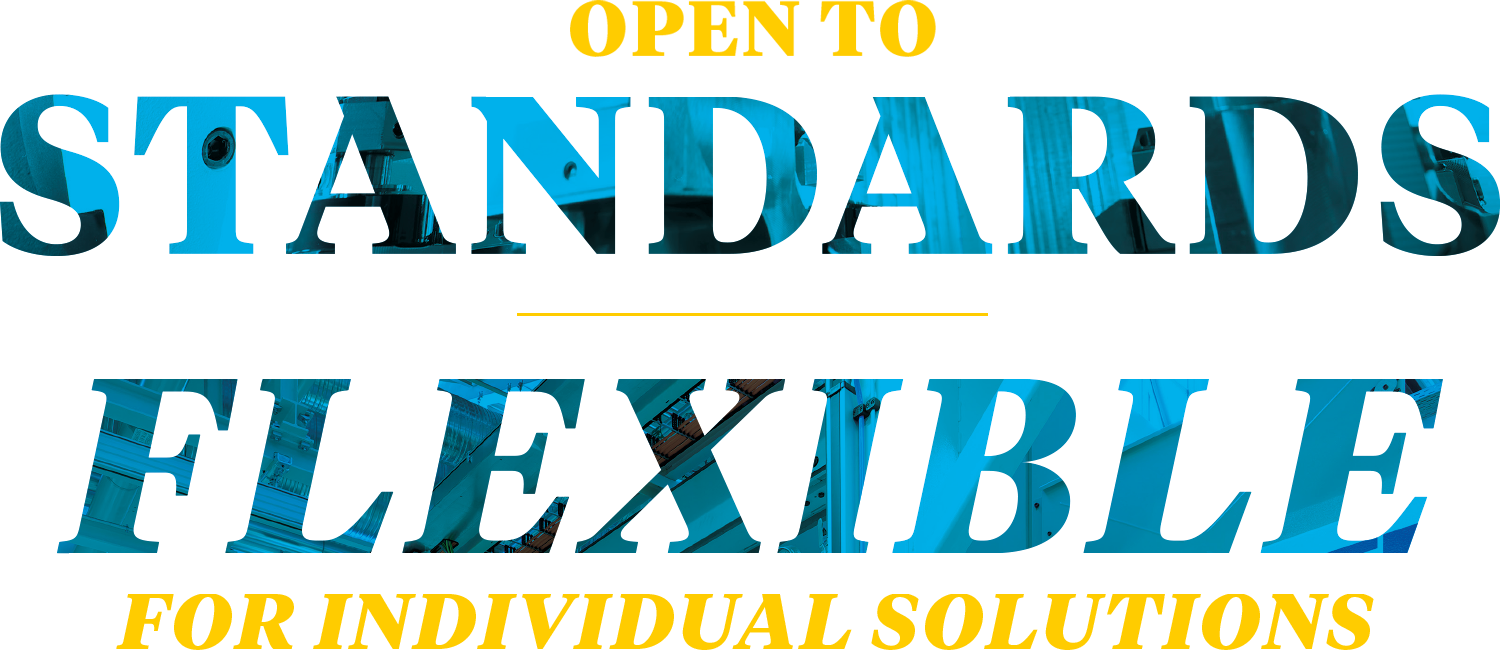
TEXT Manfred Lerch
IMAGES Jens Gelowicz, Manfred Lerch
The introduction of automation is always accompanied by organisational realignment, irrespective whether customers opt for overhead loading of the machining centre, pallet automation or flexible robot cells. The most frequently asked questions before investing in an automation solution therefore mostly concern the various possibilities this type of system offers, how large it has to be in order to be adequately dimensioned for the production in question or whether the targeted cycle times are feasible in order to achieve the desired reduction in per-piece costs.
At Daimler AG, the goal was to achieve a significant reduction in unproductive idle times through maximum productivity. The focus was on agile processes, allowing to respond flexibly to changing customer requirements. The project concerned the manufacturing of crankcases for combustion engines with different workpiece variants to be produced on a flexible, agile manufacturing line. The existing modules comprised up to eight HELLER machining centres loaded via a single gantry loader. The new project was realised using four direct-loading machines per gantry. The goal of these redundant systems is to be able to continue production at a reduced output volume in case one of the gantry loaders is out of operation. Additionally, HELLER positioned an adapter changer in front of each machine, enabling decoupling of the automation and the machining centre
Stationary, mobile or collaborative robot solutions
A totally different automated manufacturing solution was implemented at Samson AG (2) to automate bulk material and to manufacture different part families. The company based in Frankfurt opted for a HELLER 4-axis machining centre model H 2000 with a robot cell. The H 2000 was a standard machining centre, but the challenge involved was the clamping of the component for two operations and the interface to the robot. HELLER took on overall responsibility, and six months later, series production with the system was started.
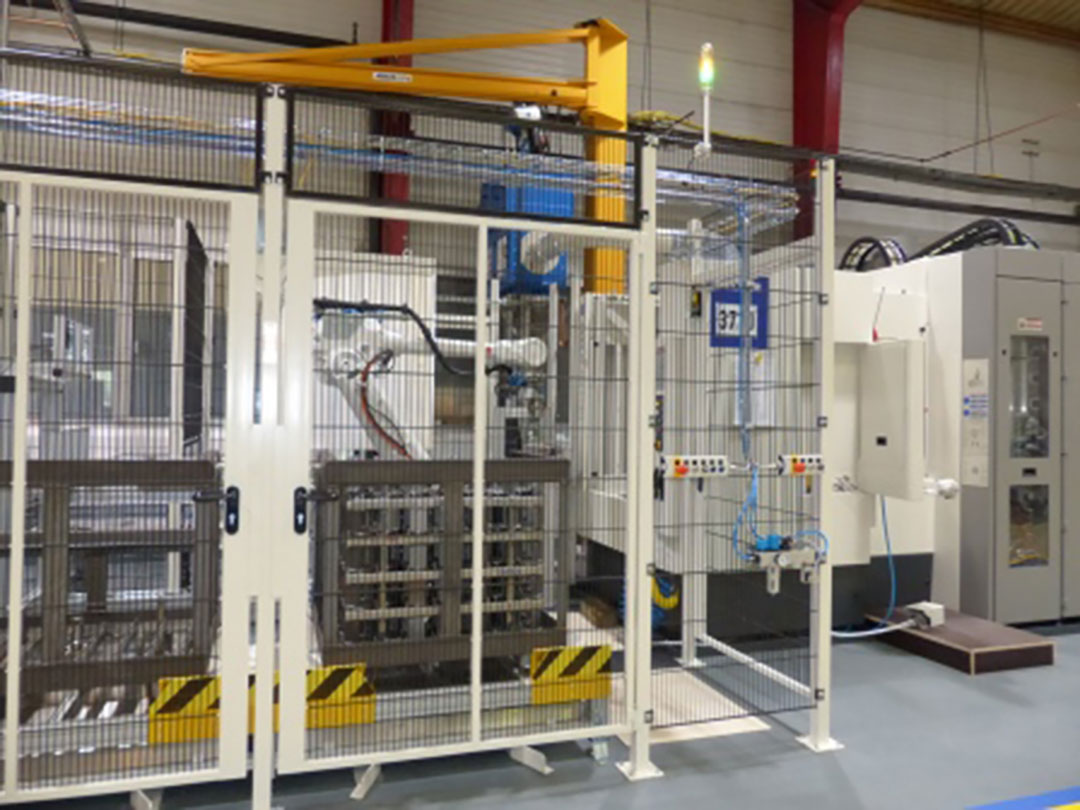
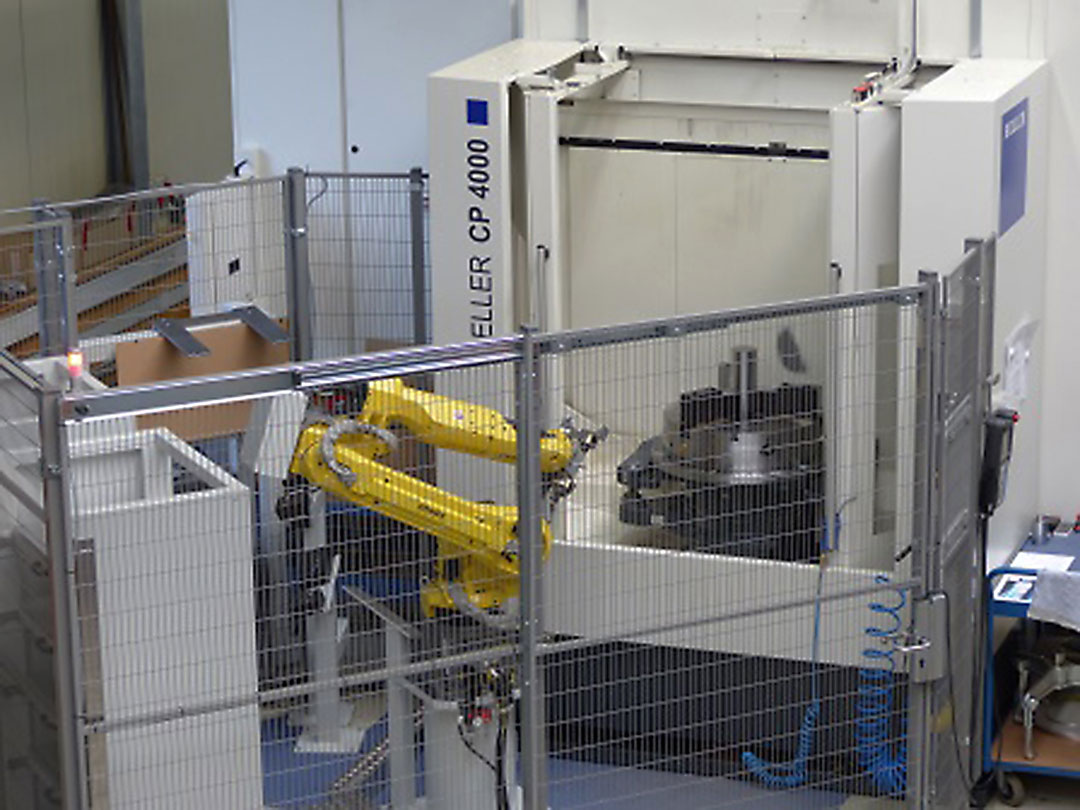
In contrast to this, the company Konstandin (3) based in Carlsbad was aware that it would not have sufficient large turning components to achieve full utilisation of the new 5-axis mill/turning centre model CP 4000 with pallet changer. Therefore, the people in charge opted for a robot automation. The automation itself was a retrofit solution with HELLER being responsible for its connection. The new level of flexibility has not only been achieved through the use of automation, but also due to the productive mill/turning centre model CP 4000. Meanwhile, this investment has resulted in massive time savings and additional capacities.
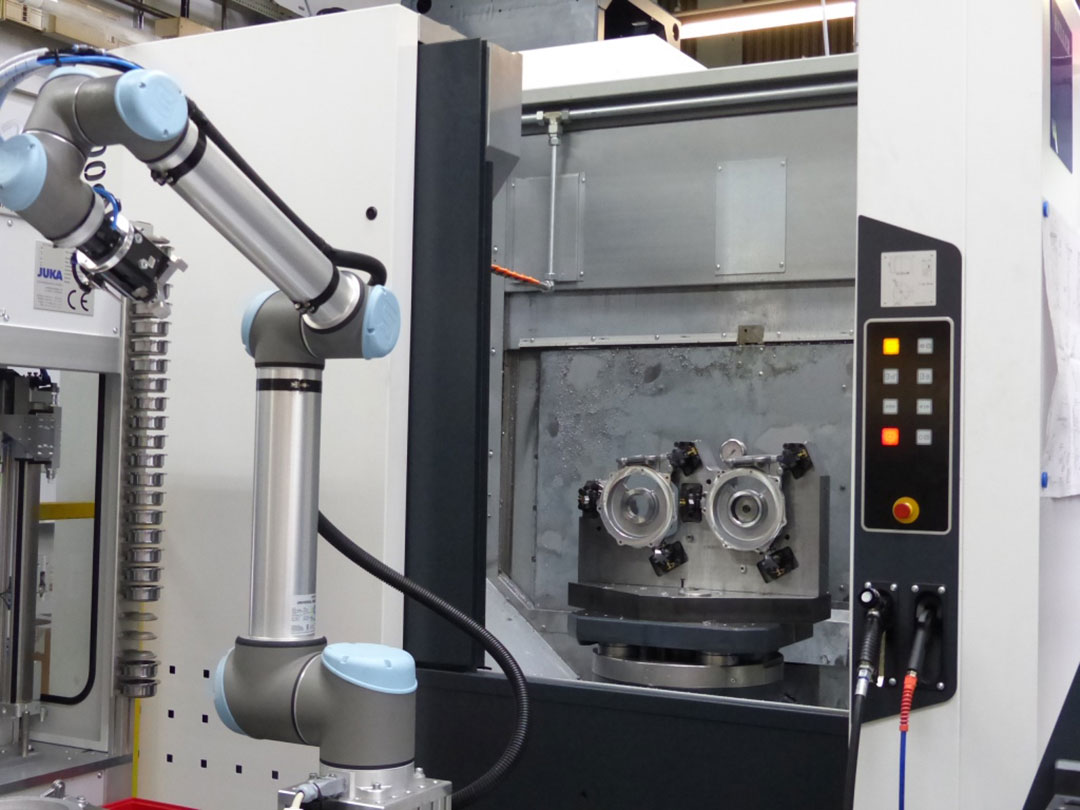
At ZSO Zerspanungs- und Systemtechnik (4) in Oberstaufen, it was also a robot solution that made the difference. The goal was to create a fully automated cell for a major project that was still in the acquisition phase. The workpieces to be machined were cast aluminium components for a major automotive supplier to be produced in an annual volume of several tens of thousands of parts. To achieve this, the manufacturing solution comprises a fully automated cell with a 5-axis machining centre model HF 3500 and a collaborative robot. The workpiece is manufactured in two setups using 5-axis machining. Additionally, a steel bushing is shrink-fitted between the two setups using liquid nitrogen. By now, the system is fully integrated into the network and can be accessed via the intranet and internet.
Central contact with know-how in pallet automation
Frequently, the wish to reduce setting times and manufacturing for just-in-time assembly are the requirements that result in automation. The solution Siemens AG in Ruhstorf initially envisaged was a simple pallet magazine. In the end, the project developed into an integrated system comprising three HELLER mill/turning centres model CP 2000 and an MLS-LD Multi-Level-System for a total of 72 machine pallets and two high-precision setting stations. Since then, the central pallet handling with integrated loading and unloading stations and the associated host computer with the relevant software ensure that the operators, especially those at the setting and loading stations, know what to do next. Current jobs to be processed are already provided in the software before start of production. In this specific case, the software is able to plan production three shifts ahead. As a result, the operator receives all relevant information about the entire production planning, including all setting data required, before the start of a shift.
The people responsible at the Rohde & Schwarz Teisnach location are constantly looking for innovation and ways to achieve shorter cycle times. In addition to approx. 4,000 parts that have recurred over the last 30 years, the company also produces an extremely wide range of variants, most of which have to be available at very short notice. Therefore, flexibility, consistency and output have top priority throughout every benchmark phase as the company wants to mitigate fluctuations in utilisation with job order processing whilst expanding its know-how. To meet these requirements on a continual basis, the company has linked all 4-axis machining centres model H 2000 with a container solution comprising 12 pallets each and is currently manufacturing in 3-shift operation, 24 hours a day, six days a week. Most of the components are cubic parts, including aluminium high-tech casings.
So, in summary, HELLER is meeting users’ demands for modern automation solutions for machining centres in all respects. Unmanned machine operation or operation during 8,760 hours/year ensure maximum availability and productivity whilst helping to cut per-piece costs. By now, quite a number of workpiece and pallet handling specialists have become well-established in the market that HELLER co-operates with as part of a best-in-class partnership.
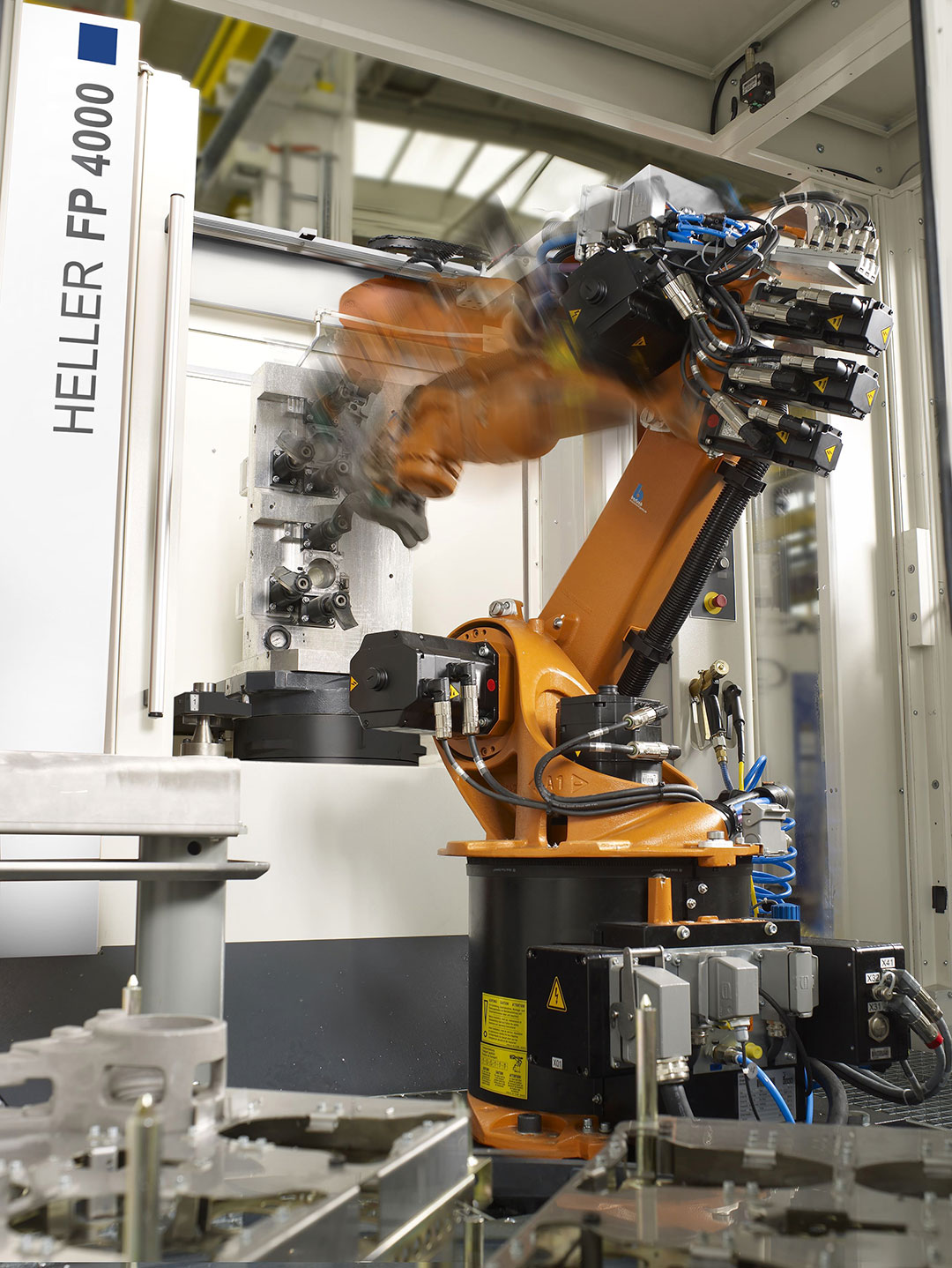
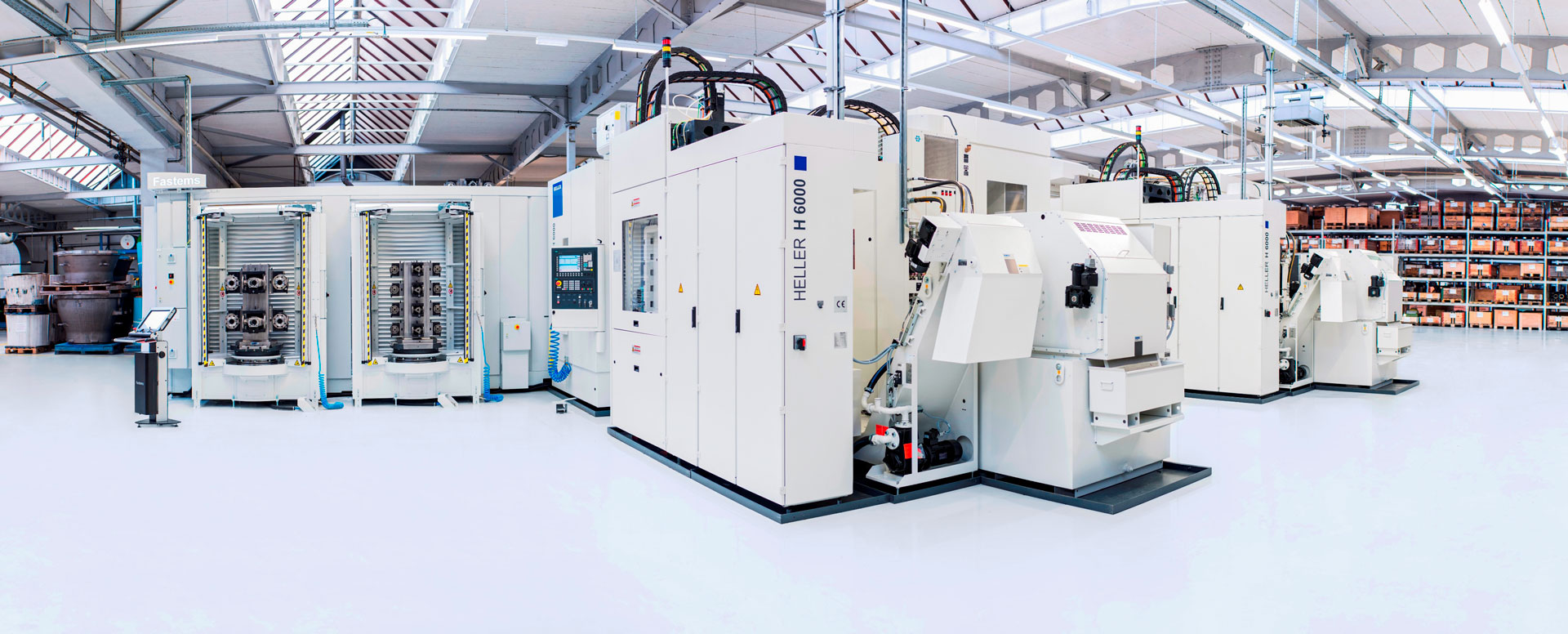