Promoting an agile climate for innovation, supporting ideas and involving employees from all functions
TEXT Martin Ricchiuti
Over the decades, HELLER has continued to expand its technological portfolio, aligning it with production-related challenges in close cooperation with its customers. It is not for nothing that HELLER machine tools are considered a guarantee for an exceptionally high level of production performance, productivity and efficiency combined with economically attractive operating costs. These characteristics and the technical maturity of the solutions have consolidated HELLER’s position as a global partner for highly productive manufacturing machines and systems. Over the years and decades, the company has strengthened its partnerships with companies from general mechanical engineering, the aerospace industry, power engineering, contract manufacturing and many other sectors. Partnerships with the world’s largest automotive manufacturers have grown into solid relationships that continue to surprise with innovations for the benefit of the users.
To this day, no reliable statements can be made about the drive and energy supply technology of the future due to the uncertainty about the concept favoured going forward. All this has caused upheavals in the automotive industry and power industry in particular. Therefore, the alignment of all development efforts to the current situation would lead to a one-sided approach and consequently to a narrowing of the perspective on the wide spectrum of innovation potentials. For HELLER, the development described does by no means provide a solid foundation for determining a strategy for innovation as no final winners have been chosen yet in the race for the drive and energy supply technology of the future – to name just two examples.
Yet, how do you make technological quantum leaps making it easy for companies and users to opt for HELLER as a partner for projects involving highly productive metal cutting with highest requirements on precision, quality and automation?
Bernd Zapf, who has been with HELLER since 1985 and who is responsible for Development New Business & Innovations, provides insights into the various innovations in his field of activity at HELLER. One of the achievements he and his team are responsible for is the in-process coating of cylinder bores, known as HELLER CBC (CylinderBoreCoating): in car engine production, this technology has resulted in a significant reduction in the friction characteristics and CO2 emissions, which in turn contributes to a lower fuel consumption and compliance with environmental standards. The integrated coating technology marks a new standard and has become synonymous with the ‘Made by HELLER’ technological solution competence in passenger vehicle engine production worldwide. The upheaval in the automotive industry, the shift away from the conventional internal combustion engine towards electric drives currently politically favoured, at first glance diminishes future prospects for the commissioning of new engine production lines, for which HELLER was able to win contracts in the past as part of the upstream and downstream production steps of the CBC process.
Another area HELLER believes to be crucial for its customers’ competitiveness and that contributes to the company’s success is the digitisation of production equipment. Under the product name ‘HELLER4Industry’, HELLER brings intelligence into its machine tools and the processes performed on them. Using the collected production data and the data streams generated within the machine tool, HELLER has built a functioning eco-sphere, which, supplemented by cloud technology, creates added value for customers in terms of both availability and productivity. With HELLER4Industry, it is thus possible to ensure the safety and operability of the system during operation and to carry out maintenance at the ideal point in time based on the current utilisation. The transparency gained helps to optimise production in the long term and with increasing precision as the volume of data increases. By consistently revealing the potential for improvement, users are able to identify cause-effect chains and make their production resilient.
These capabilities enable HELLER machines to master current production challenges with the reliability, quality and cost efficiency HELLER is known for.
Innovation processes as a compass for new business areas
In the course of the transformation process in the automotive industry that fully affects HELLER, the company strives to integrate all available sources into the company in order to make the best possible use of new and reorganised capacities. For this purpose, the machine builder is expanding its innovation process with the aim of evaluating current and future changes in production processes from different perspectives in an open and technology-neutral manner. This allows to explore potentials for the company and its customers without bias, which, in a scenario analysis, also extend beyond the previous focus on metal-cutting processes.
Bernd Zapf explains: “The last major project, HELLER4Industry, has been completed from the point of view of pre-development and has been handed over to Product Development to reach product maturity. Going forward, the supplemented innovation development area New Business & Innovations will devote itself exclusively to the new topics in the context of drive technology and energy supply. The next steps for the coming four to five years are already on our horizon. For this, we are considering various scenarios. However, we are not yet able to say with absolute certainty that they will actually materialise exactly that way. We have to learn to deal with this volatility and have to make our development approaches accordingly agile and comprehensive.”
In order to be even more broadly positioned than before and, above all, to systematise the development and exploration of new subject areas, Development New Business & Technology was expanded to include the functions ‘HELLER Transfer of Ideas (HIT)’ and the newly created ‘HELLER Innovation Lab (HIL)’ on 1 July 2021. In the course of this process, the division was renamed ‘Development New Business & Innovations’. With the name ‘Innovations@HELLER’, HELLER wants to highlight the synergies contributing to the ideation process through these functions and give them a new format.
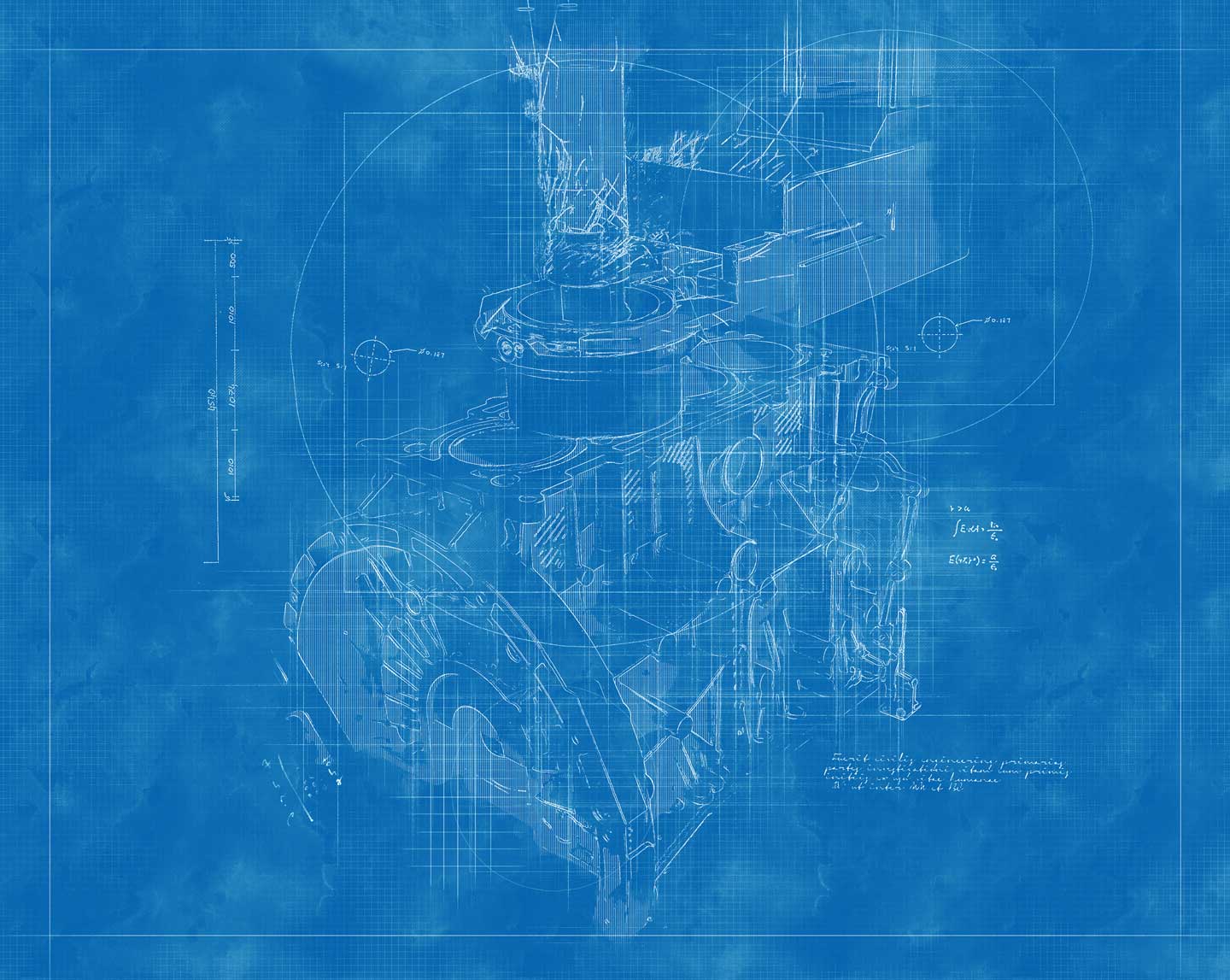
HELLER Transfer of Ideas (HIT) – a bottom-up approach to improvements
The foundation for internal suggestions for improvement was laid many years ago with the HELLER Transfer of Ideas (HIT). Based on their daily proximity to work processes, employees generate suggestions of their own aimed at internal optimisation measures and process improvements. The goal of HIT is to use the creativity and ideation potential of our employees to gradually improve our processes, to avoid anything unnecessary and to increase profitability to the benefit of our company.
HIT ideas mostly focus on areas such as material and labour time savings, work processes and procedures, quality and environmental aspects, as well as occupational safety and motivation. Long-time HELLER employee Josef Tischer coordinates the company’s suggestion system, channels and categorises ideas, allowing them to be processed, evaluated and implemented as needed in accordance with a clearly defined scheme. To speed up the process, the employee suggestion system was upgraded in 2020 with a web-based process in the HELLER intranet. The digital version allows the idea contributors to select the ‘type’ of proposal they are making, i.e. an idea with or without a solution. In addition, it is now also possible to work on suggestions collaboratively as a team. All employees have the opportunity to get involved in this process as contributors, participants or experts. Another new feature is the option to submit ideas without suggesting a solution, which means that they only point out a problem. In such a case, the internal ‘HIT fire brigade’ is called in. It allows colleagues to contribute creative solutions or to point out existing solutions that are already being used or implemented to the same effect elsewhere in the company. The stages a proposal goes through as part of the improvement process are clearly defined so that the contributors of ideas are kept informed about the status of their ideas.
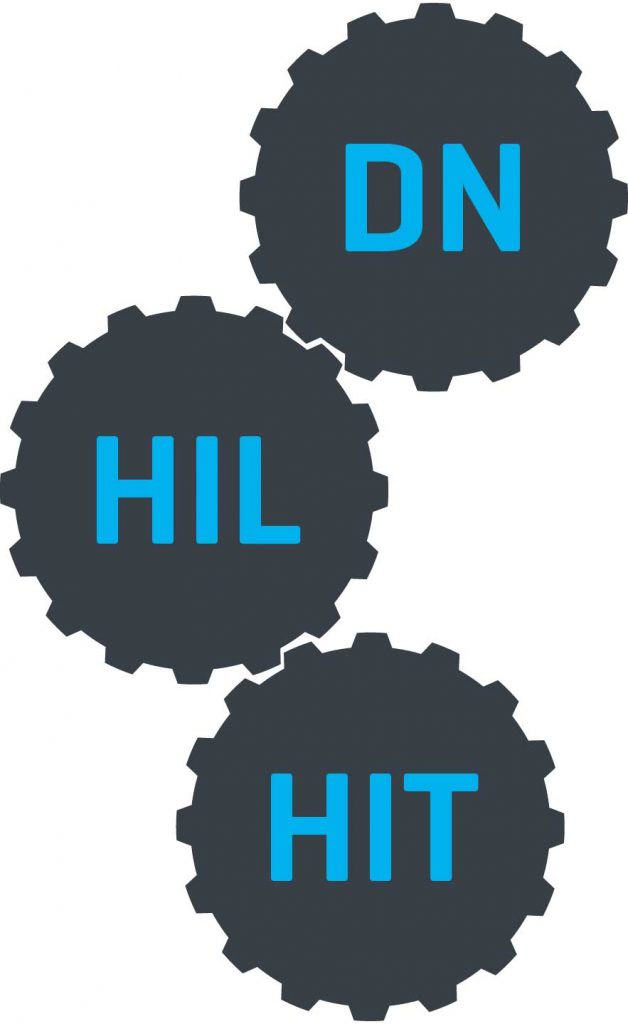
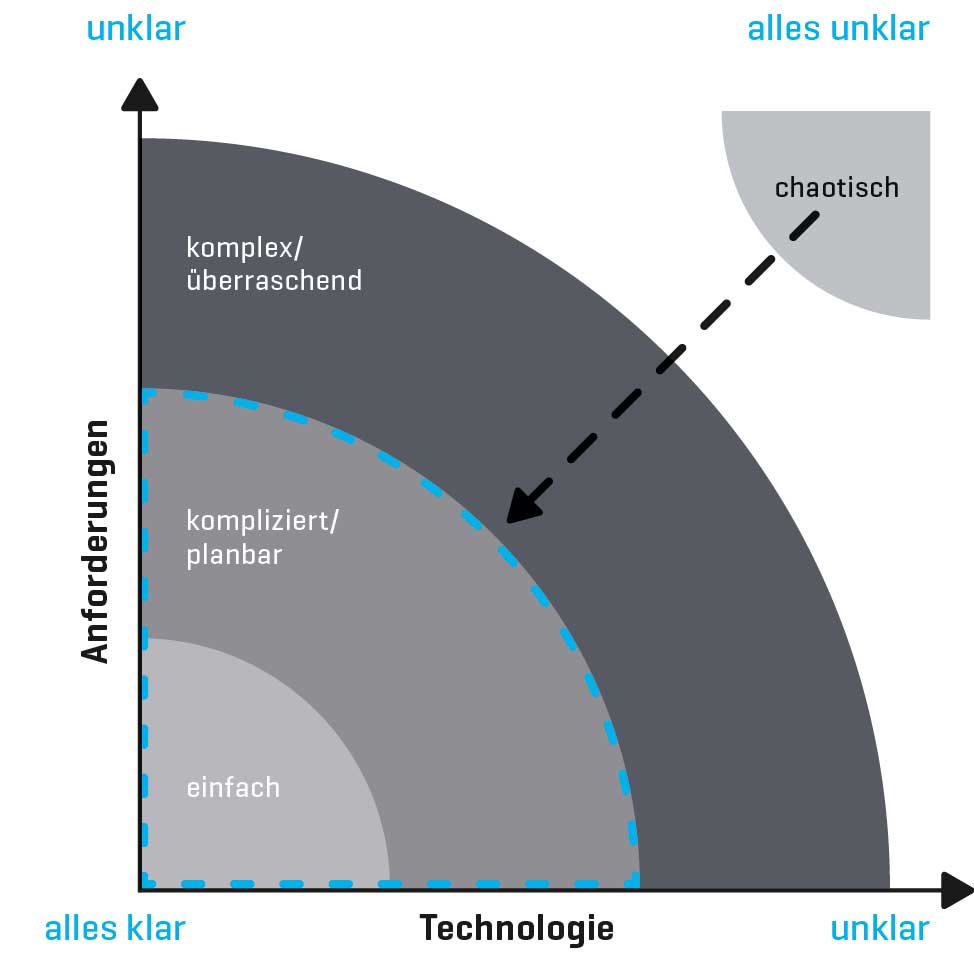
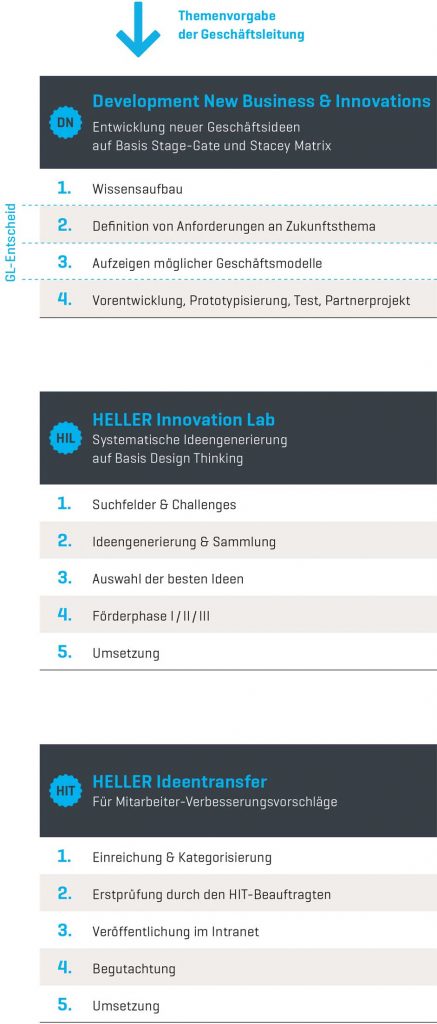
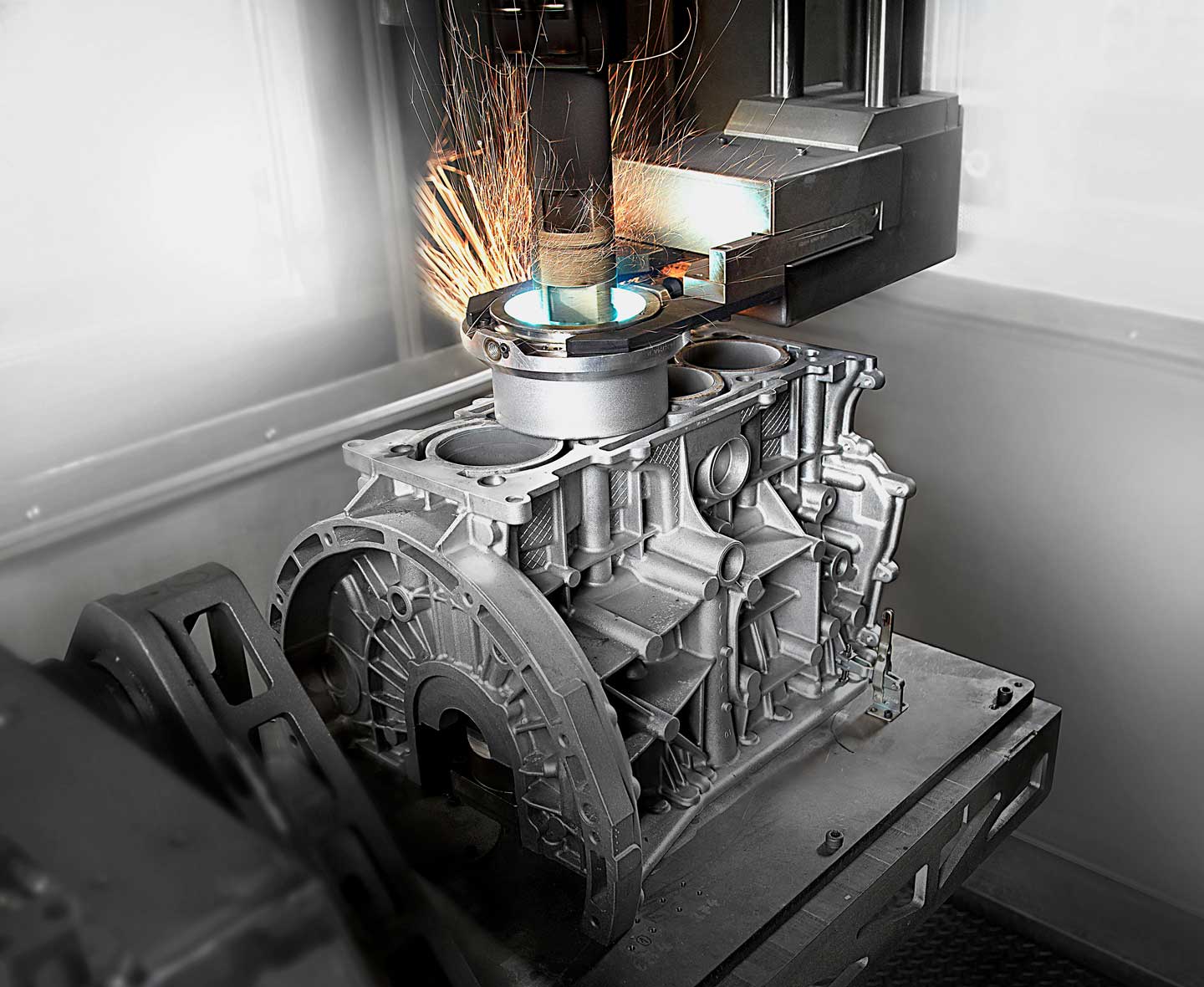
HELLER Innovation Lab (HIL) – the company’s own ideas incubator
The third function involved in the process is the HELLER Innovation Lab (HIL), which acts as a connecting link in the interplay of the Development New Business (DN) and HELLER Transfer of Ideas (HIT) functions. HIL can be regarded as a kind of ‘natural reserve’ for innovative ideas focusing on products and business models. Here, the idea of a ‘positive climate for innovation’ is not an abstract, but something that is implemented in a systematic way. Following the motto ‘Ideation – knowing how it’s done’, an innovation funnel has been set up, giving the business ideas space and time to grow and to mature sufficiently so that they are able to meet HELLER’s criteria for success. Various formats are used to give creativity a boost whilst research into new subject areas is promoted using design thinking methods. Idea workshops and boot camps as well as innovation projects provide interdisciplinary teams of specialists with professional support and coaching that only few start-ups in Germany receive. The ideation process and the selection of the best ideas, in which further resources are invested, is followed by three funding phases before the final presentation to investors. This allows the teams to prepare an ideal basis for the decision-making process after each funding phase to help the steering committee decide whether an idea moves on to the next funding phase. If the idea in question is convincing in the ‘investor pitch’ following the third funding phase, the idea will be implemented. Once an idea has made it to this stage, questions about the added value of the solution, the business model behind it, market potential and size, the competitive situation and financing plan through to the market entry strategy and the team required for it can be answered. The process ends with the third and final funding phase, which is structured individually according to the type of the idea. Depending on the requirements, elements from the first and second funding phase can be examined further or additional technological investigations up to first pilot projects can be carried out. If necessary, interfacing with the Development New Business & Innovations function takes place at this point or the idea is implemented in cooperation with a relevant department.
Two promising ideas have currently made it into funding phase 3 and are currently being piloted individually together with the relevant departments. Preparations for the next iteration of the innovation process have already started. The innovation cycle is further improved with the support of HIL and based on the feedback received from the people involved. Feedback is kept in a steady flow with ideas being generated and implemented in a practice-oriented way throughout different states according to their prospect of success and expected sales potential.
Development New Business (DN): future topics on the horizon
“The development area that has consolidated HELLER’s reputation among its customers as a unique partner providing solution expertise to unlock previously undiscovered manufacturing potential with outstanding inventions such as the above CBC coating technology is currently looking into production-related challenges for the world of tomorrow,” says Bernd Zapf when asked how he would define HELLER’s foresight. In the recent past, the company has regularly set milestones with additive manufacturing, lightweight construction, sensitive clamping technology or the HELLER4Industry Industry 4.0 topic and has expanded its product portfolio in a sustainable way.
A new field HELLER has identified as a forward-looking topic area is in the broadest sense again related to drive technology but also to energy supply solutions. It is based on a single element: hydrogen. The storage and use of hydrogen involves adapted combustion engines or stationary and mobile fuel cells and despite the unclear initial situation, HELLER already foresees new challenges in the area of hydrogen production. In the short term, the application of HELLER’s core competencies and their expansion to new business areas that will play a key role in e-mobility and decarbonisation of the future is based on the company’s existing core competencies such as metal cutting and automation. In the long term, we will adapt and expand our core competencies to include new technologies. In order for this to be successful, the necessary expansion of competencies receives support from research and university institutions.
The team around Bernd Zapf continues to work on its key skill of production optimisation using artificial intelligence methods. With the latest developments, the refinement and expansion of self-optimising production continues. These include the ‘AutoLearn’ consortium project developed in cooperation with the University of Karlsruhe and other industrial partners as well as projects to improve workpiece quality, OEE and process reliability.
To achieve its goals, Development New Business uses agile development methods that organise the innovation process in accordance with the criteria of Robert Cooper’s Stage-Gate model. In the model, the innovation process is divided into several stages. Results are checked against the milestones or gates achieved. Tasks that are initially unspecific and complex are converted into manageable development units in accordance with the Stacy matrix. Concepts, specifications and a first technical feasibility study for product generation in product and technology development are developed throughout four stages focusing on the development of basic knowledge, matching with HELLER skills, development of business models and development into prototypes, thus ensuring a well-founded basis for the development work.
Innovations@HELLER strengthens DN with HIT and HIL through systematic ideation using new formats. This enables HELLER employees to participate in the innovation process and increases the speed of innovation.
With its new innovation process geared towards future production challenges, HELLER is taking a big step towards remaining the reliable partner for production tasks its customers have come to know and trust. Technology innovations are driven forward wherever they are needed and are being brought to product maturity using systematic processes. The driving force provided by the HELLER employees remains the most valuable resource for venturing into new application areas and achieving future viability for everyone involved – despite, or perhaps because of, the major challenges the industry is facing today.
In this new innovation process, Innovations@HELLER sees itself as a catalyst for new business ideas and believes that all HELLER employees can make a contribution to this process with great ideas. Innovations@HELLER supports and promotes this approach with systematic methods to ensure that all HELLER employees can become part of the innovations.