Like machines,
TEXT Sabine Muth PHOTOS HELLER
Stable foundation – shaped by change and the topology of the location
We are aware of our roots and appreciate their value. They have shaped our development. We are optimally set up at our location and structurally embedded in a way that allows our strength to flow – also and especially in the face of constantly changing challenges. As a result, our customers have been able to rely on innovative technologies and highest quality for 127 years – whilst ensuring maximum productivity. That in turn provides the best foundation for trust and real partnership.
The HELLER Group – managed centrally, positioned close to the markets
With production facilities close to the markets, we can respond optimally to the respective markets and, above all, to our customers’ needs: two plants offering a complete value chain are located in Germany and Brazil, three further plants for final assembly and application installation in England, the USA and, since 2013, in China. We support our customers from a network comprising more than 30 local sales and service subsidiaries worldwide. This network is managed centrally from the Nürtingen location. This is where production strategies, policies, methods and tools are developed and tested in the ‘spirit of lean management’ – and then transferred to the other plants. Therefore, the company is able to guarantee its ‘Made by HELLER’ brand and quality promise across the world.
-
The beginnings
Hermann Heller (1869–1931) establishes the company ‘Hermann Heller Handelsgeschäft und Fabrikation in geschützten Artikeln und Uhrmacherwerkzeugen’ in Nürtingen, trading and manufacturing patented products and watchmaker’s tools. At the beginning, HELLER produces chimney heads, spiral stairs, parallel jaw vices and other tools.
-
From trade business to machine factory
In 1913, the first apprentice workshop is set up in Nürtingen. 1938 sees the canteen first opening its doors and the company doctor taking up his work.
In 1942, the company starts to equip HELLER machine tools with hydraulic controls and expands the portfolio with crankshaft milling machines. In 1949, the product range is expanded by heavy bench-type milling machines, special-purpose machines and manufacturing lines in modular design.
-
Developing the characteristic HELLER genes
In 1960, Hubert Heller joins the management of the company, followed by his brother in 1969.
During the time of the so-called Economic Miracle or ‘Wirtschaftswunder’, HELLER produces an increasing number of special-purpose machines and transferlines to meet the growing demand for manufacturing capacities. In 1962, HELLER starts to build numerically controlled milling machines and machining centres with automatic tool changer.
-
Flexible and modular range of machines
The company consistently expands its network with production plants in Redditch/UK and Sorocaba/Brazil (both 1974) and Troy/Michigan, USA (1995).
In 1982, HELLER starts with the series production of BEA machining centres equipped with state-of-the-art HELLER uniPro NC 80 CNC control technology. In the 1990s, HELLER expands its model range, for example, with the MC series of machining centres (1997).
-
Industry 4.0 and digitisation
In 2013, HELLER opens the company’s fifth production plant in Changzhou (China). In addition, the competence network is expanded over the years – most recently with STS Maschinendienstleistung GmbH in Metzingen (Germany).
In 2012, the first CBC modules for the coating of crankcase cylinder bores are supplied to customers.
In 2016, HELLER introduces an enhanced range of solutions for the digitisation of production with ‘HELLER4Industry’.
In 2020, HELLER first the first time welcomes its customers to V-CON, a virtual and interactive international event.
In 2019/2020, the new generations of the H series 4-axis machining centres and the HF series 5-axis machining centres are presented.
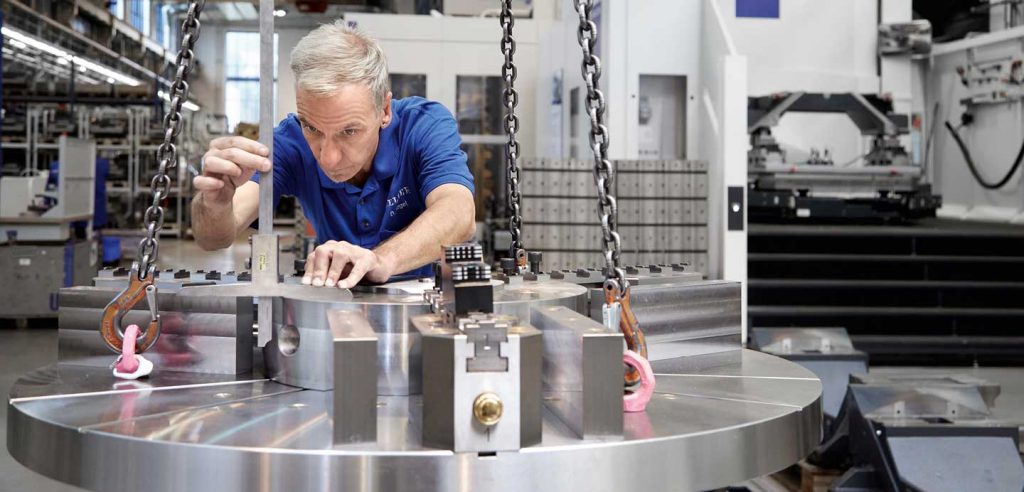
Dynamic kinematics
–
a well-rounded concept thanks to motivated employees
HELLER still has the status and flair of a family business. This is noticeable in the corporate philosophy and in employee loyalty. The large HELLER family provides consistency – especially at the Nürtingen location, where it all began. Despite all stability, the company lives, demands and supports flexibility and dynamism. At our HELLER Academy, we provide excellent technical qualifications with a wide range of advanced training courses by our own and external trainers. In addition, promoting young talent has top priority. The success speaks for itself.
The way employees identify with ‘their’ company is often underestimated.”
Klaus Winkler
„
HELLER takes the development of skilled professionals into its own hands
In 2021, HELLER is training 159 people worldwide in six different apprenticeships. 71.1 percent of HELLER apprentices complete their training at the Nürtingen location. The concept of the HELLER Learning Factory is a role model within the industry. The social projects to teach soft skills such as flexibility, social skills and a sense of responsibility also have high priority.
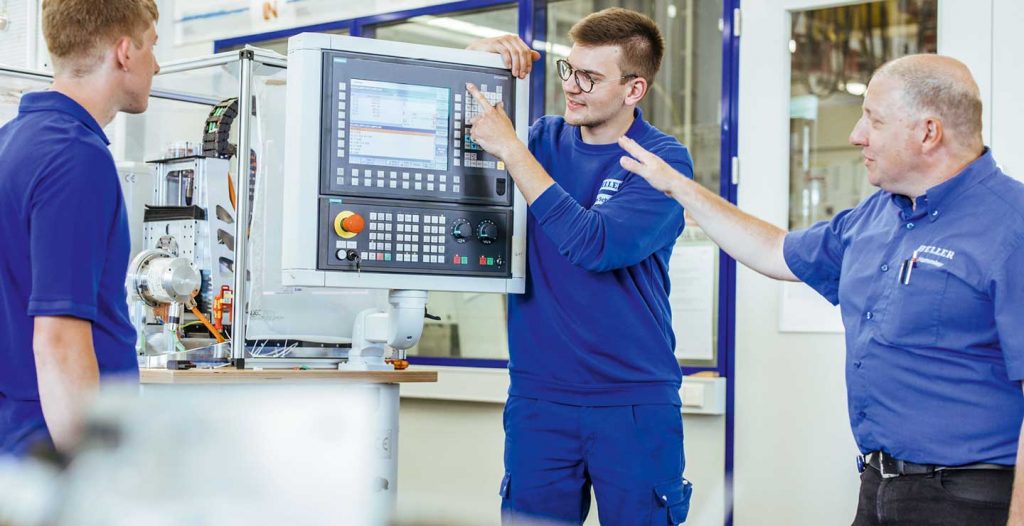
Whoever gained first professional experience at HELLER is well prepared for the next steps:
The HELLER Talent Programme
Particularly in challenging times, HELLER strives to think ahead and relies on the long-term development of specialists and executive staff. The sixth HELLER Talent Programme started in September 2020 with eight participants from different departments. As part of the programme, they have the opportunity to gain practical experience in forward-looking projects, for example: ‘Rotary table assembly line at Plant 2’, ‘Upgrade of control of inspection, measuring and test equipment at HELLER’ plus six further projects..
“The colleagues were really willing to take some time out to work on my project”
Michael Stippler took part in the 6th HELLER Talent Programme – and is enthusiastic about what he experienced in theory and practice during the 8 months. The goal of his project was to develop a concept for the rotary table assembly line at Plant 2 in order to reduce the cycle times of customer-specific manufacturing orders and to improve capacity utilisation at HELLER. The basic idea: neutral pre-assembly. The result: with neutral pre-assembly, the cycle time required for a manufacturing order is now almost 70 percent below the initial time. Precisely timed material deliveries using picking carts and Kanban have resulted in a 20 percent reduction in assembly time. The management was also extremely satisfied with the results achieved.
„In the development of this concept, I closely worked with staff in Assembly. That allowed us to get quicker and better results – also in terms of the implementation.“ .
Michael Stippler
„
Powerful drive
–
with ideas and innovative strength
Our innovation motor is driven by our employees and vigorously pushed forward. We are heading towards the future with foresight and confidence, never losing sight of the trust our customer place in us. To achieve this, we are working on various levers in different areas.
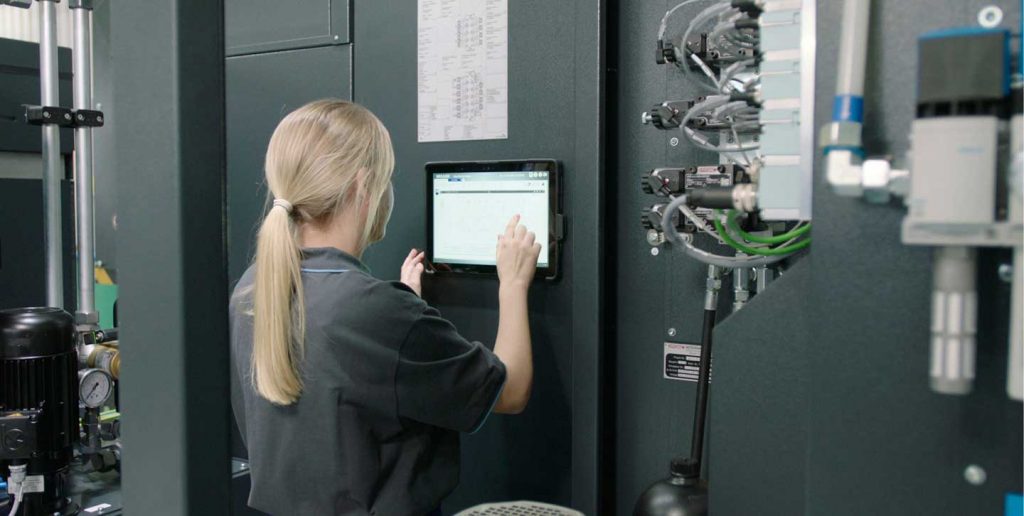
Innovation Shopfloor Interface – working together to drive digitisation in assembly
An interview with Ralf Fauser, Process Organisation at HELLER
Mr Fauser, could you explain in a few sentences what the Shopfloor Interface is all about?
The SFI is an application that has been developed in close cooperation between our IT’s application developers and Assembly as part of an agile process. It has been tailored to the specific needs and is very easy to use; it runs on a tablet computer and offers the user a 360° view of all the data relevant for the machine and the assembly process.
A 360° view? Does that mean that the operator can call up all relevant documents and no longer has to print them?
Yes, that is one of the benefits, but the SFI is not just about documents. It focuses on the entire assembly process and all of the data related to it. It allows display of assembly instructions, parts lists, electric diagrams, fluid layouts, design drawings etc., but also the recording of serial numbers and measured values for the quality process as well as the confirmation of completion, which in turn starts a logistics process.
Sounds complicated. Do the users find it easy to work with the system or were there reservations?
They have been involved in the development process from the very beginning. Acceptance is therefore very high and the colleagues regularly contribute new ideas – it is an agile system after all.
Does that mean the system can be expanded and adapted?
Exactly! For example, we are currently working on a time confirmation module for jobs in order to eliminate the need to walk to the booking terminals, allowing all tasks to be performed using the tablet computer. This is a perfect example of our user-centred approach with the SFI – usability is enhanced and processes are optimised while productivity is increased.