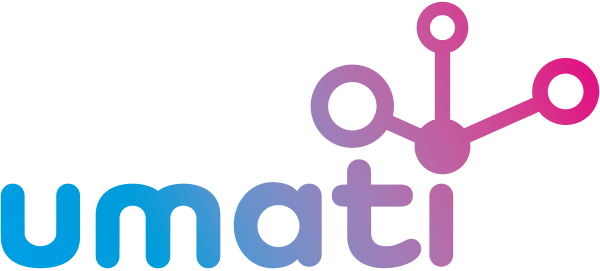
Die Digitalisierung der Fertigung schreitet immer weiter voran. Bislang erschweren proprietäre Systeme die Verknüpfung mit unter- und übergeordneten Steuerungsebenen. Eine vom VDW gestartete Initiative hat es mit umati geschafft, einen international akzeptierten Standard für eine Schnittstelle zum Datenaustausch zu erarbeiten.
TEXT Martin Ricchiuti BILDER VDW, Ansgar Pudenz
Jeder, der sich mit der Verknüpfung von industriellen Anlagen beschäftigt – sei es eine vertikale Integration mit übergeordneten Systemen oder eine horizontale Integration von gleichrangigen Partnern – muss sich eingehend mit der Kompatibilität der unterschiedlichen Steuerungen und Schnittstellen befassen. Denn über Jahrzehnte haben diverse Hersteller und Dienstleister eigene, proprietäre Ansätze verfolgt, die ihnen für den jeweiligen Anwendungsfall geeignet erschienen. Im Ergebnis entstehen heterogen gesteuerte und verknüpfte Maschinenparks, die zwar nach erfolgter Installation ihre Leistung liefern, aber bei jeder Änderung der ursprünglichen Konfiguration erneut einen hohen Integrationsaufwand fordern.
Die Auswirkungen dieser fast schon babylonischen Sprachverwirrung spüren Unternehmer gerade im Umfeld der zahlreich gestarteten Digitalisierungsinitiativen besonders deutlich. Denn wer Daten aus seinen Systemen extrahieren möchte, muss diese vorher zusammenführen und vereinheitlichen. Sonst gelingt es nicht, über Systemgrenzen hinaus Analysen vorzunehmen. Diese Problematik stellt sich laut Bernd Zapf, Leiter Development New Business & Technology bei der Gebr. Heller Maschinenfabrik GmbH (Foto S. 51), bereits bei der Verknüpfung einer Maschine mit einer MES-Software: „Wir haben eine standardisierte und umfassend dokumentierte Schnittstelle. In der Praxis entscheidet sich dann, ob wir unsere Schnittstelle an die Bedingungen des Kunden anpassen – oder umgekehrt. Im ersten Fall entstehen uns regelmäßig Aufwände, die Kapazitäten binden und eine reibungslose Integration erschweren. Ein Umstand, der uns bei fast jeder verkauften Maschine begegnet. Im zweiten Fall trägt der Automations- oder Softwarepartner den Anpassungsaufwand.“ Das lässt erahnen, mit welcher Komplexität der Hersteller von Werkzeugmaschinen bei der Integration konfrontiert ist – und welches Know-how er in den vergangenen Jahren aufgebaut hat.
Einheitliche Maschinenschnittstelle macht den Weg frei für Datenaustausch
Zapf begrüßt die vom VDW gestartete Initiative, eine einheitliche Maschinenschnittstelle in enger Zusammenarbeit mit den Werkzeugmaschinenherstellern auszuarbeiten, ausdrücklich: „Wir sind lieber in der Rolle des Gestalters, um unsere Vorstellung von einer universalen Kompatibilität verschiedener Maschinen, Aggregate und Software zu forcieren.“ Als sogenannter Core-Partner der frühen Stunde hat HELLER maßgeblich die Ausarbeitung der umati-Schnittstelle mitgestaltet.
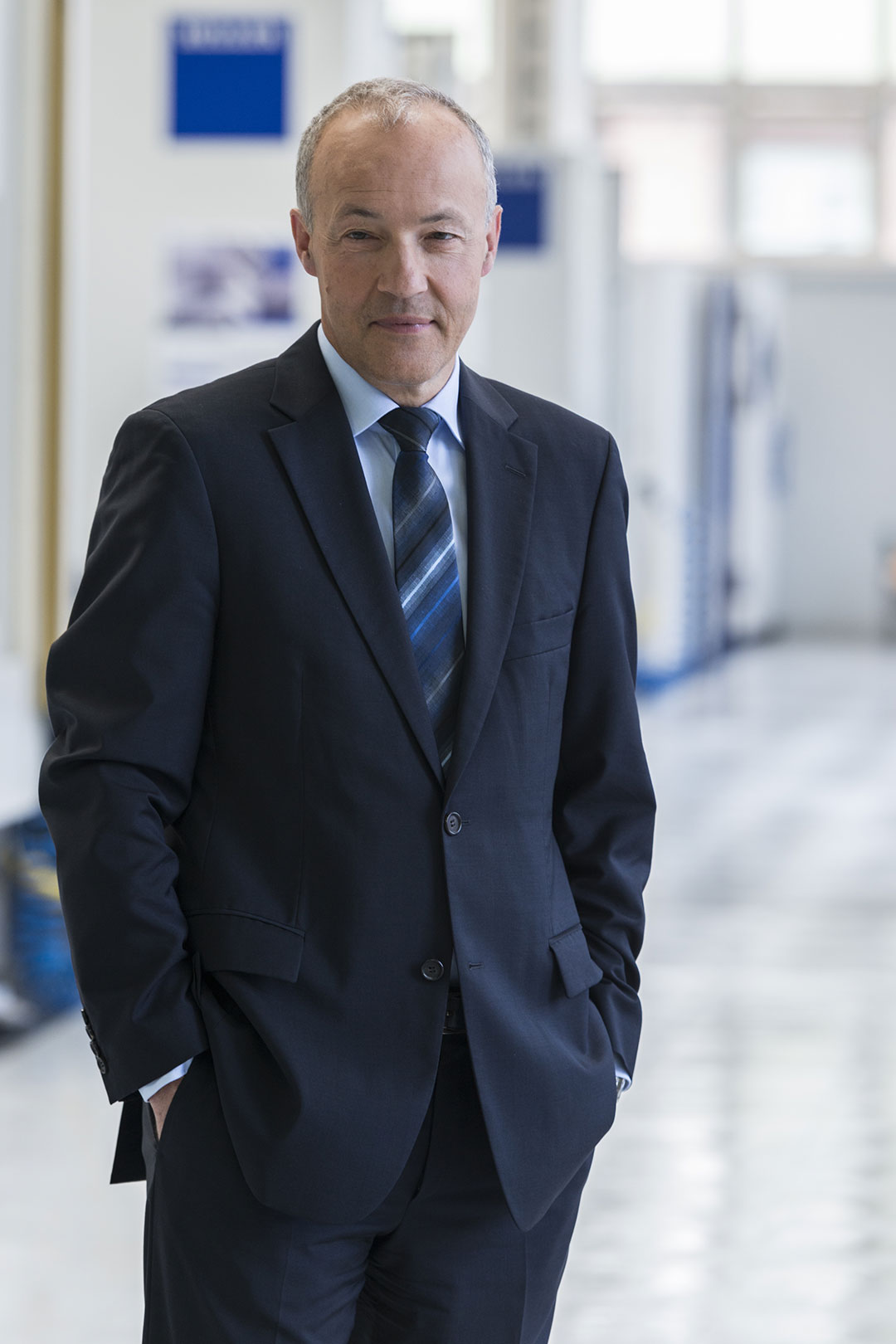
Grundlage des umati-Standards ist der vom VDW 2006 entwickelte OPC-UA-Server. Der als „Übersetzer“ fungierende OPC-UA-Server transformiert die unterschiedlichen Datenformate, die die CNC-Steuerung, das HMI oder andere Datenquellen liefern, in klartext-codierte Signale. Die Kommunikation wird so auf einer rein formalen Ebene deutlich vereinfacht. Zapf macht dies an einem einfachen Beispiel deutlich: „Wenn Sie den Maschinenstatus abfragen wollen, genügt die Frage: Wie lautet der Maschinenstatus? Die Antwort wäre ebenso im Klartext einfach verständlich. Vor umati wäre die Frage ebenso kryptisch wie die Antwort ausgefallen. Das erhöht den Bedienkomfort und natürlich auch die Benutzerakzeptanz.“
„Ein weiterer entscheidender Vorteil des umati-Projekts ist seine Transparenz“, weiß Bernd Zapf zu berichten. „Im Unterschied zu früheren Standardisierungsbemühungen ziehen in der gegründeten „Joint-Working Group“ alle an einem Strang. Das bedarf auch einer gewissen Kompromissbereitschaft, damit ein tragfähiger Konsens und damit der Fortschritt des Projekts sichergestellt werden. Die Einbindung von Steuerungsherstellern aus Japan oder der nordamerikanischen MQTT-Initiative unterstreicht die Reichweite und Bedeutung der Standardisierungsbemühungen seitens umati.
Dabei funktioniert umati wie eine Straßenverkehrsordnung – wenn sich jeder an die Regeln hält, klappt der Datenaustausch reibungslos und sicher. Gleichzeitig ist das vom VDW geleitete Projekt für viele verschiedene Maschinenhersteller offen. Es können also Unternehmen aus verschiedenen Branchen teilnehmen, die wiederum Anforderungen an Datensignale haben, die etwa in der Metallbearbeitung unüblich sind. Vom Austausch mit diesen Branchen können auch neue Impulse für den Werkzeugmaschinenbau abgeleitet werden. Dieser unterschiedliche Datenbedarf wird zukünftig trotzdem von umati abgedeckt. Für HELLER ergibt sich daraus der Vorteil, dass für die Bereitstellung der Daten der OPC-UA-Server für die umati-Kommunikation nur konfiguriert und nicht programmiert werden muss. Zapf betont dabei: „Wir als Heller haben uns dafür entschieden, die gesamte Transformation außerhalb der Steuerung zu realisieren, um die Maschinensteuerung unangetastet zu belassen. Dafür kommt das Edge-Computing in Form der Sinumerik Edge zum Einsatz: Auf der kleinen grauen Box wird der OPC-UA-Server installiert. Wenn dies für den benötigten Signalumfang bereits ausreicht, genügt diese Installation. Wird ein größerer Signalumfang gewünscht als der bisher in der Steuerung vorhandene, installieren wir zusätzlich die Transformation-Engine und können so den umati-Standard erfüllen.“
Diese Konfiguration kann übrigens bei bereits bestehenden HELLER Maschinen, die den Edge-Computer nutzen, ohne Aufwand nachgerüstet werden. Auch in Zukunft sind Kunden, die ältere Maschinenmodelle betreiben, durch den zusätzlichen Edge-Computer hochrüstbar und so auf der sicheren Seite.
Standardisierung wo nötig, Flexibilität wo möglich
Die breite Zustimmung zur Standardisierung nach umati ist nach der Überzeugung von Zapf der Herangehensweise geschuldet, die sich Funktionen aus dem Bereich der Social Communities zunutze macht: „Je mehr mitmachen, desto breiter wird die Akzeptanz. Und gelebte Kompromissbereitschaft sichert die Zustimmung aller. Inzwischen interessieren sich auch China, Japan und die USA für diesen Standard – das ist ein Traum, der bis vor Kurzem noch undenkbar gewesen wäre.“
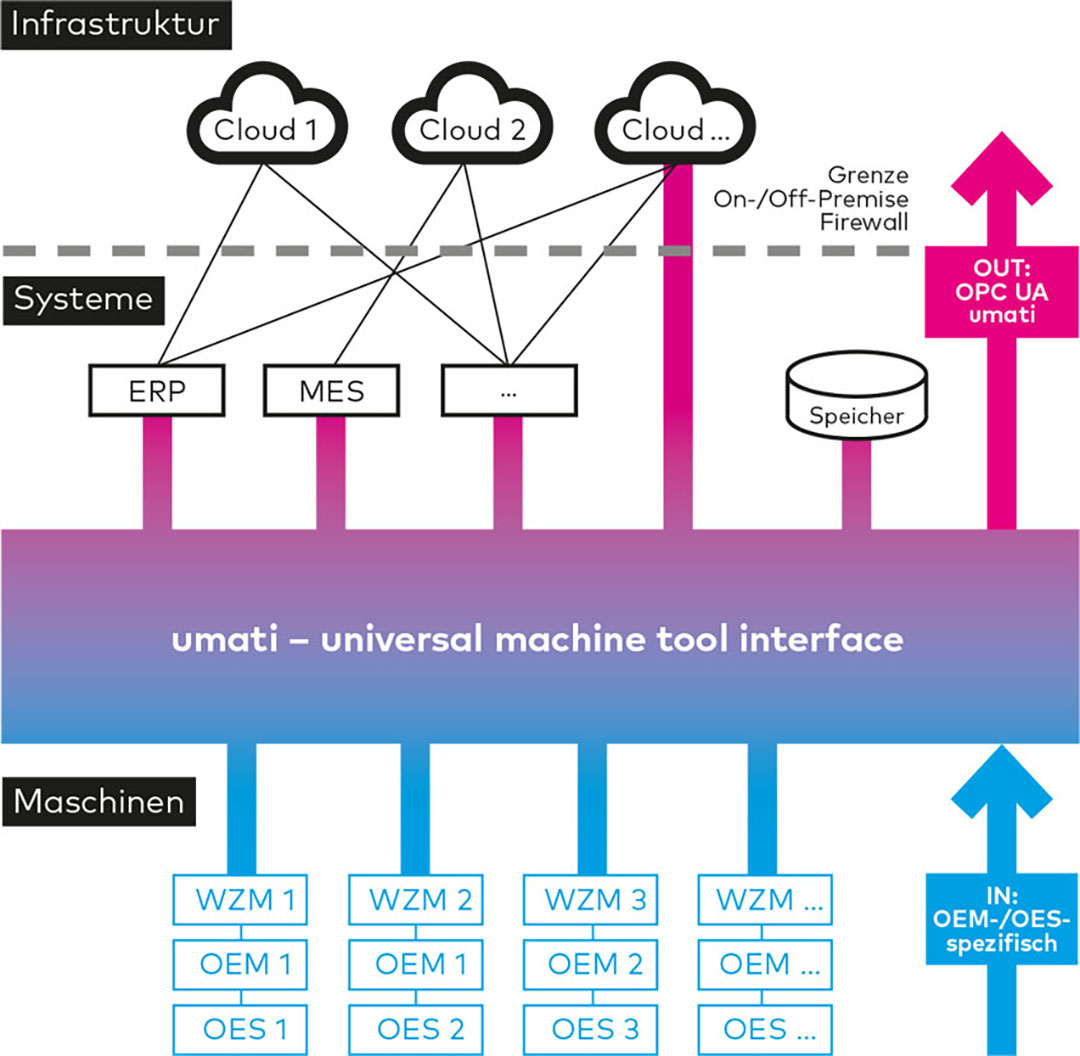
Aber welche Vorteile ergeben sich für Anwender?
Der Anwender hat den Vorteil, dass er verschiedene Systeme ohne hohen Aufwand koppeln kann. Das gilt für unterschiedliche Maschinentypen vom Werkzeugvoreinstellgerät über eine Messmaschine, von der Entgratzelle über die Teilereinigung bis hin zur Werkzeugmaschine und Peripherie-Aggregaten.
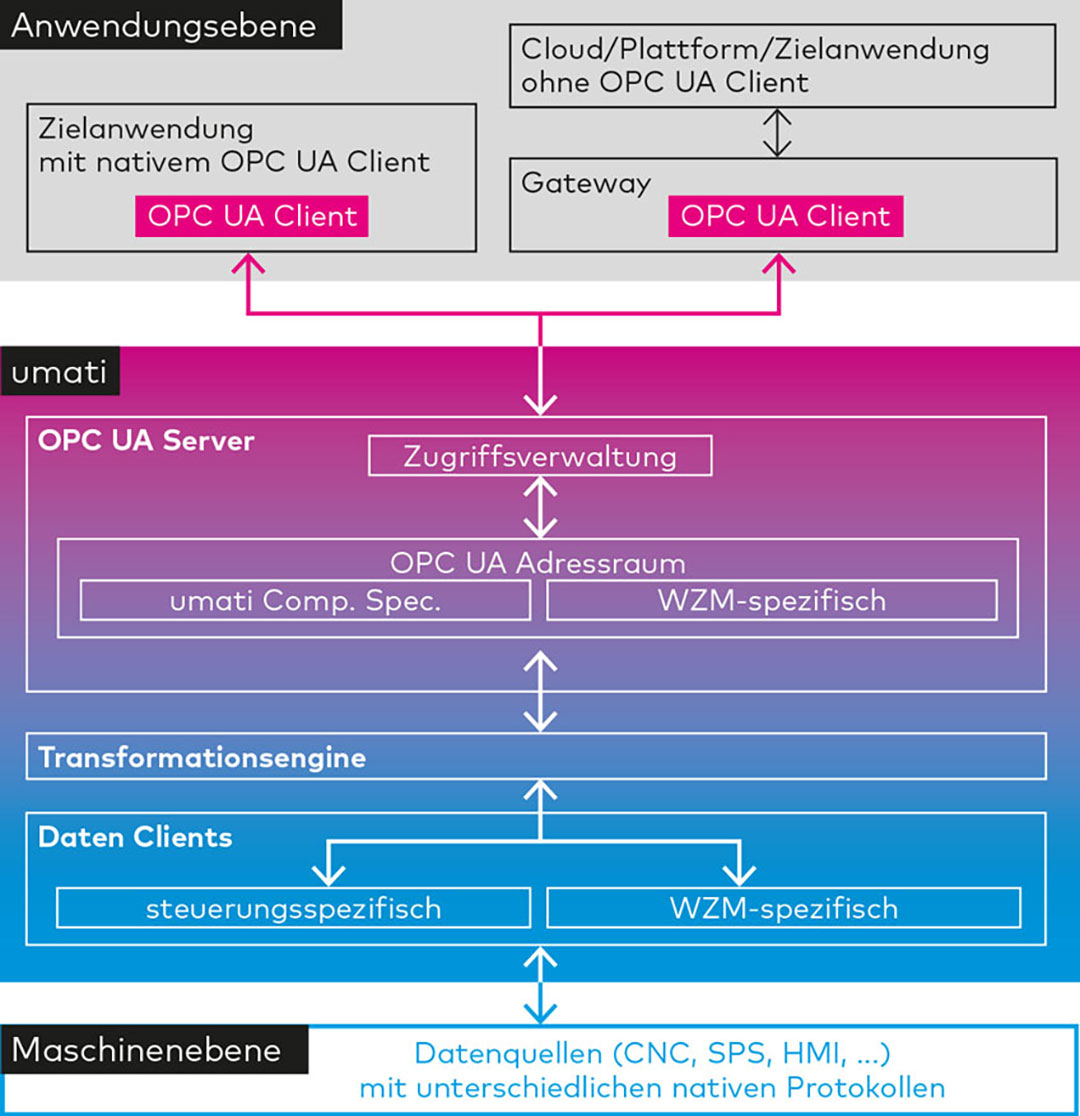
Um die Funktionsweise von umati zu veranschaulichen, wird HELLER auf der EMO verschiedene Use-Cases präsentieren. Der Nürtinger Werkzeugmaschinenbauer wird insgesamt vier Datenlieferanten mit dem EMO-umati-Datenmodell auf der Messe zur Verfügung stellen: eine 5-Achs-Maschine auf dem HELLER Stand, zwei Schulungsmaschinen, von denen eine auf dem VDW-Stand ausgestellt wird und eine weitere 5-Achs-Maschine, die allerdings in der Fertigung in Nürtingen steht und von dort aus ihre Daten sendet.
An einem anderen Beispiel aus dem Toolmanagement wird die Kompatibilität der umati-Schnittstelle deutlich: Erfolgt die Abfrage aller erforderlichen Werkzeuge für eine Bearbeitungsoperation über umati, können Maschinen unterschiedlichen Typs oder Herstellers ihre „Antworten“ an das übergeordnete Steuerungssystem übergeben. Da zurzeit erst ein Teil der Anforderungen an die neue Schnittstelle abgearbeitet ist, stehen Anwendungsbeispiele aus der Maschinendatenerfassung derzeit im Vordergrund. Dazu wird HELLER seine bisherige MDE/BDE-Schnittstelle ebenfalls in das umati-Datenmodell integrieren, sodass auch diese bisherige Schnittstelle per umati problemlos mit MES-Systemen verbunden werden kann.
Mit umati und seiner breiten Marktakzeptanz, die auf der Einbindung vieler unterschiedlicher Stakeholder wie Steuerungshersteller, Maschinenbauer und Softwareanbieter beruht, rückt das Ziel des „Plug-and-Produce“ in greifbare Nähe – im Hinblick auf Industrie 4.0 und die Digitalisierung der Fertigung ein enormer Schritt nach vorn.