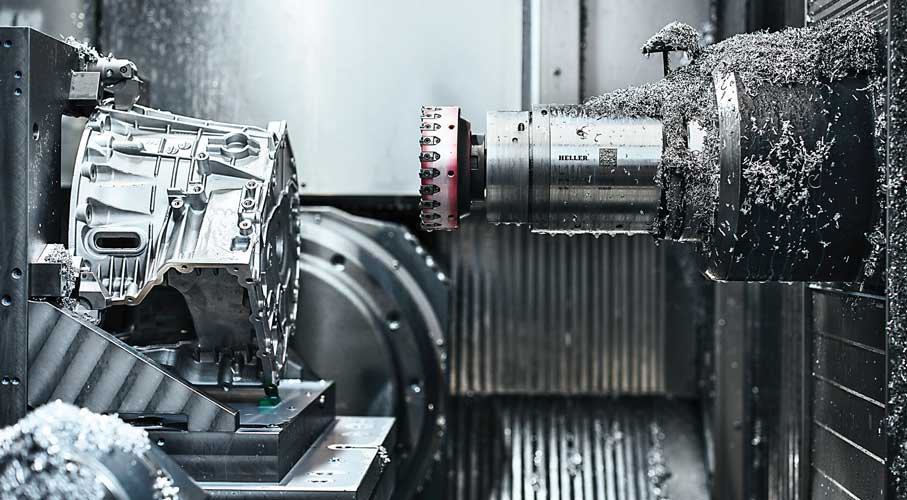
TEXT Manfred Lerch FOTOS Sebastian Grenzing
Den Einsatz der ersten 5-Achs-Bearbeitungszentren der Baureihe HF, mit der 5. Achse im Werkstück, sah HELLER noch überwiegend bei mittleren Losgrößen in der Serienproduktion. Mit der Entwicklung der zweiten Generation hat sich dieser Einsatzbereich nun deutlich erweitert. Beim Unternehmen Stöferle werden auf zwei HF 5500, eingebunden in eine Fertigungslinie, bis zu 350.000 Bauteile pro Jahr gefertigt. In drei Schichten geht der Zulieferer der Automobilindustrie dafür kontinuierlich an die Grenzbereiche der Bearbeitungszentren und ist überzeugt, dass diese eine Investition in die Zukunft waren. Darüber hinaus hat Stöferle auch in die mittlerweile vierte Generation der vierachsigen Bearbeitungszentren der H-Baureihe investiert.
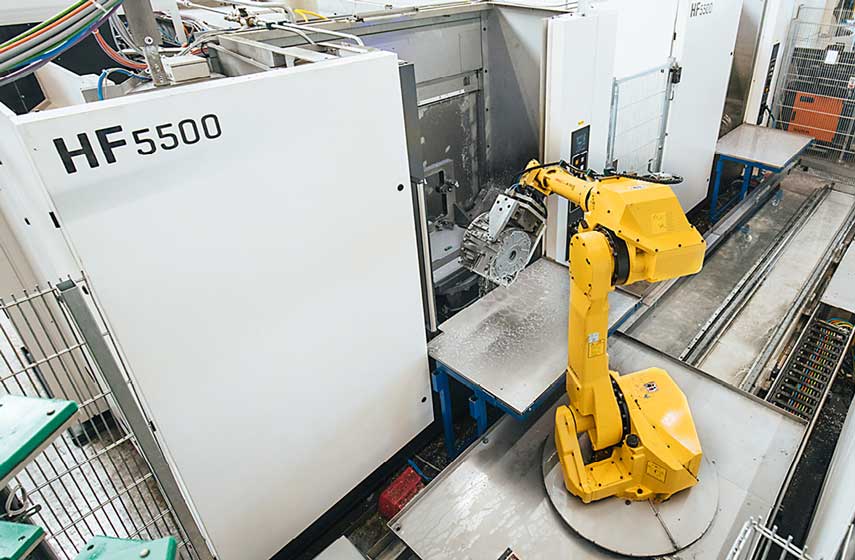
Mit der Entwicklung alternativer, CO₂-freier Antriebsformen in der Automobilindustrie sieht sich das Unternehmen Stöferle in Laupheim seit Jahren konfrontiert. Durch die Einführung der Elektromobilität bzw. der Hybrid-Technologie werden Bauteile komplexer. Außerdem steigen die Anforderungen an präzise und zunehmend schräge Flächen sowie an hochwertige Oberflächen. Für Großbauteile mit Passungen zwischen H6 und H7 bei Durchmessern zwischen 240 und 320 mm für Mild-Hybrid-Modelle war man deshalb 2019 auf der Suche nach entsprechenden Bearbeitungszentren. Investiert hat man in zwei 5-Achs-Bearbeitungszentren HF 5500 der zweiten Generation von HELLER.
Nun befindet sich Stöferle allerdings in einer besonderen Situation. Zum einen entwickelt das Unternehmen selbst Sondermaschinen. Zum anderen erprobt man als Partner von HELLER Bearbeitungszentren in Mittel- und Großserien, dreischichtig, sieben Tage die Woche. Für Geschäftsführer Erich Stöferle sind das echte Härtetests: „Wir fahren mit den Maschinen, auch mit der HF-Baureihe, immer am Maximum. Das heißt, wir reizen die von HELLER vorgegebenen Leistungsgrenzen bis auf zehn Prozent aus. Ist das Maximalgewicht eines Fräsers mit 16 kg definiert, gehen wir bis 15,5 kg. Das machen wir schon seit Jahren. Ein Fräser Ø 160 mm läuft bei uns beispielsweise mit 15.000 min⁻¹. Das mag bei der Einzelteilfertigung kein Problem sein, aber bei uns produzieren wir dreischichtig. Ein weiterer Aspekt ist, dass diese beiden HF 5500 Bestandteil einer Fertigungslinie mit fünf bis sechs Maschinen sind und die Losgrößen zunächst mit 350.000 Stück/Jahr definiert sind. Höchste Zuverlässigkeit und Verfügbarkeit ist bei uns deshalb eine Grundvoraussetzung.“ Die HELLER Gene Produktivität, Genauigkeit und Zuverlässigkeit sind demnach auch bei dieser Weiterentwicklung praxisnah umgesetzt.
Deutliche Vorteile gegenüber der ersten Generation sieht man in Laupheim bei den neuen HSU-Inline-Spindeln, die absolut Made by HELLER sind. Diese Spindeln zeigen sich im Spindelschwingverhalten wesentlich steifer und überzeugen mit einem schnellen und kostengünstigen Austausch im Servicefall. Bei den Arbeitseinheiten setzt man bei Stöferle auf die Speed Cutting (SC)-Spindeln mit Drehzahlen von 18.000 min⁻¹ und einem Drehmoment von 103 Nm. Und auch in Sachen Präzision überzeugen die Bearbeitungszentren. In den Parallelitäten bewegt man sich bei den Großbauteilen innerhalb von 2/100 mm, bei Oberflächen und Ebenheit bei WT 6. Diese Toleranzen sind demnach erreichbar. Mehr noch, im Gegensatz zur ersten Generation sind durch die neuen Spindeln deutlich hochwertigere Oberflächen zu erzielen. Eine weitere und sehr wichtige Veränderung sieht Erich Stöferle in der Verkürzung des Abstandes der Spindelvorderkante zur Drehmitte der B-Achse, denn bisher war in Laupheim für die Werkzeuge häufig eine Verlängerung notwendig.
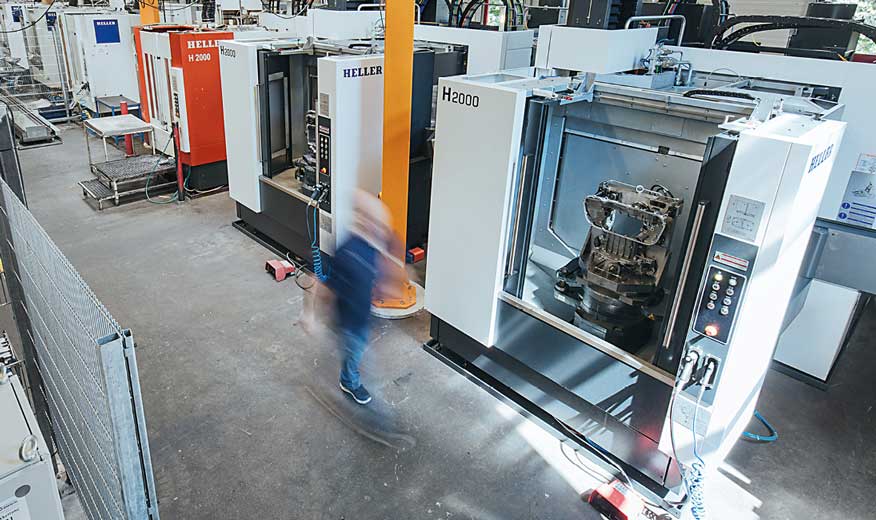
HELLER hat bei der vierten Generation der H-Baureihe in der Dynamik deutlich zugelegt. An konkreten Bauteilen konnten die Span-zu-Span-Zeiten messbar reduziert werden. Deshalb hat man in zwei H 2000 der neuen Generation investiert.
In der 4. Generation Span-zu-Span-Zeiten deutlich reduziert
Feldtests führt Stöferle auch bei der mittlerweile vierten Generation der vierachsigen Bearbeitungszentren der H-Baureihe durch. Seit Februar 2020 wird mit diesen Maschinen in der Großserie am Maximum gefertigt. Für Geschäftsführerin Katja Stöferle ist das eine logische Konsequenz aus den bisherigen Erfahrungen: „Wir verfügen über mehr als 20 Maschinen dieser Baureihe und haben auf mancher Maschine sicher über eine Million Bauteile ohne größere Reparaturen gefertigt. Wir hatten beispielsweise eine H 2000, die 15 Jahre mit ein und demselben Kugelgewindetrieb gelaufen ist. Bei Getriebeteilen mit Losgrößen von 250.000 Stück/Jahr müssen die Stabilität, die Antriebe und die Spanabfuhr einfach stimmen. Um es kurz zu machen, das sind unsere besten Maschinen. Unabhängig davon steigen durch die Elektromobilität nicht nur die Anforderungen bei den Bauteilen, sondern auch die Losgrößen. Deshalb suchen wir kontinuierlich nach Möglichkeiten zur Reduzierung der Stückzeiten. Über die Zuverlässigkeit der neuen Generation der Baureihe H kann man zwar noch nicht viel sagen, aber HELLER hat bei dieser Generation in der Dynamik nochmals deutlich zugelegt, denn an konkreten Bauteilen konnten wir die Span-zu-Span-Zeiten messbar reduzieren. Auch deshalb haben wir wieder in drei H 2000 investiert.“ Für diese Reduzierung der Hauptzeiten, so René Greising von der Gebietsvertretung Hans P. Greising GmbH, ist vor allem das Herz der Maschine, die Spindel, verantwortlich. „HELLER bietet bei dieser Generation drei Varianten an: Power Cutting (PC), Speed Cutting (SC) und neu Dynamic Cutting (DC). Dabei kombinieren insbesondere die DC-Einheiten hohe Drehmomente mit hohen Drehzahlen perfekt.“
In der Summe wurden also beide neuen Generationen aus dem Hause HELLER schon im realen Einsatz auf Herz und Nieren getestet und stehen dem Markt seit Anfang 2021 als ausgereifte Maschinen zur Verfügung.
Die H 2000 war und ist schon immer eine Supermaschine. Da stimmen die Proportionen einfach. Die liegt tief, hat wenig Bewegung im Bett, breite Führungen, eine gute Spindel und läuft im Drei-Schicht-Betrieb über Jahre absolut zuverlässig.
Erich Stöferle
„
In die beiden Bearbeitungszentren hat man für Großbauteile mit Passungen zwischen H6 und H7 bei Durchmessern zwischen 240 und 320 mm für Mild-Hybrid-Modelle investiert.
„Bei Losgrößen zwischen 200.000 und 300.000 Teilen müssen wir hochproduktiv und -flexibel sein. Die Bauteile ändern sich laufend. Da kommen schräge Bohrungen, neue Winkel, die angefahren werden etc. Darauf müssen wir natürlich schnell reagieren können.“
Erich und Katja Stöferle
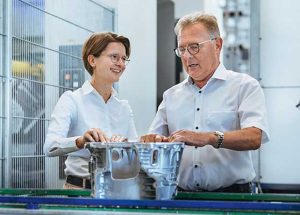
Die Stöferle GmbH wurde 1992 gegründet, beschäftigt 200 Mitarbeiter und konzentriert sich auf maßgeschneiderte, individuelle Lösungen für die wirtschaftliche und schnelle Produktion von Mittel- und Großserien in der Leichtmetallverarbeitung. Dazu gehört auch die Entwicklung von Sondermaschinen. Stöferle ist Partner und Zulieferer der Automobilindustrie. Um Technologietransfer und Synergien noch besser zu nutzen, wurde das Unternehmen mit der Stöferle Automotive GmbH erweitert. In diesem Bereich agiert Stöferle als Systemlieferant. Außerdem stellt Stöferle Teilewaschanlagen, Anlagen für Dichtheitsprüfungen und Montage sowie Zusatzkomponenten wie Spannvorrichtungen, Handling-Systeme und produktionsbegleitende Mess- und Prüfvorrichtungen her. www.stoeferle-gmbh.com
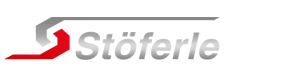