Bei automatisierten Fertigungs- und Produktionszentren geht es überwiegend darum, Nebenzeiten zu reduzieren und damit die Anlagenverfügbarkeit zu optimieren. Die Anforderungen der einzelnen Branchen sind allerdings sehr unterschiedlich, das Angebot entsprechend groß. HELLER ist hier in den drei Hauptgruppen der Automationslösungen völlig offen, wenn es um Produktivität, Verfügbarkeit und Wirtschaftlichkeit geht.
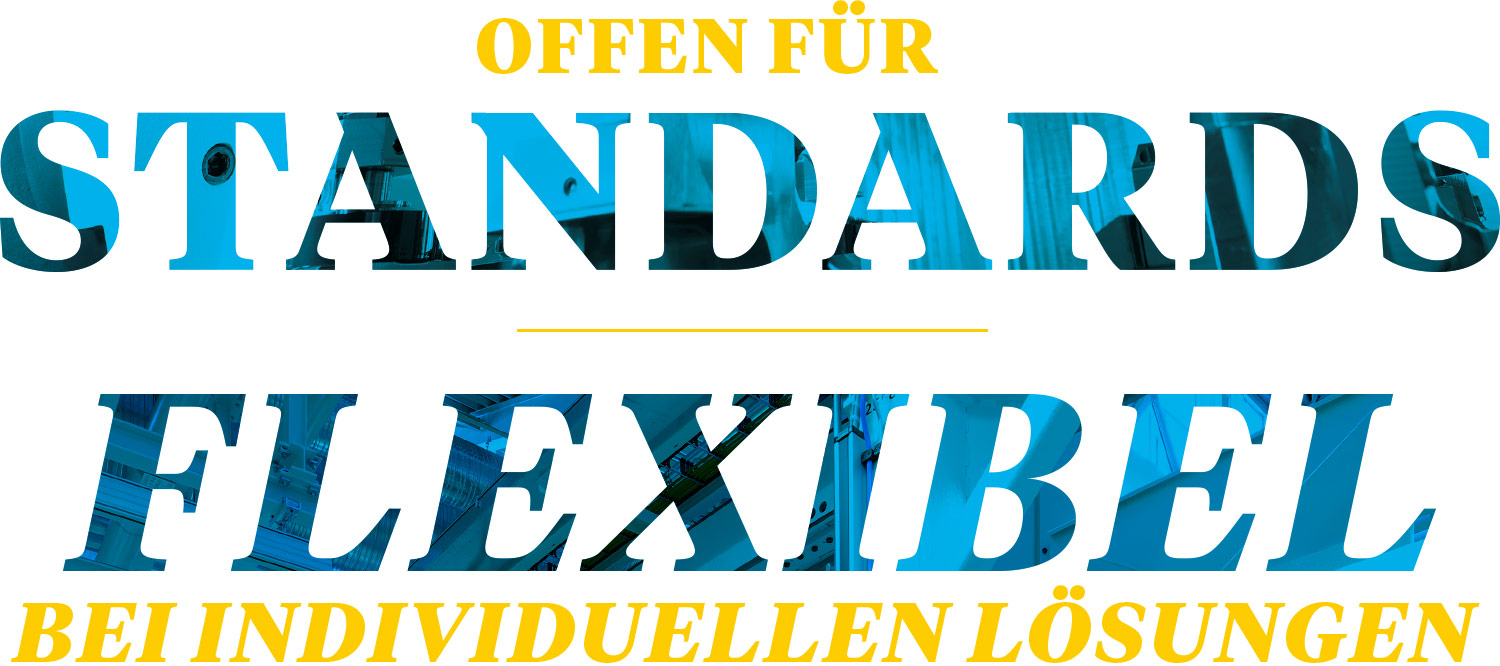
TEXT Manfred Lerch
FOTOS Jens Gelowicz, Manfred Lerch
Ob Beladung des Bearbeitungszentrums von oben, über Palettenautomation oder flexible Roboterzellen – der Weg in die Automation geht immer mit einer organisatorischen Neuausrichtung einher. Die häufigsten Fragen vor einem Invest in eine Automation orientieren sich deshalb zunächst meist daran, welche Möglichkeiten ein solches System bietet, wie groß es sein muss, um für die jeweilige Fertigung ausgelegt zu sein oder ob beabsichtigte Taktzeiten damit möglich sind, um schließlich die gewünschte Reduzierung der Stückkosten zu erreichen.
Um höchste Produktivität für eine signifikante Reduzierung unproduktiver Zeiten ging es bei der Daimler AG. Es standen agile Prozesse im Vordergrund, um damit flexibel auf veränderte Kundenanforderungen reagieren zu können. Im Bereich der Kurbelgehäuse-Fertigung von Verbrennungsmotoren sollten unterschiedliche Werkstückvarianten auf einer flexiblen agilen Fertigungslinie produziert werden. Bei den bestehenden Modulen standen noch bis zu acht HELLER Bearbeitungszentren unter einem Portallader. Das neue Projekt wurde mit vier Direktbeladungsmaschinen pro Portallader realisiert. Ziel dieser redundanten Systeme ist es, dass bei Stillstand eines Portalladers mit reduzierter Ausbringung weiterproduziert werden kann. Zudem stationierte HELLER vor jeder Maschine einen Adapterwechsler, der eine Entkopplung von Automation und Bearbeitungszentrum ermöglicht.
Die Roboterlösungen, ob stehend, fahrend oder kollaborierend
Um eine völlig andere automatisierte Fertigungslösung ging es bei der Samson AG, denn es sollten damit Schüttgut automatisiert und unterschiedliche Teilefamilien gefertigt werden. Entschieden hat man sich in Frankfurt für ein 4-Achs-Bearbeitungszentrum H 2000 von HELLER mit Roboterzelle. Obwohl es bei der H 2000 um ein Standard-Bearbeitungszentrum ging, bestand die Herausforderung darin, das Bauteil für zwei Operationen zu spannen und die Schnittstelle zum Roboter herzustellen. HELLER übernahm dafür die Generalverantwortung und sechs Monate später wurde damit die Serienproduktion gestartet.
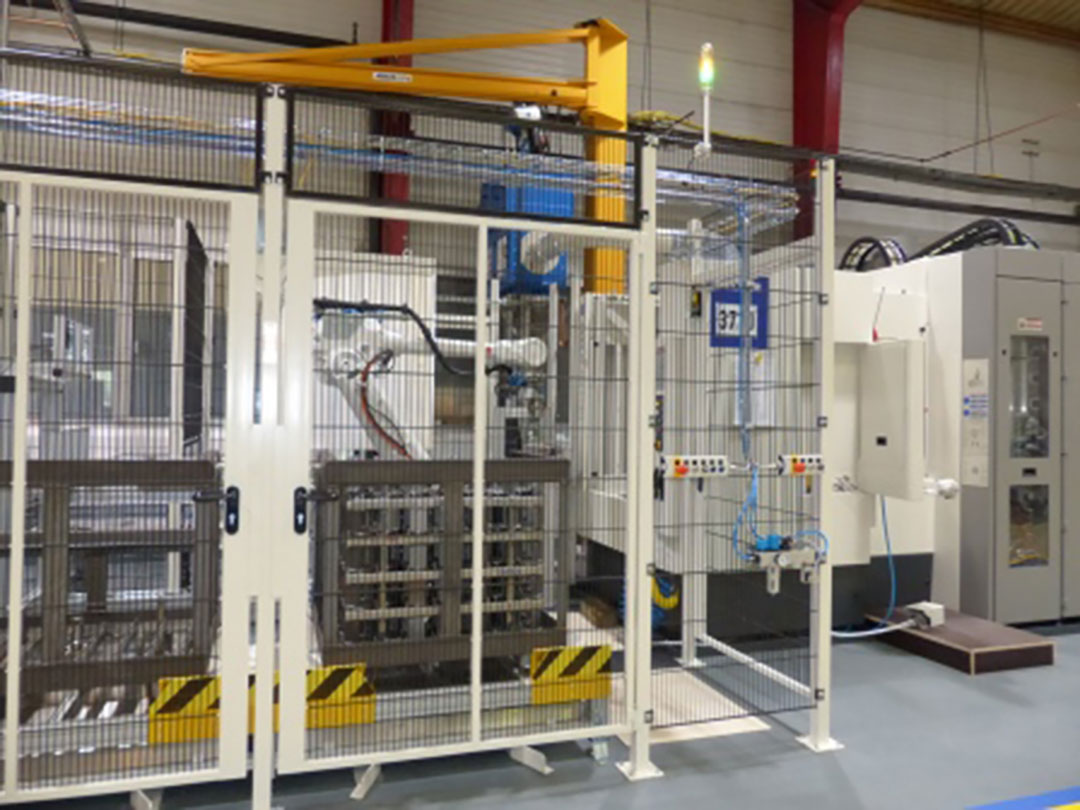
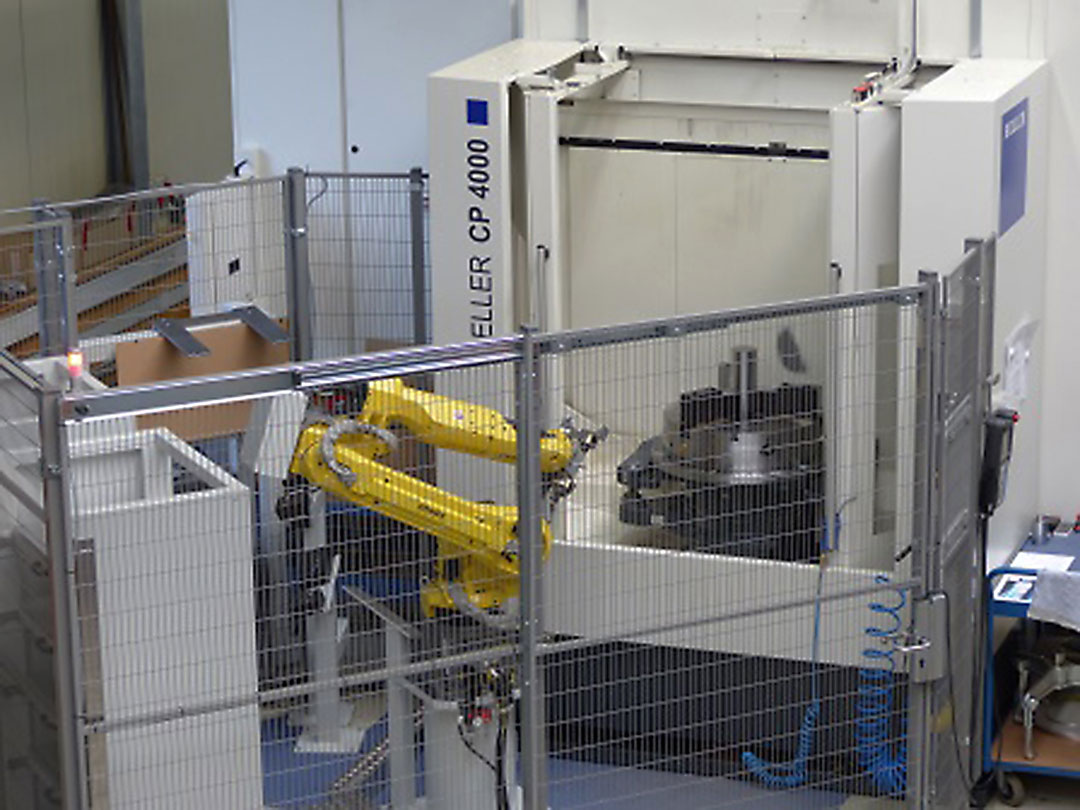
Beim Unternehmen Konstandin in Karlsbad dagegen war man sich bewusst, dass man für das neue 5-Achs-Fräs-Drehzentrum CP 4000 mit Palettenwechsler die Maschine allein mit großen Dreh-Bauteilen nicht auslasten kann. Deshalb haben sich die Verantwortlichen für eine Automatisierung mit einem Roboter entschieden – eine nachgerüstete Automatisierung, deren Anbindung aber über HELLER gestaltet wurde. Auch wenn man die Gründe für die neue definierte Flexibilität nicht allein in der Automation, sondern mit im produktiven Fräs-Drehzentrum CP 4000 sieht, hat diese Investition inzwischen zu enormen Zeiteinsparungen und zusätzlichen Kapazitäten geführt.
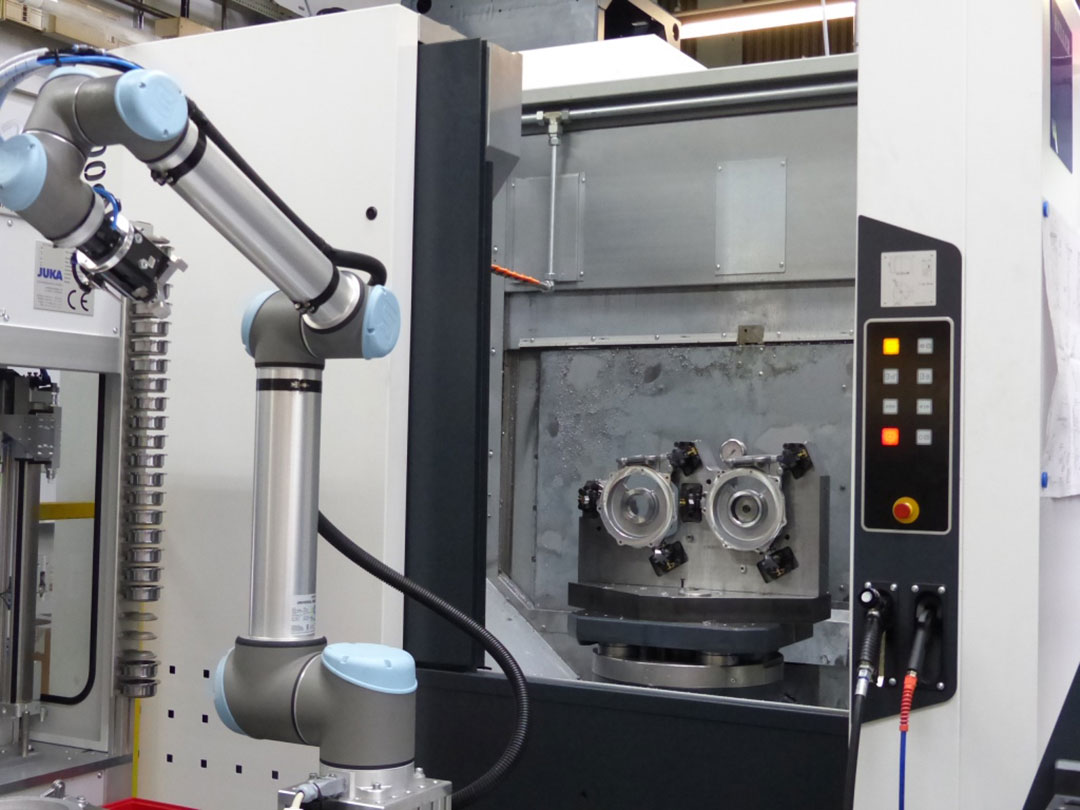
Eine Roboterlösung ist es auch bei der ZSO Zerspanungs- und Systemtechnik in Oberstaufen. Das Ziel war eine vollautomatisierte Zelle für ein großes Projekt, bei dem man sich noch in der Akquisitionsphase befand. Es ging um Bauteile aus Aluminiumguss mit einer Losgröße von einigen zehntausend Stück im Jahr für einen großen Automobilzulieferer. Allerdings sollte hier in einer voll automatisierten Zelle mit einem 5-Achs-Bearbeitungszentrum HF 3500 und einem kollaborierenden Roboter gefertigt werden. Das Werkstück wird fünfachsig in zwei Aufspannungen bearbeitet, zusätzlich wird eine Stahlbuchse mit Stickstoff zwischen den beiden Aufspannungen eingeschrumpft. Die Anlage ist mittlerweile komplett vernetzt, Zugriffe sind über Intranet und Internet möglich.
Zentraler Ansprechpartner mit Know-how in der Paletten-Automation
Rüstzeiten reduzieren und just in time für die Montage fertigen, das sind häufig Anforderungen, die zu einer Automation führen. Bei der Siemens AG in Ruhstorf war dafür zunächst ein einfacher Palettenspeicher als Lösung geplant. Entwickelt hat sich das Projekt dann zu einem Systemverbund mit drei Fräs-Drehzentren CP 2000 von HELLER und dem Multi-Level-System MLS-LD für insgesamt 72 Maschinenpaletten sowie zwei Hochgenauigkeits-Rüststationen. Das zentrale Paletten-Handling mit integrierten Be- und Entladestationen oder auch der dazugehörige Leitrechner mit der entsprechenden Software sorgen seither dafür, dass die Bediener speziell an den Rüst- und Ladestationen wissen, was als Nächstes zu tun ist. Die aktuellen Aufträge sind so bereits vor Produktionsbeginn in der Software hinterlegt, wobei die Software in diesem konkreten Fall über einen Zeitraum von drei Schichten vorausplant. Der Bediener erhält vor Schichtbeginn sämtliche relevanten Informationen über die gesamte Fertigungsplanung inklusive aller Rüstinformationen.
Bei Rohde & Schwarz im Werk Teisnach ist man ständig auf der Suche nach Innovationen sowie kürzeren Taktzeiten. Neben ca. 4.000 Teilen, die seit 30 Jahren immer wiederkehren, geht es aber auch um eine enorme Variantenvielfalt, die meist sehr kurzfristig verfügbar sein muss. Flexibilität, Durchgängigkeit und die Ausbringung haben deshalb in jeder Benchmark-Phase oberste Priorität, denn man will mit der Auftragsfertigung die Auslastungsschwankungen abfedern und weiter Know-how aufbauen. Um diesen Anforderungen weiter gerecht zu werden, hat man aktuell alle 4-Achs-Bearbeitungszentren H 2000 mit einer Container-Lösung mit jeweils 12 Paletten verkettet und fertigt im 3-Schicht-Betrieb, 24 Stunden, sechs Tage die Woche. Überwiegend geht es dabei um kubische Teile wie zum Beispiel High-Tech-Gehäuse aus Aluminium.
In der Summe wird HELLER so dem Wunsch der Anwender nach modernen Automatisierungslösungen für Bearbeitungszentren in allen Belangen gerecht. Die bedienarme Maschine oder der 8.760 Stunden/Jahr-Betrieb stehen für maximale Verfügbarkeit und Produktivität zur Senkung der Kosten pro Bauteil. Deshalb gibt es insbesondere im Bereich des Werkstück- bzw. Paletten-Handlings mittlerweile eine Reihe von Spezialisten am Markt, mit denen HELLER im Rahmen einer Best-in-Class-Partnerschaft zusammenarbeitet.
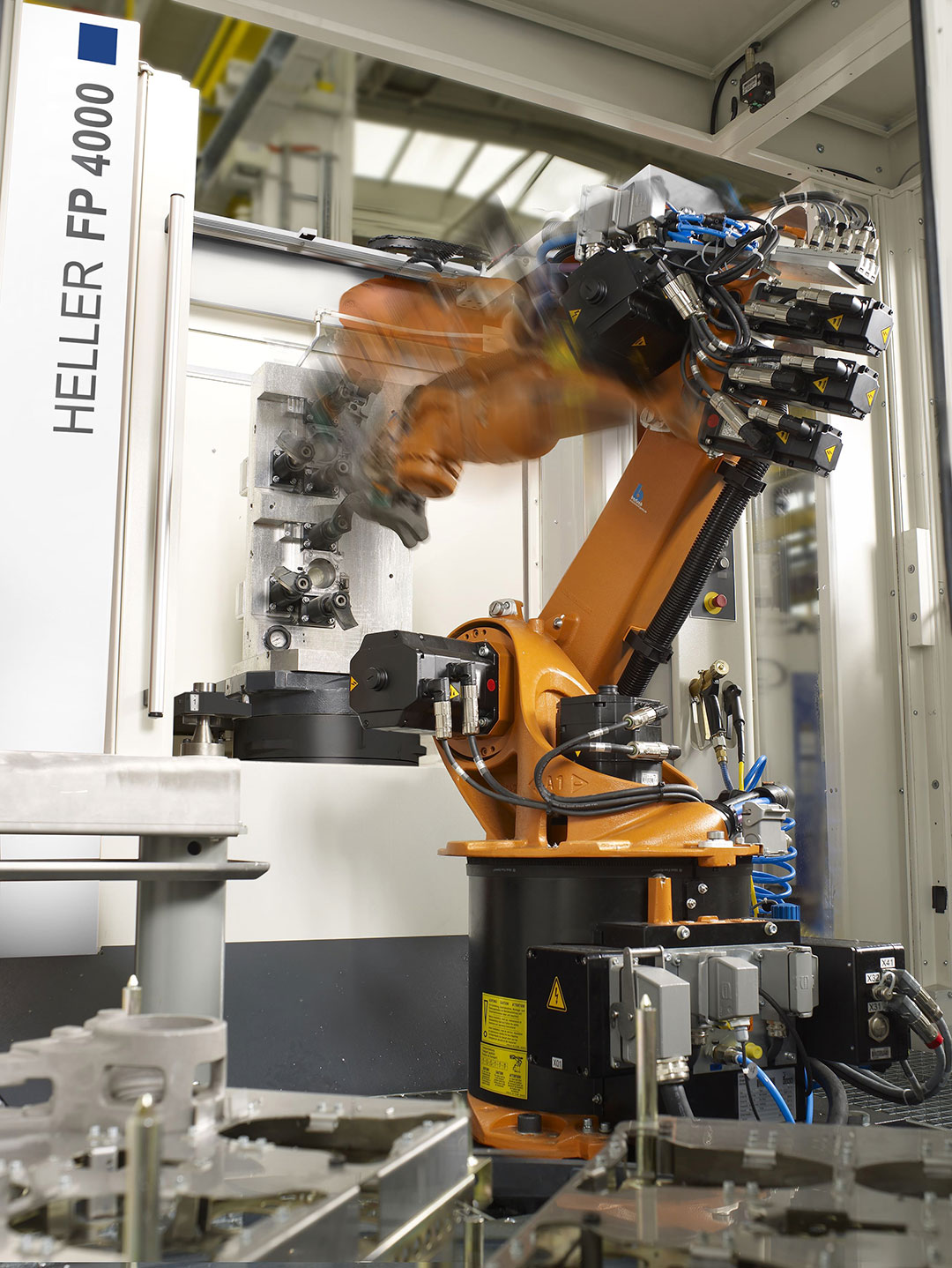
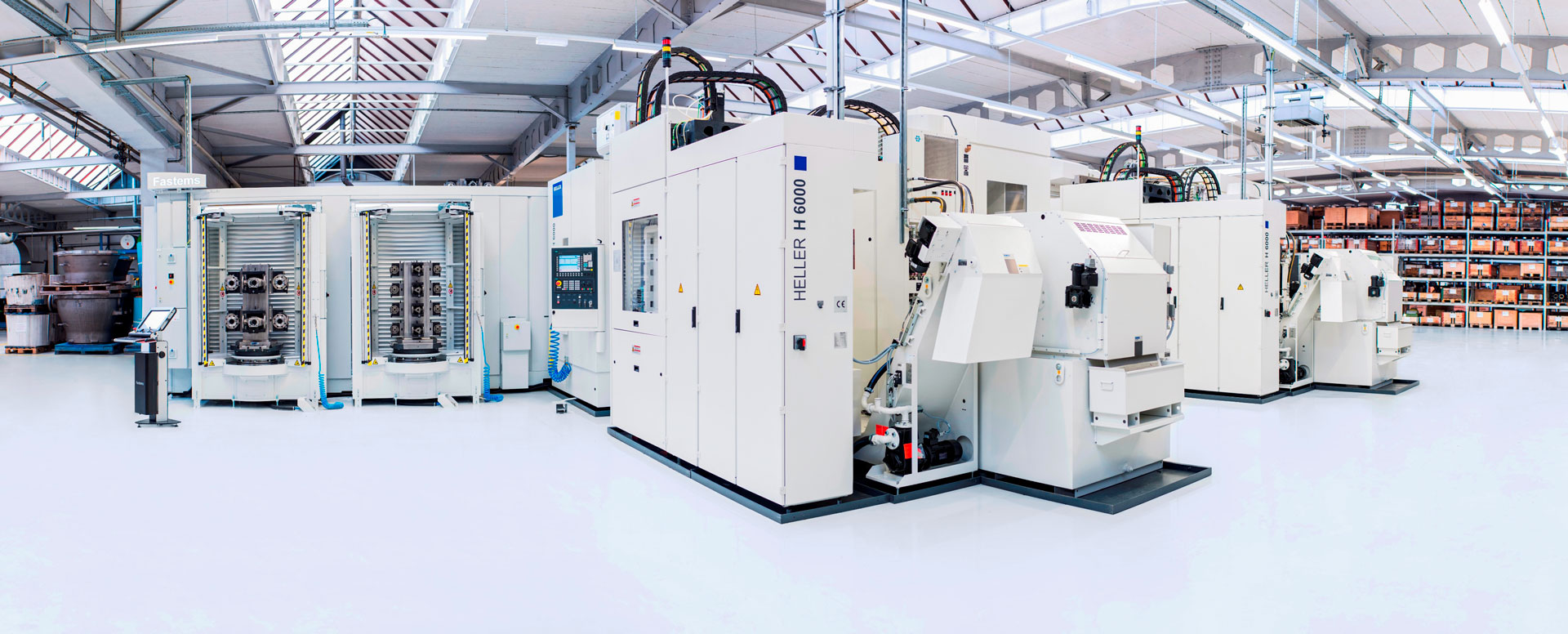