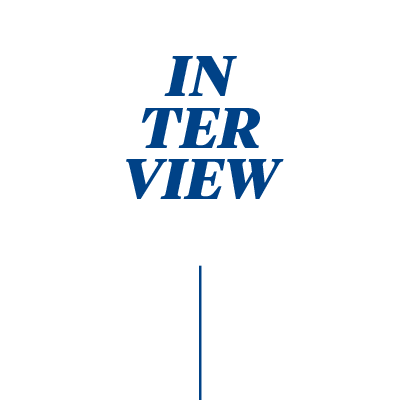
INTERVIEW Helmut Angeli FOTOS Tina Trumpp
Die Zukunft der Verbrennungsmotoren steht auf dem Prüfstand. Wer sich als Hersteller von Werkzeugmaschinen in der Vergangenheit vor allem auf das Umfeld Automotive konzentriert hat, muss umdenken. Bei der Gebr. Heller Maschinenfabrik GmbH hat dieses Umdenken, so Entwicklungschef Dr. Manuel Gerst, schon vor Jahren begonnen – und auch bereits zu neuen Lösungen geführt.
Es ist ja noch gar nicht allzu lange her, dass Sie zum Chef der Entwicklungsabteilung berufen wurden …
… ich bin 2018 zu HELLER gekommen und leite seit nunmehr einem knappen Jahr die Produktentwicklung.
Dann darf man auf Sie fast noch das gute alte Sprichwort „Neue Besen kehren gut“ anwenden. Wo haben Sie in Ihrer neuen Funktion den vordringlichsten Bedarf gesehen, einen neuen Weg einzuleiten?
Dazu eine Vorbemerkung: Die Angebotspalette von HELLER ist in den letzten Jahren durch die Entwicklung der Baureihen H respektive F und HF zu einer breit aufgestellten Produktrange geworden, die wirtschaftliche Lösungen für viele Unternehmen der Metallbearbeitung bietet. Wichtig war es daher zunächst, den erreichten Stand gemeinsam mit dem Vertrieb und der Applikation auf Herz und Nieren zu prüfen: Wo gibt es noch Performance-Lücken, wo müssen wir die Durchgängigkeit bestehender Lösungen weiter verbessern? Sicherlich hat uns dabei auch die Stärkung des Produktmanagements und seine enge Anbindung an den Entwicklungsbereich geholfen. Unsere Entwicklungs-Roadmap steht nun im Hause HELLER auf einer sehr stabilen und breiten Basis. Das ist die Voraussetzung dafür, dass Innovation gelingt und Produkte erfolgreich sind.
Aber ist es nicht so, dass sich durch das doch sehr schnelle Aufkommen der Elektromobilität manche Maschinenkonzepte überlebt haben? Vor allem, da sich HELLER in der Vergangenheit gerade in Bereichen einen Namen gemacht hat, die zukünftig an Bedeutung verlieren könnten?
Ich gehe davon aus, dass Sie hier auf das Spannungsfeld Projekt-/Flächengeschäft abzielen. Es ist natürlich nicht falsch, dass sich HELLER in der öffentlichen Wahrnehmung seit jeher weitgehend auch und vielleicht sogar vor allem im Projektgeschäft bewegt hat. Hier geht es darum, ganz konkrete Kundenforderungen in ein Fertigungssystem umzusetzen, und diese Aufgabenstellung haben wir hier in Nürtingen – das zeigt sich beispielhaft in den vielen Projekten, die wir gegen namhafte Wettbewerber gewonnen haben – bislang ganz ordentlich gelöst. Allein mit Engineering ist das aber nicht möglich. Was heißt, dass wir auch auf der Maschinenseite einiges zu bieten haben.
Ein gewisses Umdenken, und da kann ich Ihre Aussage nachvollziehen, besteht bei uns darin, dass wir unsere Maschinen mehr und mehr auch für ein anonymisiertes Umfeld bereitstellen. Das Pflichtenheft beschreibt dann nicht das kundenspezifische, sondern ein möglichst breit konfigurierbares System in einem oft ganz unterschiedlichen Umfeld. Konkret heißt das, einzelne Module noch weiter zu standardisieren, sodass wir Kundenanforderungen vermehrt aus einem smarten Baukasten bedienen können. Damit lassen sich nicht nur Kosten einsparen, sondern auch kürzere Lieferzeiten realisieren. Und, um nicht missverstanden zu werden: Diese Vorgabe ist im Hause HELLER nichts wirklich Neues, aber hat durch die Marktentwicklung der letzten Zeit deutlich an Gewicht gewonnen. Wir verwenden in der Entwicklung viel Know-how und Zeit dafür, eine echte Durchgängigkeit bei möglichst vielen peripheren Komponenten sicherzustellen. So soll ein Kunde, der eine 4-Achs-Maschine von uns im Einsatz hat und jetzt auf eine 5-Achs-Lösung setzt, möglichst viel seiner vorhandenen Peripherie und Betriebsmittel – zum Beispiel gleiche Paletten und Spannvorrichtungen, gleiche Automation – nutzen können.
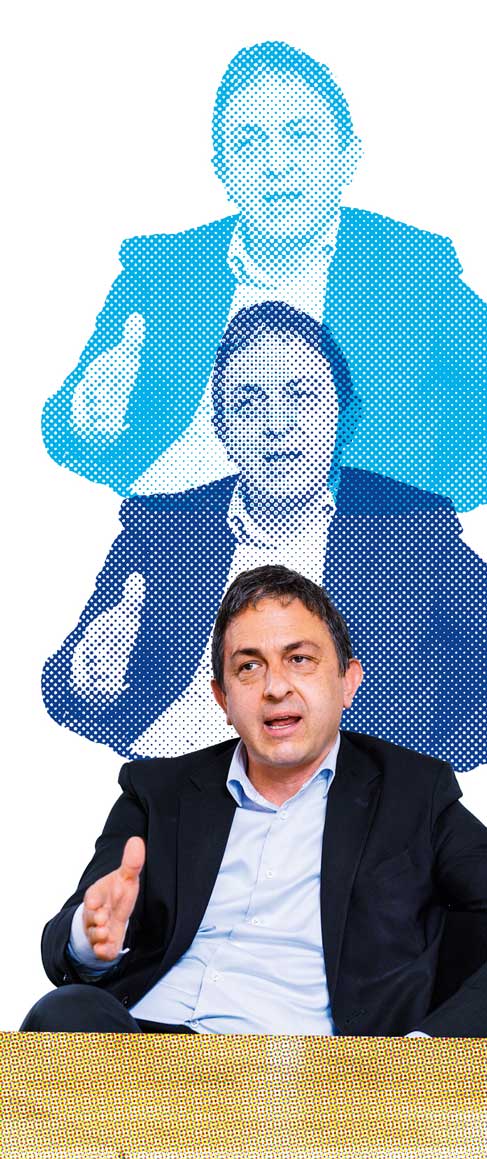
Das Know-How direkt an der Maschine ist durch nichts zu ersetzen
HELLER Maschinen sind vielfach ja nicht nur auf höhere Stückzahlen ausgelegt, sondern auch speziell für die Bearbeitung von Motorteilen. Deshalb nochmals die Frage: Müssten die Maschinenkonzepte denn nicht grundsätzlicher überarbeitet werden?
Unsere horizontalen Bearbeitungszentren können als echte Universalbearbeitungszentren keinem eingeschränkten Werkstückspektrum zugeordnet werden. Durch die schon angesprochene Modulbauweise lassen sie sich zudem exakt an die jeweiligen Bedürfnisse des Anwenders anpassen.
Gleichzeitig möchte ich aber feststellen, dass es für ein Unternehmen wie HELLER nicht das Ziel sein kann, „auf allen Hochzeiten zu tanzen“. Wir haben ganz spezifische Stärken und die daraus entstehenden Vorteile tragen wir in den Markt. Wenn man so will, kann man das als die HELLER Gene bezeichnen.
Wie würden Sie denn diese HELLER DNA umreißen?
Mit HELLER verknüpft die Branche sicherlich eine stabile Grundkonstruktion, Stichwort robuster Fahrständer, eine bemerkenswerte Langzeitgenauigkeit und Zuverlässigkeit sowie die hohe Produktivität.
Zurück zu der von Ihnen gebrauchten Begrifflichkeit „smarter Baukasten“: Der klingt ja sehr interessant, was hat man sich darunter konkret vorzustellen?
Wir haben das unter dem Motto „Innere Varianz verringern, äußere Varianz erhöhen“ zusammengefasst. Darunter verstehen wir alle Entwicklungen, die bei der Modularisierung und Standardisierung unserer Baugruppen von Bedeutung sind. Ein Beispiel: Wir haben Ende letzten Jahres eine neue Spindelgeneration eingeführt. Die HELLER Spindel Units (HSU) werden insgesamt in sechs Varianten durchgängig mit nur zwei Nullspindeln (HSK-A 63 und 100) ausgestattet. Diese Nullspindeln zeichnen sich durch einen schnellen Austausch sowie einen günstigen Preis aus und sind nun durchgängig sowohl für die 5-Achs-Baureihe HF wie auch für die 4-Achs-Maschinen der Baureihe H verfügbar. Dies bringt eine deutliche Vereinfachung und Kostenreduzierung für unsere Kunden mit sich. Wir arbeiten derzeit daran, einen ähnlich großen Schritt auch in den 5-Achs-Köpfen zu vollziehen. Dadurch können wir auch hier unserem Kunden trotz der internen Baugruppen-Standardisierung eine größere Angebotsvielfalt und damit nun auch im 5-Achs-Bereich die optimale Spindel für den jeweiligen Anwendungsfall bieten.
Trotzdem steht HELLER meiner Einschätzung nach nun einmal nicht für Einzelteil- und Kleinserienfertigung. Kann man das mit den skizzierten Aufgaben ändern?
Nur bedingt. Aber das ist nicht ausschließlich ein Nachteil. Wir sind es gewohnt, eine Maschine als Teil eines größeren Produktionsnetzwerkes zu sehen, und diese Voraussetzung findet man heute auch verstärkt bei kleinen und mittelständischen Unternehmen. Die Werkzeugmaschine wird mehr und mehr Teil einer komplexeren und größeren Einheit, die im Material-, aber auch Datenfluss vernetzt ist.
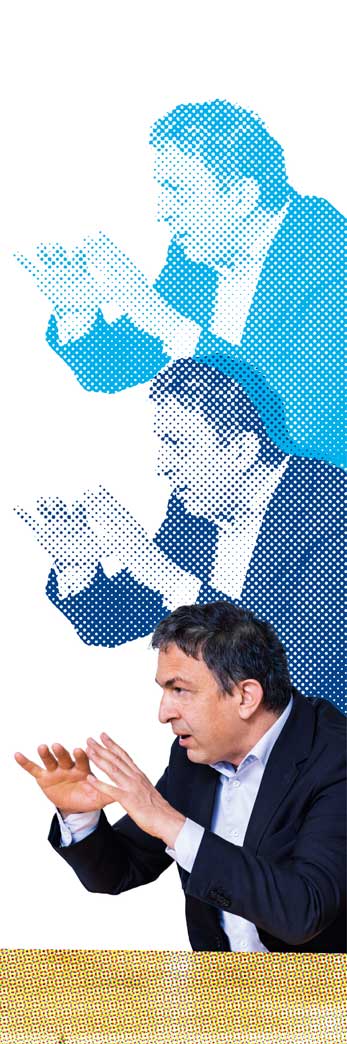
Stichwort Industrie 4.0: Ist die immer weiter fortschreitende Integration der Datenverarbeitung verbunden mit dem Trend zu einer durchgehenden Automatisierung nicht ein Hinweis, dass die Bedeutung der Mitarbeiterqualifikation und des Know-hows des Mitarbeiters direkt an der Maschine stark rückläufig ist? Verliert der Produktionsstandort Deutschland dadurch die Trumpfkarte seiner hochqualifizierten Mitarbeiter?
Know-how direkt an der Maschine ist in vielen Unternehmen inzwischen ein knappes Gut. Meiner Überzeugung nach ist es aber nicht zu ersetzen. Auch dann, wenn wir als Maschinenhersteller viel daransetzen, eine Maschine möglichst gut automatisierbar und einfach bedienbar zu machen. Dabei spielen Kenngrößen wie robuste Arbeitsgenauigkeit, Prozessstabilität, Zugänglichkeit bis hin zum Bedienkomfort und vielerlei Software-Unterstützung eine entscheidende Rolle. Dem Menschen soll ein Arbeitsumfeld geboten werden, das ihn unterstützt, ihn von einfachen operativen Aufgaben entlastet und ihm gleichzeitig die Möglichkeit offenlässt, sein Wissen und Können für Optimierungsaufgaben zu nutzen.
Bleiben wir doch noch beim Themenfeld Industrie 4.0. Viele der angeblichen Vorteile scheinen mir doch etwas weit hergeholt oder sind Elemente, die schon vor Jahrzehnten im Umfeld von Computer Integrated Manufacturing (CIM) diskutiert wurden. Gibt es bei HELLER schon marktreife Angebote an Anwender, die auch einen ganz konkreten Nutzen vorweisen?
HELLER bietet im Rahmen seiner HELLER4Industry-Stategie eine Reihe von einzelnen Modulen an, die ganz unbestritten einen hohen Nutzwert im Produktionsalltag aufweisen. Ein Beispiel ist das Modul HELLER Services Interface. Im Gegensatz zu bisherigen Servicemodellen, wo die Maschine in vorgegebenen Intervallen untersucht wird, werden bei dem HELLER Servicemodul alle relevanten Daten während des Betriebs laufend abgefragt und analysiert. Damit wird nicht nur der momentane Maschinenzustand erfasst, sondern es lassen sich aufgrund der Datenlage auch sehr genaue Prognosen erstellen, wann der Verschleiß der Schlüsselkomponenten sich auf die Bearbeitungsqualität auswirkt. Auf dieser Basis lassen sich zielgenaue Servicemaßnahmen optimal planen, um deren Auswirkung auf die laufende Produktion zu minimieren.
Unabhängig davon bleibt festzuhalten, dass die Anforderungen an die Maschinenbedienung gestiegen sind. Haben wir hier in Deutschland noch die richtigen Ausbildungskonzepte oder müsste sich auch hier etwas ändern?
Prinzipiell ist das duale Ausbildungssystem wohl immer noch der beste Weg, gute Fachkräfte zu bekommen. Zudem gibt es in vielen Firmen durchdachte Konzepte, wie zum Beispiel Lernfabriken, um Auszubildende noch besser und möglichst praxisnah auf ihre berufliche Tätigkeit vorzubereiten. Auch sind wir bei HELLER sehr froh, dass wir pro Jahr rund 30 Auszubildende bei uns am Standort haben. So decken wir einerseits den Bedarf in unserer hauseigenen mechanischen Fertigung, in der die Schlüsselkomponenten unserer Maschinen mit höchstem Anspruch an Genauigkeit gefertigt werden. Andererseits bilden wir so hochqualifizierte Anwendungstechniker aus, die anspruchsvollste Kundenprozesse ganz nach der HELLER Maxime „Wissen, wie es geht“ implementieren.
Wir wollen Kundenanforderungen vermehrt aus einem Baukasten bedienen
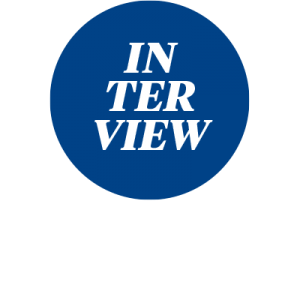